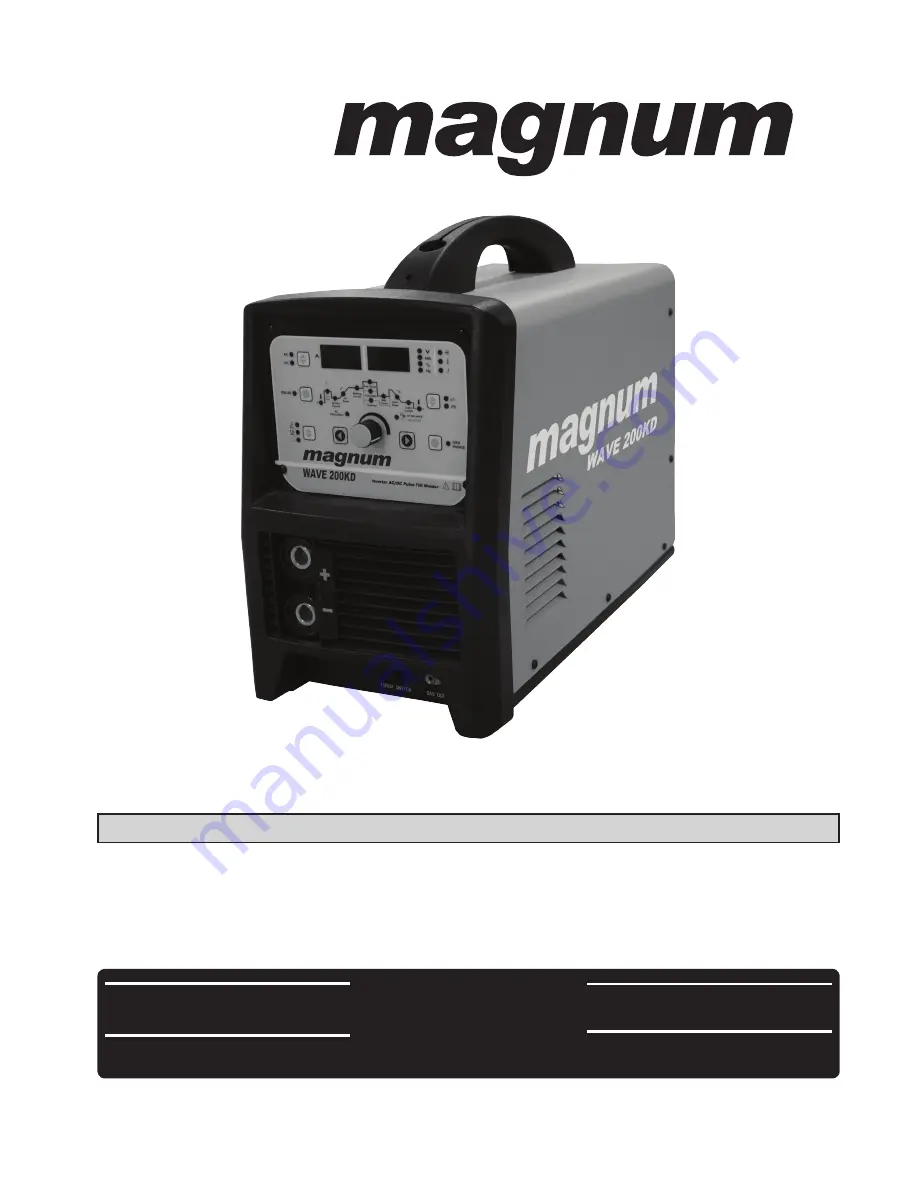
WE3107 v.110413
SAVE THIS MANUAL
You will need this manual for safety instructions, operating procedures, and warranty.
Put it and the original sales invoice in a safe, dry place for future reference.
CONSERVEZ CE GUIDE
Vous aurez besoin de ce guide pour les instructions de sécurité, les procédures d’utilisation et la garantie.
Conservez-le dans un endroit sûr et sec pour référence future.
QUESTIONS? 1-800-567-8979
Model:
Our Customer Service staff are ready to provide assistance.
If a part is damaged or missing, replacement parts can be
shipped from our facility.
For help with assembly, or for additional product
information, call our North American toll-free number:
1-800-567-8979
Notre personnel de service à la clientèle sera prêt à
fournir assistance. Si une pièce est endommagée ou
manquante, des remplacements seront expédiés de notre
usine.
Pour de l’aide avec l’assemblage, ou pour des
informations additionnelles sur le produit, appeller notre
numéro sans frais nord-américain : 1-800-567-8979
WAVE 200KD
AC/DC Pulse TIG/ARC Welder