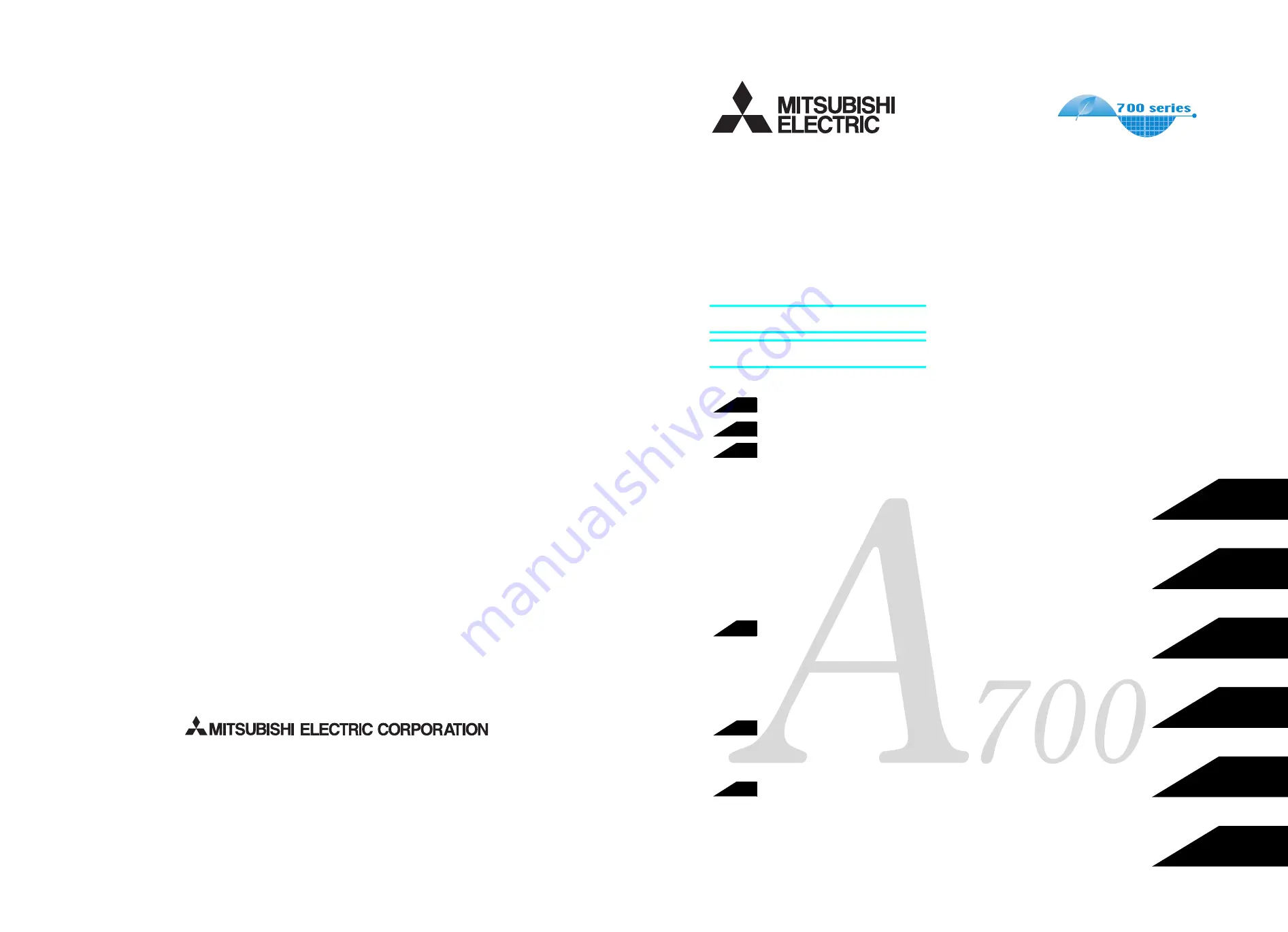
FR-A700-A1
INSTRUCTION MANUAL
INVERTER
HEAD OFFICE: TOKYO BUILDING 2-7-3, MARUNOUCHI, CHIYODA-KU, TOKYO 100-8310, JAPAN
1
2
3
4
5
6
CONTENTS
OUTLINE OF THE DEDICATED FUNCTIONS..............................................1
DANCER CONTROL/WINDING DIAMETER COMPENSATION ................14
Parameter setting procedure for dancer control function....................................... 19
3.10 Dedicated monitor function..................................................................................... 49
3.11 Regeneration avoidance function (Pr. 882)............................................................ 53
3.12 Operation command source and speed command source (Pr. 338, Pr. 339) ....... 53
TENSION CONTROL...................................................................................55
APPLICATION EXAMPLE...........................................................................67
Dancer control with winding diameter compensation for printers .......................... 67
Dancer control with winding diameter compensation for wiredrawing machine .... 70
Parameter change when replacing FR-A500-A1 with FR-A700-A1 ...................... 75
Control mode-based parameter (function) correspondence and
Dancer Control Function
Tension Control Function
IB(NA)-0600372ENG-C(1210)MEE Printed in Japan
Specifications subject to change without notice.