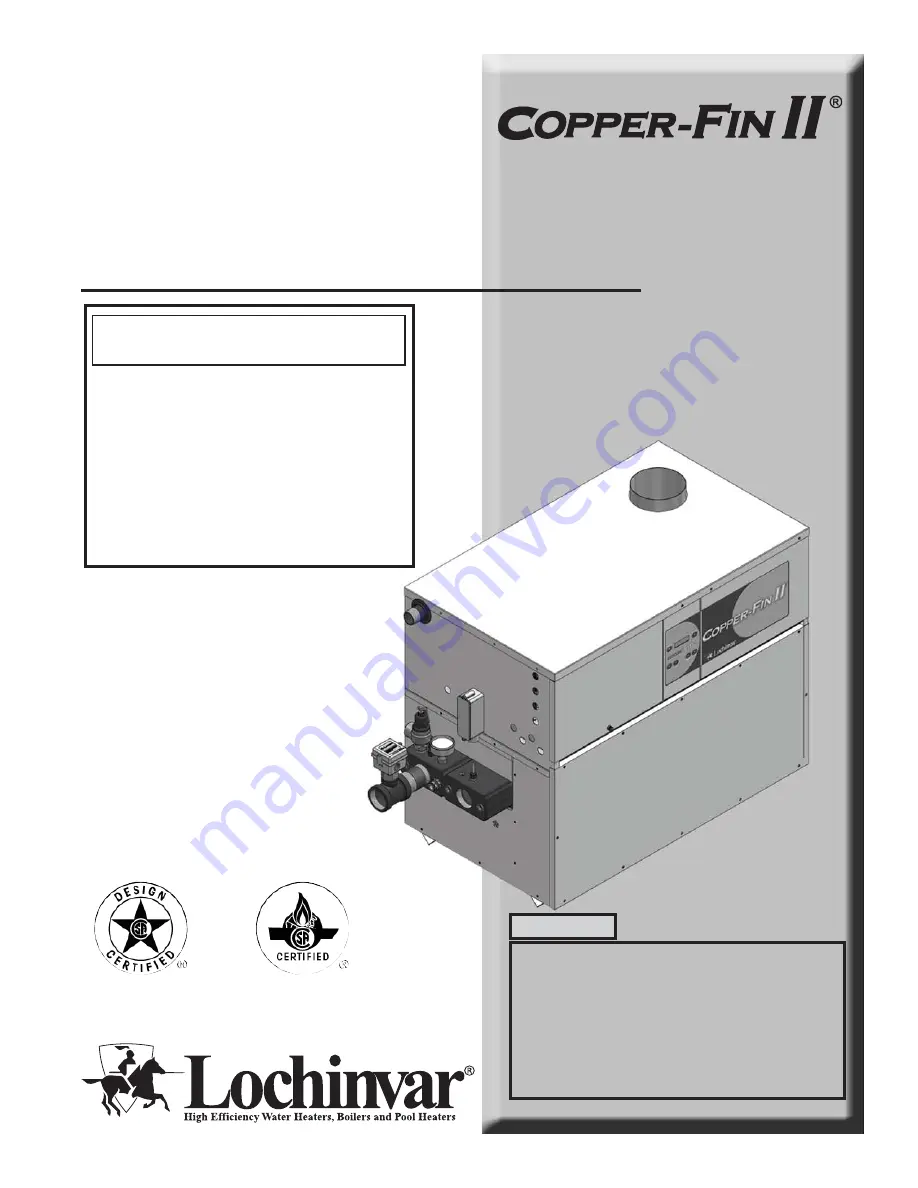
Installation & Operation Manual
Models: 402 - 2072
This manual supplies information for the
installation, operation, and servicing of the
appliance. It is strongly recommended that this
manual and the Copper-fin II Service Manual be
reviewed completely before proceeding with an
installation. Perform steps in the order given.
Failure to comply could result in severe personal
injury, death, or substantial property damage.
WARNING:
Save this manual for future reference.
CFX-CHX-I-O Rev A
-- Do not store or use gasoline or other flammable vapors and
liquids in the vicinity of this or any other appliance.
--
WHAT TO DO IF YOU SMELL GAS
• Do not try to light any appliance.
• Do not touch any electrical switch; do not use any phone in your
building.
• Immediately call your gas supplier from a near by phone.
Follow the gas supplier’s instructions.
• If you cannot reach your gas supplier, call the fire department.
-- Installation and service must be performed by a qualified
installer, service agency, or the gas supplier.
WARNING:
If the information in these instructions is not
followed exactly, a fire or explosion may result causing property
damage, personal injury or death.