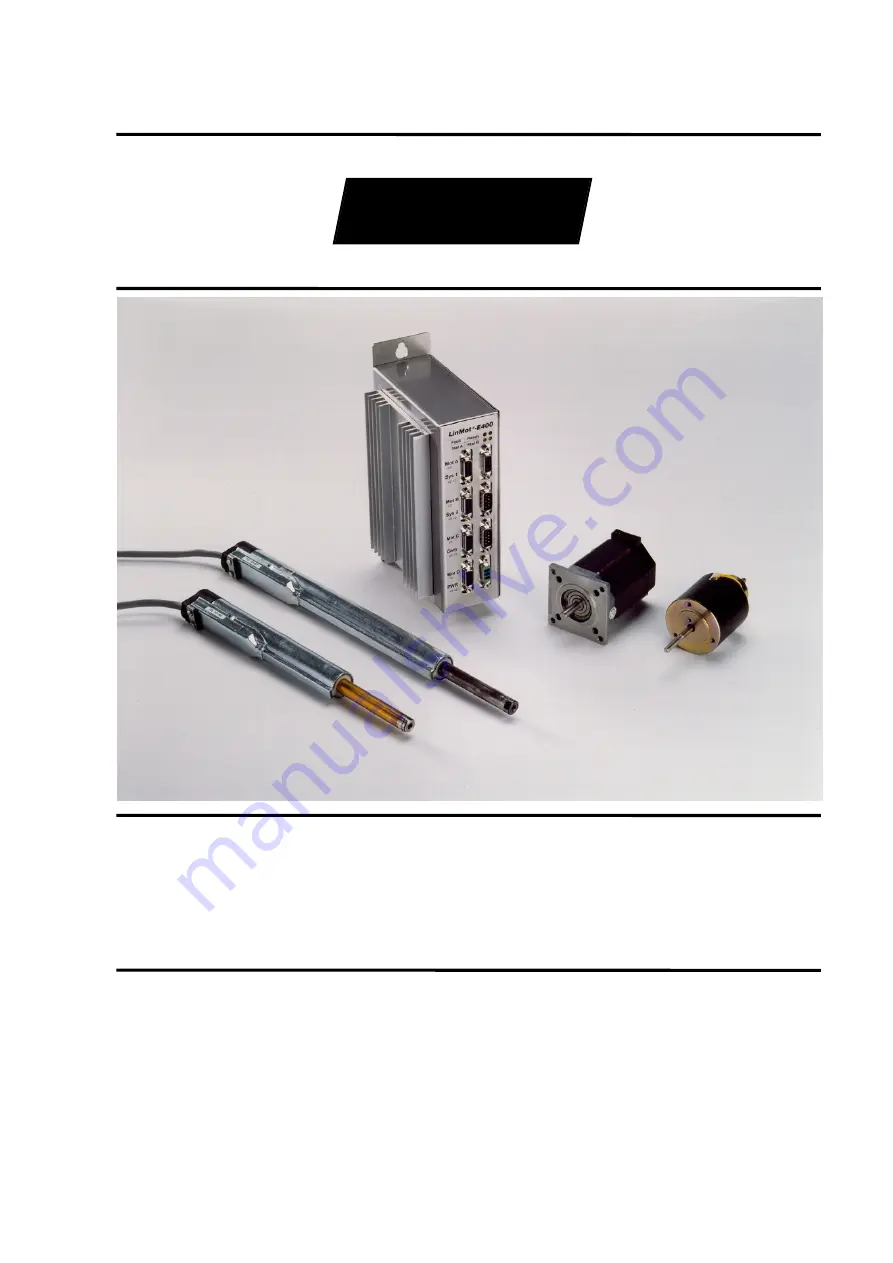
LinMot
User Manual
Rel. 1.0
Tel.: +41 (0)56 419 91 91
Fax: +41 (0)56 419 91 92
Email: [email protected]
Homepage: www.linmot.com
NTI AG
LinMot
Haerdlistrasse 15
CH-8957 Spreitenbach
LinMot
User Manual
Rel. 1.0
Tel.: +41 (0)56 419 91 91
Fax: +41 (0)56 419 91 92
Email: [email protected]
Homepage: www.linmot.com
NTI AG
LinMot
Haerdlistrasse 15
CH-8957 Spreitenbach