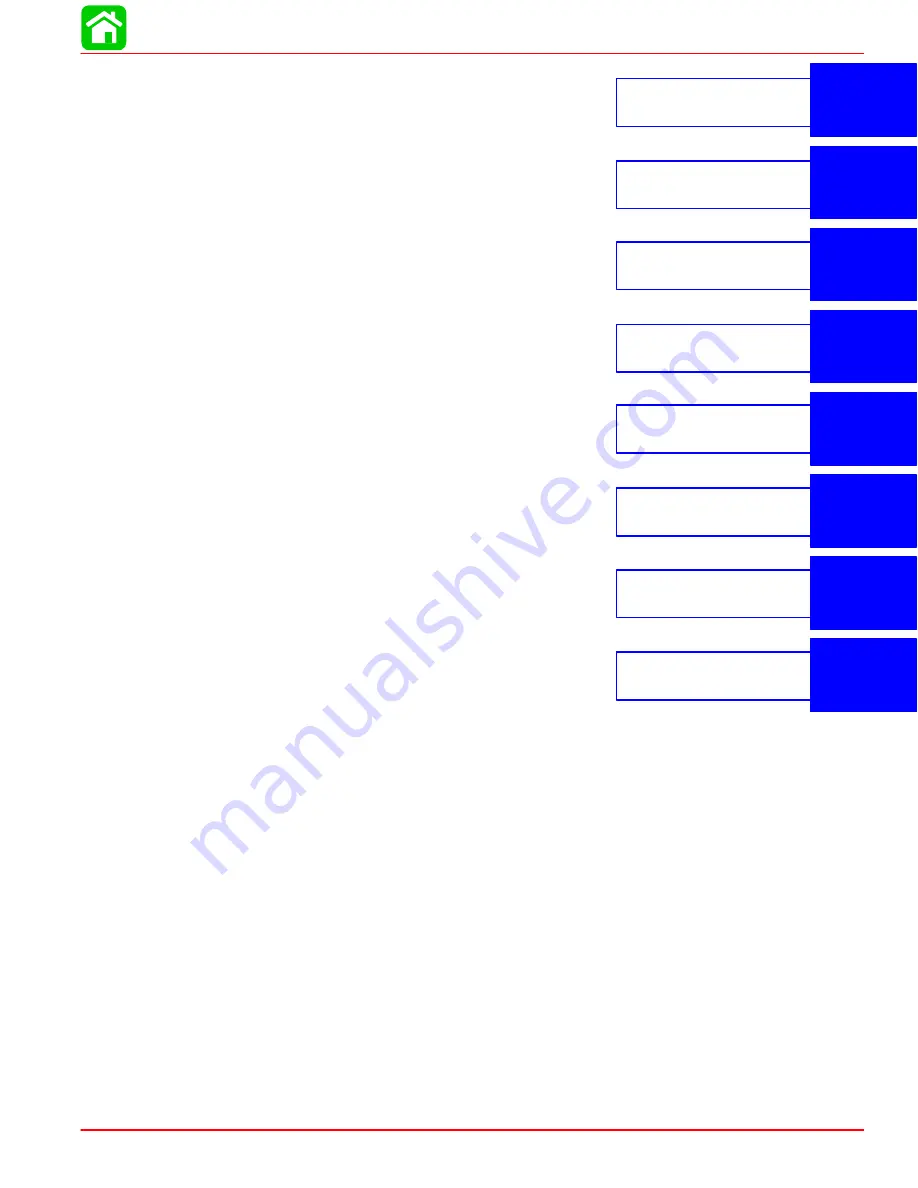
1
2
3
4
5
6
7
8
9
Important Information
Electrical
Fuel System
Powerhead
Mid-Section
Lower Unit
Attachment/Control Linkage
Manual Starter
90-826883R2 JUNE 1998
Page iii
Service Manual Outline
Section 1 - Important Information
A - Specifications
B - Maintenance
C - General Information
D - Outboard Installation
Section 2 - Electrical
A - Ignition
B - Charging & Starting System
C - Timing, Synchronizing & Adjusting
D - Wiring Diagrams
Section 3 - Fuel System
A - Carburetor/Fuel Pump
B - Emissions
Section 4 - Powerhead
Section 5 - Mid-Section
Section 6 - Lower Unit
A - Gear Housing
B - Jet Drive
Section 7 - Attachments/Control Linkage
A - Throttle/Shift Linkage
B - Tiller Handle
C - Side Shift
Section 8 - Manual Starter