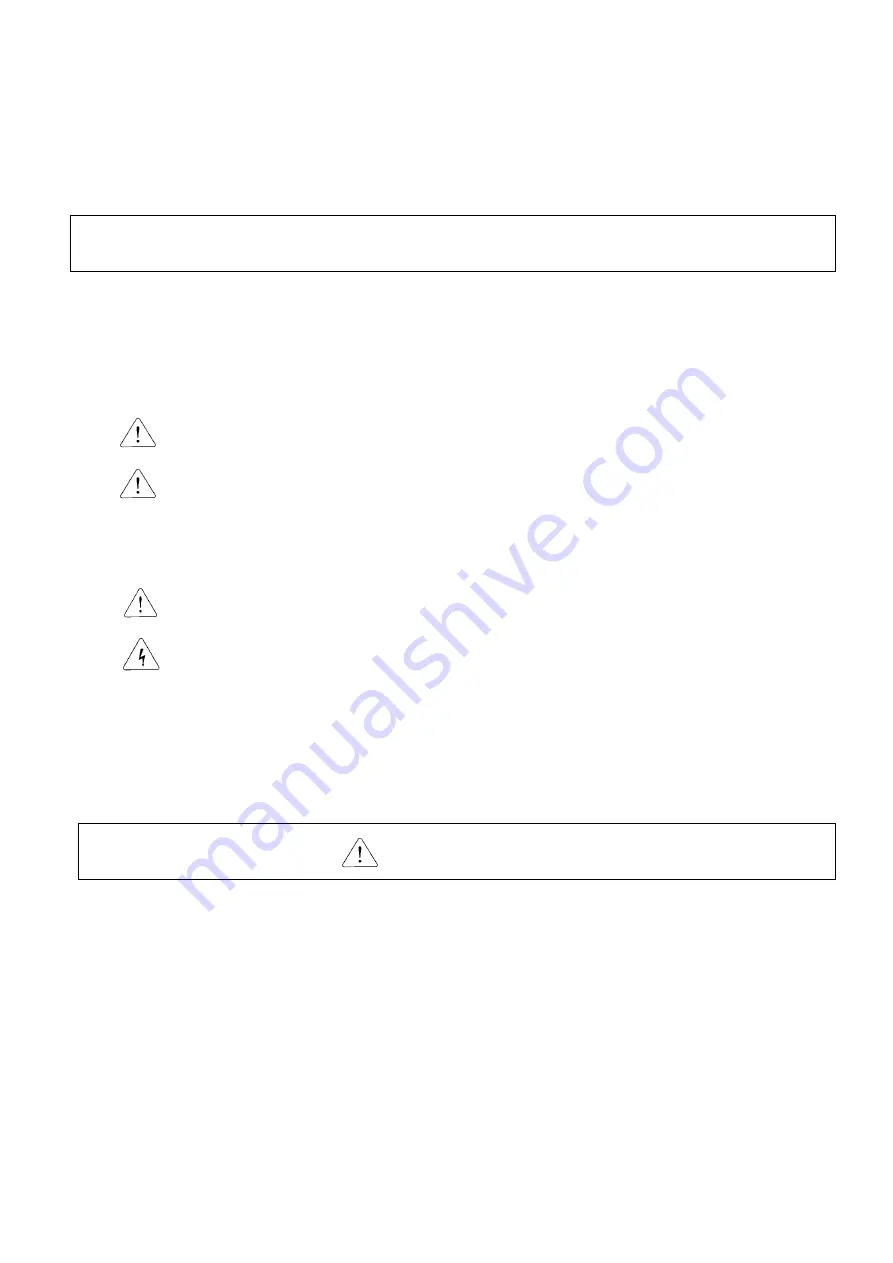
Before using the product, thank you for purchasing SV-iS7 CANopen option board.
SAFETY PRECAUTIONS
z
Always follow safety instructions to prevent accidents and potential hazards from occurring.
z
Safety precautions are classified into “WARNING” and “CAUTION” and their meanings are
as follows:
WARNING
CAUTION
z
The indicated illustrations on the product and in the manual have the following meanings.
Danger may be present. Read the message and follow the instructions carefully.
Particular attention should be paid because danger of an electric shock may be
present.
z
Keep operating instructions handy for quick reference.
z
Read the operating instructions carefully to fully understand the functions of the SV-iP5A
series and to use it properly.
CAUTION
z
Be cautious, when handling the CMOS components of the Option Board.
Static may lead to malfunctioning of the product.
z
Turn off the inverter power, when changing the communication cable.
Otherwise, you may damage the board or a communication error may occur.
z
Make sure to insert the Option Board connector to the inverter precisely.
Otherwise, you may damage the board or a communication error may occur.
z
Check the parameter unit before setting up the parameter.
Otherwise, a communication error may occur.
Improper operation may result in serious personal injury or
death.
Improper operation may result in slight to medium personal
injury or property damage.