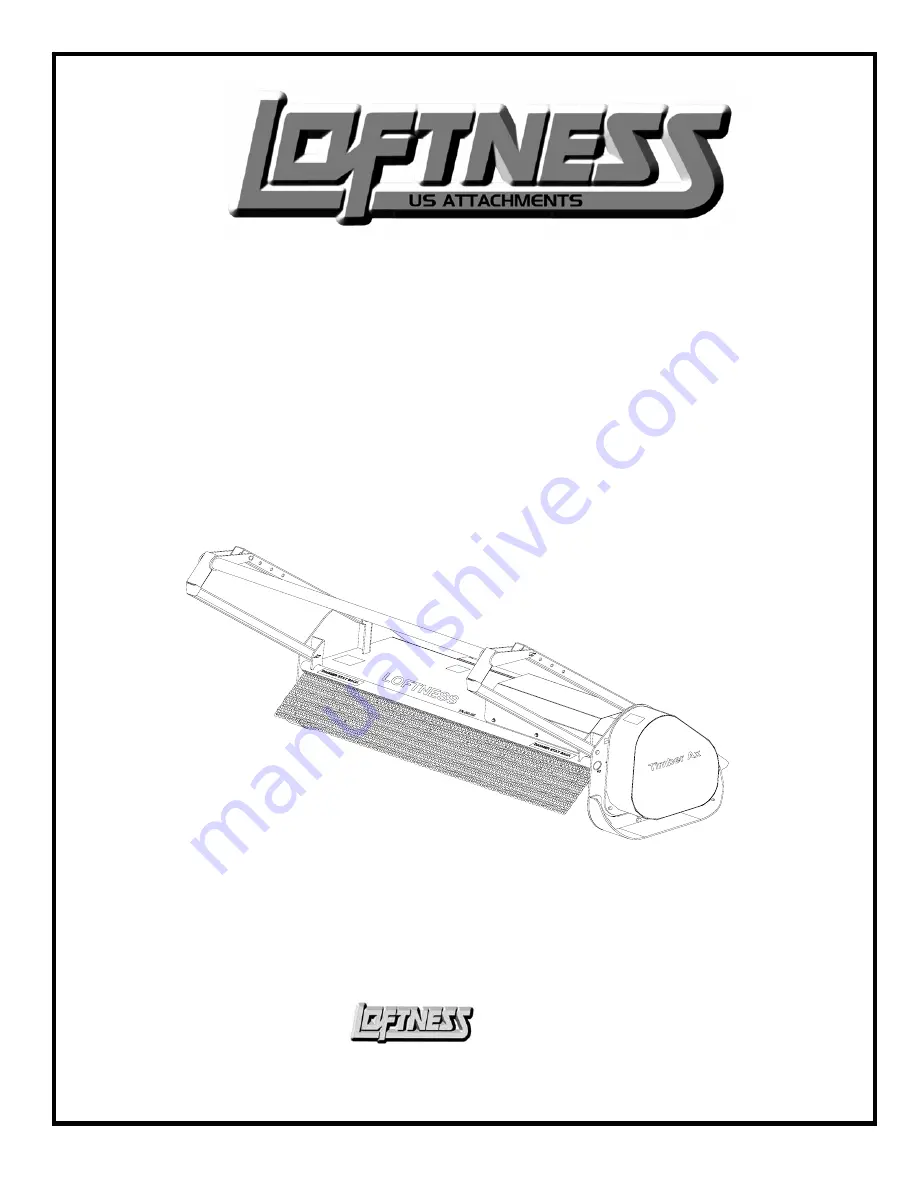
Timber Ax
Skid-steer Mounted Tree Shredder
43AXH 53AXH 63AXH 73AXH 83AXH
Operator’s Manual & Parts Book
(2004)
Model Number: _________________
Serial Number:
01-100 Thru 01-168
Date of Purchase: ________________
Specialized
Equipment, Inc.
650 So. Main Street - PO Box 337 - Hector, MN 55342
Business Phone: 320-848-6266 * Fax: 320-848-6269 * Toll Free: 1-800-828-7624
N14867 January, 2004
Summary of Contents for 43AXH
Page 5: ...Section 1 Safety ...
Page 11: ...Section 2 Operating ...
Page 15: ...Section 3 Maintenance ...
Page 16: ......
Page 23: ...Section 4 Service Parts ...
Page 24: ......
Page 27: ......
Page 28: ......
Page 29: ......
Page 30: ......
Page 31: ......
Page 32: ......
Page 33: ......
Page 34: ......
Page 35: ......
Page 36: ......
Page 37: ......
Page 38: ......