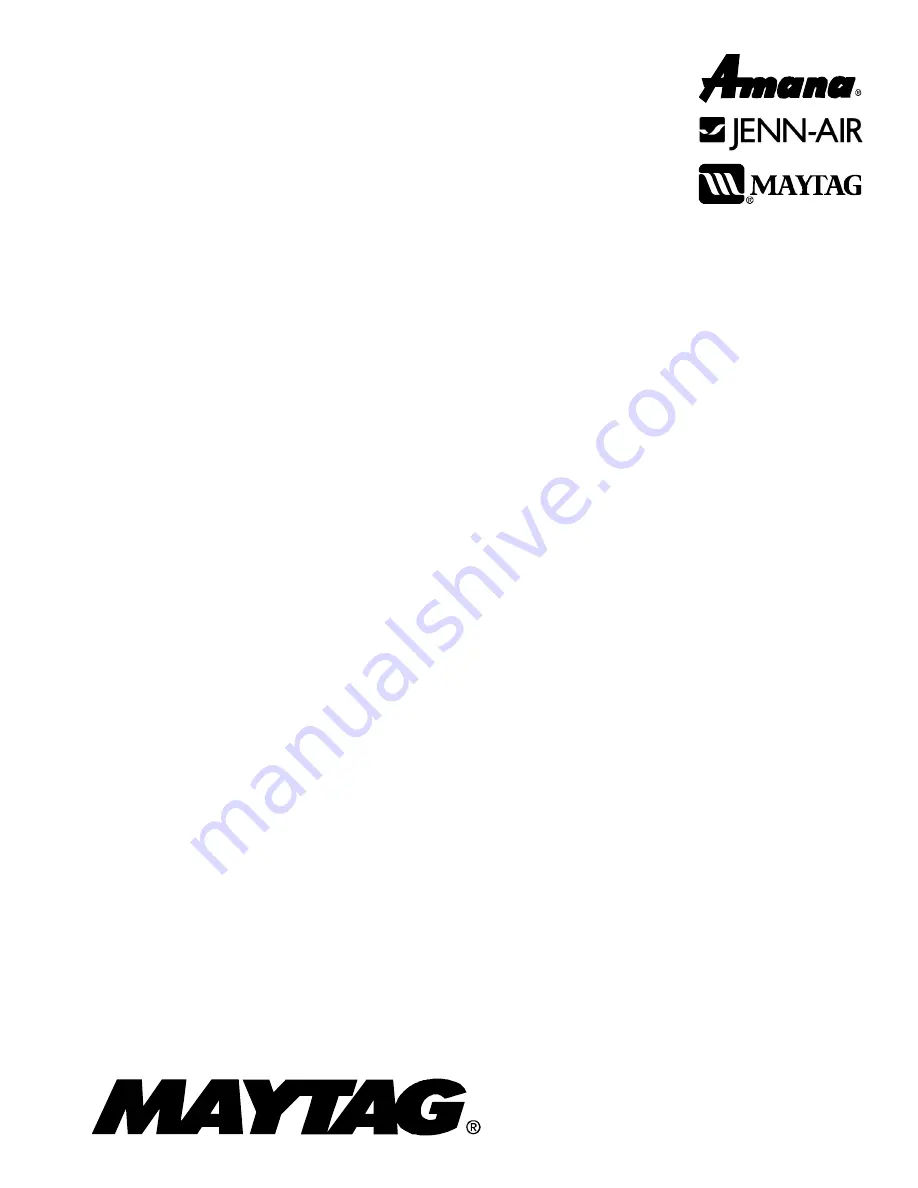
AGR5715QD*
AGR5735QD*
AGR5835QD*
JGR8775QD*
JGR8875QD*
MGR5754QD*
MGR5755QD*
MGR5765QD*
MGR5775QD*
MGR5875QD*
16022498
Revision 0
November 2003
Gas
Freestanding
Range
This Base Manual covers general information
Refer to individual Technical Sheet
for information on specific models
This manual includes, but is
not limited to the following:
Service
This manual is to be used by qualified appliance
technicians only. Maytag does not assume any
responsibility for property damage or personal
injury for improper service procedures done by
an unqualified person.