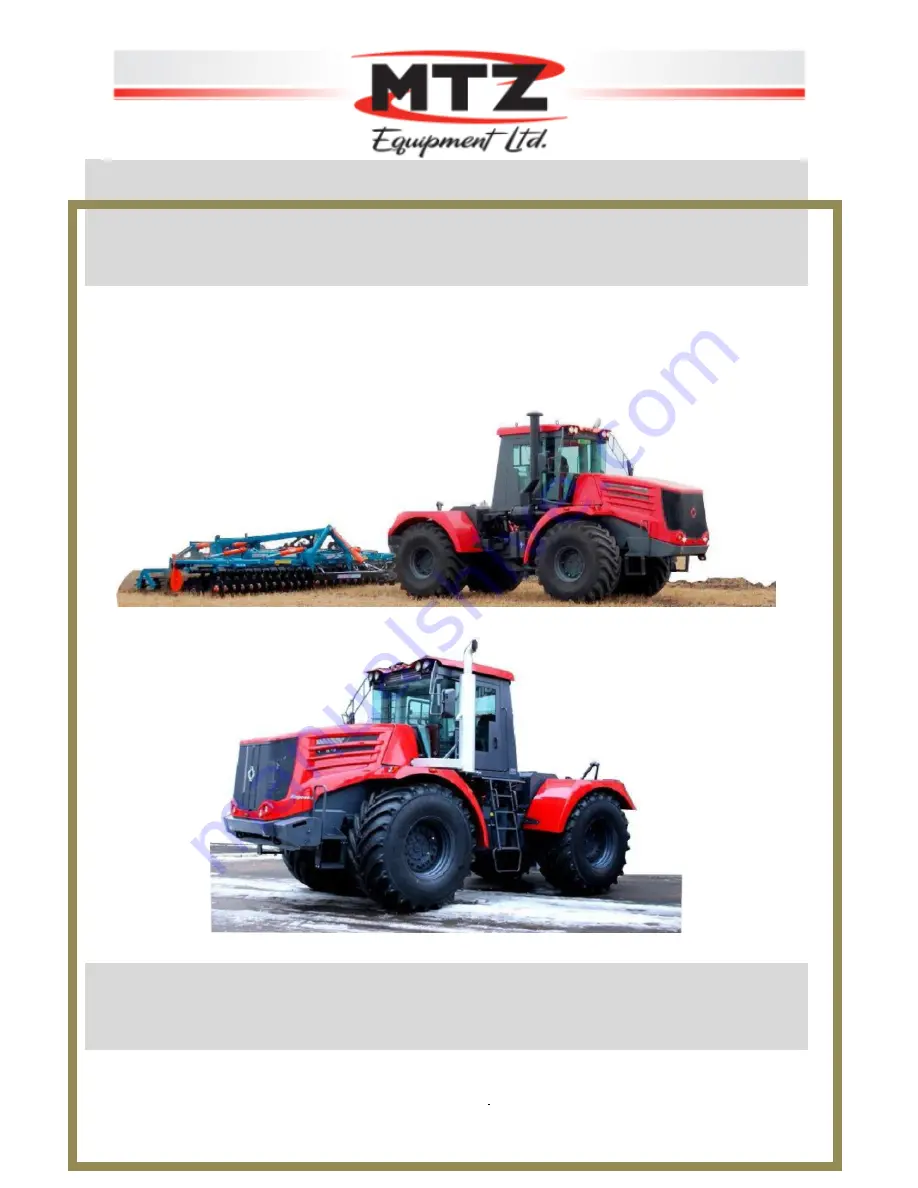
OPERATING
INSTRUCTION
744Р-0000010
MTZ-KIROVETS tractors K-744R1, K-744R2
K-744R3, K-744R4
Head Office:
3-1136 Centre St. Ste 124, Thornhill, ON, L4J 3M8, Canada
Warehouse:
2682 Highway 34, Hawkesbury, Ontario. K6A 2R2 Canada
Tel:
1-855-2GO-4MTZ (1-855-246-4689)
Fax:
1-647 933-9066
Web: