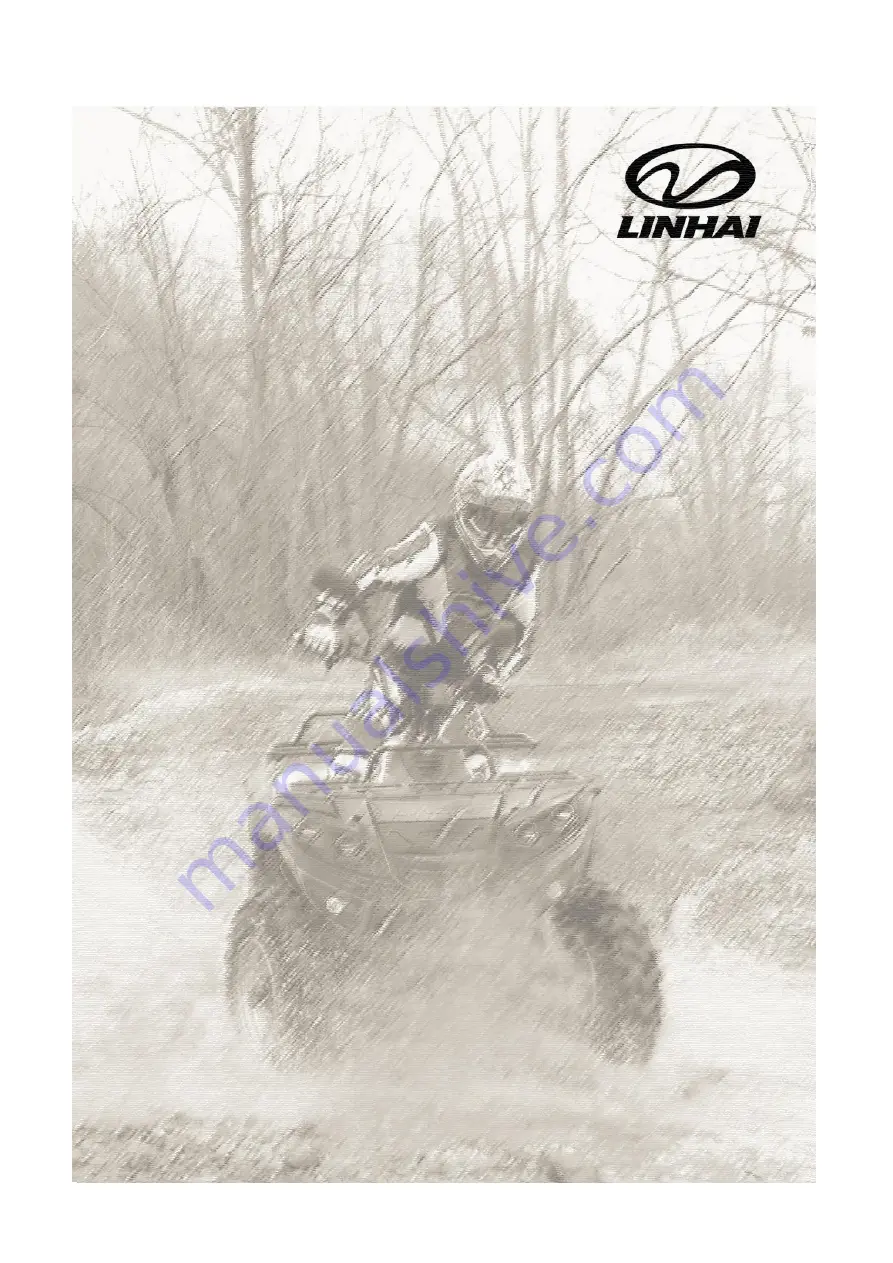
2020 ATV
SERVICE MANUAL
20.0
PN.
F010106A27
M565Li T3 EFI
WARNING
The parts of different types/ variants/ versions maybe un-interchangeable, even some parts
have almost same appearance. Always refer to Parts Manual of each ATV model for spare
parts information and service.
※
General Information
※
Maintenance
※
Engine
※
Chassis
※
Final Drive
※
Brakes
※
Electrical
Summary of Contents for M565Li T3 EFI
Page 2: ...ATV SERVICE MANUAL EUROPE 20 0 PN F010106A27 M565Li T3 EFI 20 0 F010106A27...
Page 33: ...CHAPTER 2 MAINTENANCE M565LiT3 EFI SERVICE MANUA 20 0 CHAPTER 2 MAINTENANCE PAGE 2 20 NOTES...
Page 34: ...CHAPTER 2 MAINTENANCE M565LiT3 EFI SERVICE MANUA 20 0 CHAPTER 2 MAINTENANCE PAGE 2 21...
Page 36: ...CHAPTER 3 ENGINE M565Li T3 EFI SERVICE MANUAL 20 0 3 1 Service information...
Page 51: ...CHAPTER 3 ENGINE M565Li T3 EFI SERVICE MANUAL 20 0 CHAPTER 3 ENGINE PAGE 3 14...
Page 65: ...CHAPTER 3 ENGINE M565Li T3 EFI SERVICE MANUAL 20 0...
Page 147: ...76 CHAPTER 3 ENGINE M565Li T3 EFI SERVICE MANUAL 20 0 CHAPTER 3 ENGINE PAGE 3...
Page 186: ...CHAPTER 3 ENGINE M565Li T3 EFI SERVICE MANUAL 20 0 CHAPTER 3 ENGINE PAGE 3 115...
Page 188: ...CHAPTER 3 ENGINE M565Li T3 EFI SERVICE MANUAL 20 0...
Page 203: ...CHAPTER 3 ENGINE M565Li T3 EFI SERVICE MANUAL 20 0 CHAPTER 3 ENGINE PAGE 3 104...
Page 210: ...CHAPTER 3 ENGINE M565Li T3 EFI SERVICE MANUAL 20 0...
Page 254: ...CHAPTER 4 CHASSIS M565Li T3 EFI SERVICE MANUAL 20 0 CHAPTER 4 CHASSIS PAGE 4 6 NOTES...
Page 290: ...CHAPTER 5 FINAL DRIVE LH500ATV D SERVICE MANUAL 14 0 CHAPTER 5 FINAL DRIVE 5 36 NOTES...
Page 304: ...CHAPTER 6 BRAKES M565Li T3 EFI SERVICE MANUAL 20 0 CHAPTER 6 BRAKES PAGE 6 14 NOTES...
Page 331: ...CHAPTER 8 ELECTRICAL M550 SERVICE MANUAL 16 0 CHAPTER 7 ELECTRICAL PAGE 7 27 Switch table...
Page 337: ...CHAPTER 8 ELECTRICAL M550 SERVICE MANUAL 16 0 CHAPTER 7 ELECTRICAL PAGE 7 33 7 13 WIRING DIAGR...
Page 338: ...CHAPTER 8 ELECTRICAL M550 SERVICE MANUAL 16 0 CHAPTER 7 ELECTRICAL CTRICAL PAGE 8 34...