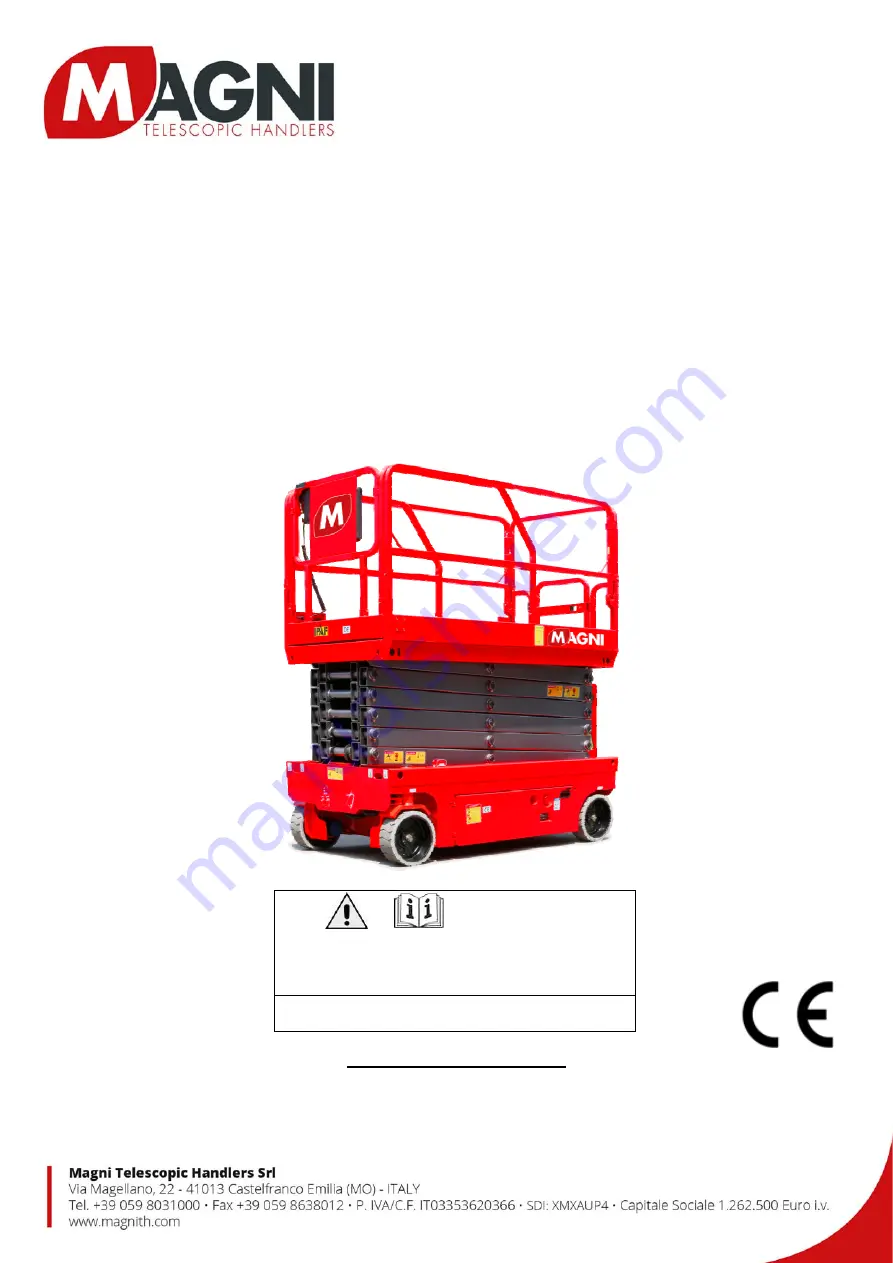
P.N.56622
.B
_EN
10/2020
‐‐
ORIGINAL
INSTRUCTIONS
‐‐
Drafted in accordance with the essential requirement of health and safety 1.7.4 of Annex I to Directive 2006/42 / EC
SELF-PROPELLED SCISSOR LIFTS
OPERATOR’S MANUAL
with Maintenance Information
(For ES0808H / ES1008H / ES0812H / ES1012H / ES1212H / ES1412H / ES1612HLB / ES1612HCP)
(For ES0808E / ES1008E / ES0812E / ES1012E / ES1212E / ES1412E / ES1612ELB / ES1612ECP)
( Hydraulic Motor / DC Motor Drive )
WARNING
THE MANIFACTURER SHALL NOT BE HELD LIABLE IN CASE OF
FAULTS OR ACCIDENTS DUE TO NEGLIGENCE, INCAPACITY,
INSTALLATION BY UNQUALIFIED TECHNICIANS AND IMPROPER USE
OF THE MACHINE.
DO NOT OPERATE THIS MACHINE UNTIL YOU READ AND
UNDERSTAND ALL THE DANGERS, WARNINGS AND CAUTIONS IN
THIS MANUAL.