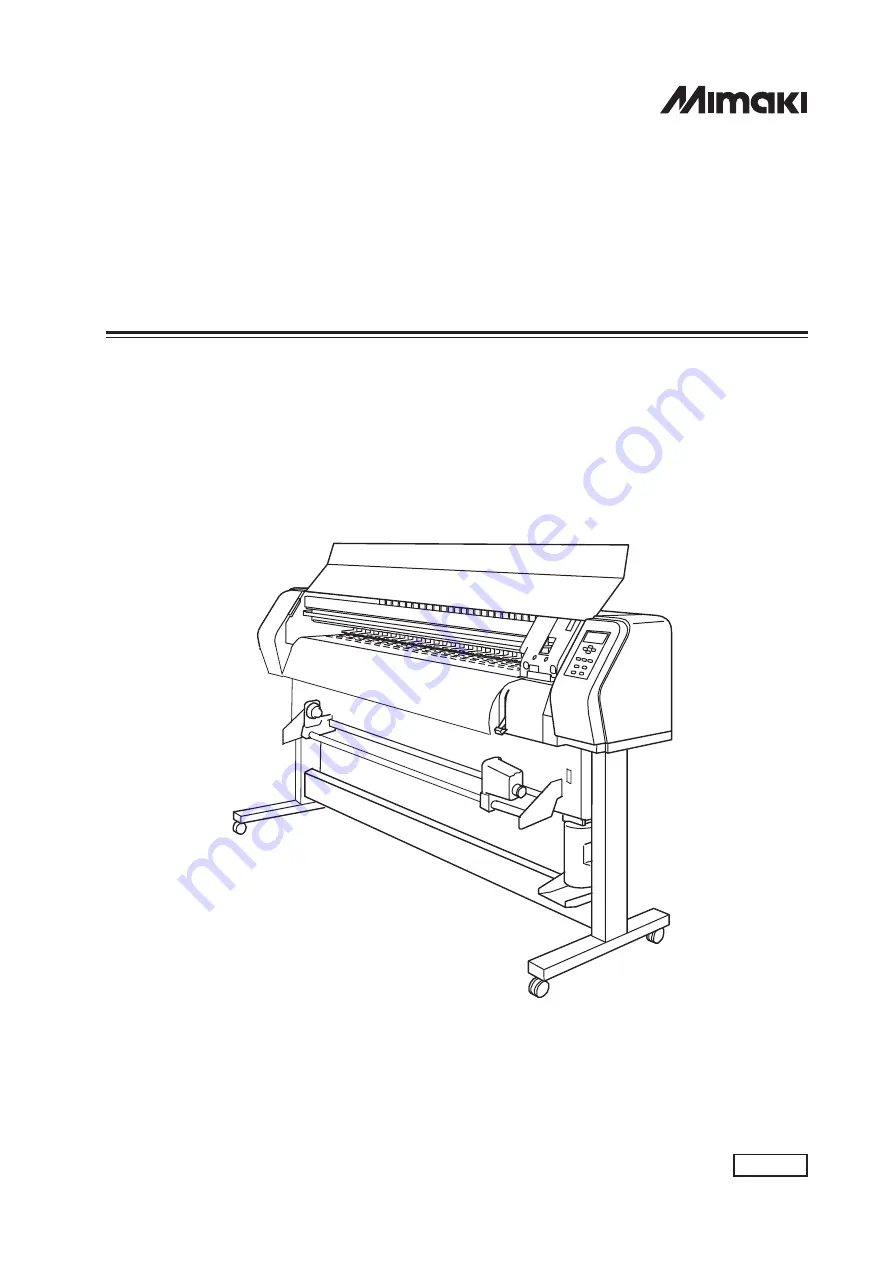
MIMAKI ENGINEERING CO., LTD.
TKB Gotenyama Building, 5-9-41, Kitashinagawa, Shinagawa-ku, Tokyo 141-0001, Japan
Phone: +81-3-5420-8671 Fax: +81-3-5420-8687
URL: http: // www.mimaki. co. jp /
E-mail: [email protected]
D201031
OPERATION MANUAL
JV22 Series
JV22-130
JV22-160
Summary of Contents for JV22-130
Page 2: ......
Page 34: ... 1 18 ...
Page 86: ... 4 14 ...
Page 120: ... A 6 ...
Page 125: ......
Page 126: ...PrintedinJapan D201031 MIMAKI ENGINEERING Co Ltd 2006 ...