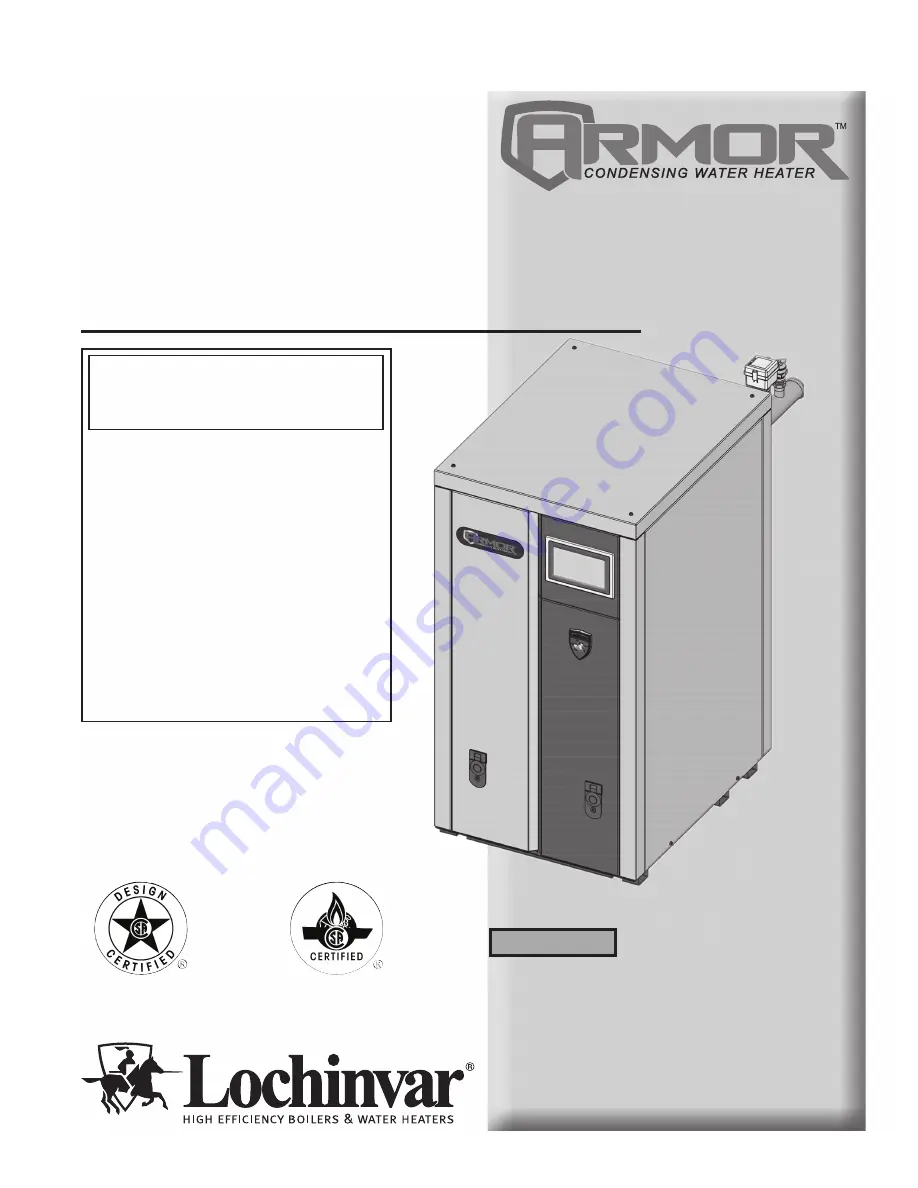
Installation & Operation
Manual
Models: 400 - 1000
Series 100 & 101
This manual must only be used by
a qualified heating installer / service
technician. Read all instructions,
including this manual and the
Armor Water Heater Service
Manual, before installing. Perform
steps in the order given. Failure
to comply could result in severe
personal injury, death, or substantial
property damage.
⚠
WARNING
Save this manual for future reference.
100331786_2000588637_Rev B
-- This water heater MUST NOT be installed in
any location where gasoline or flammable vapors
are likely to be present.
-- WHAT TO DO IF YOU SMELL GAS
• Do not try to light any appliance.
• Do not touch any electric switch; do not use any
phone in your building.
• Immediately call your gas supplier from a near by
phone. Follow the gas supplier’s instructions.
• If you cannot reach your gas supplier, call the fire
department.
• Installation and service must be performed by a
qualified installer, service agency, or the gas
supplier.
⚠
WARNING:
If the information in this
manual is not followed exactly, a fire or
explosion may result causing property damage,
personal injury or loss of life.