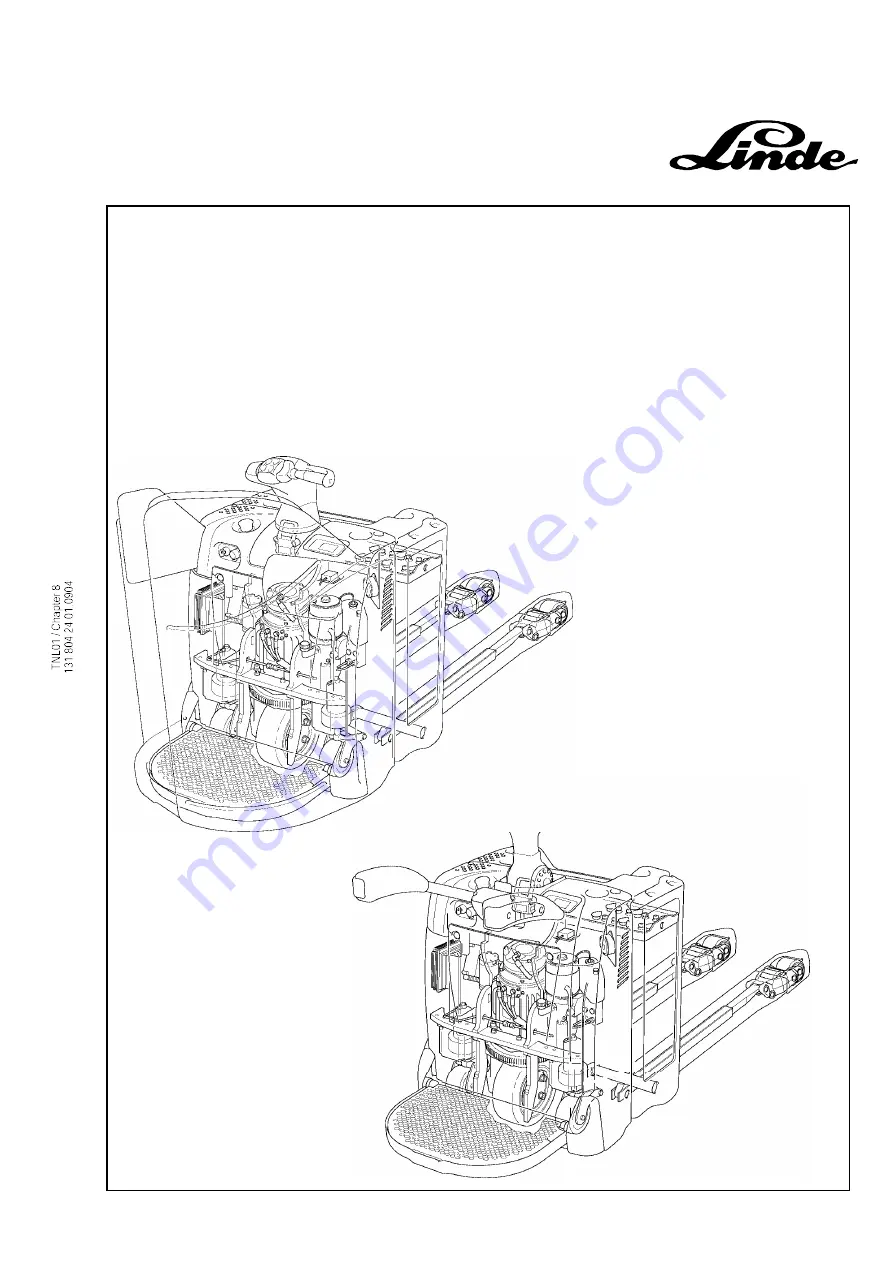
https://www.besttruckmanuals.com/
Summary of Contents for T20 AP
Page 1: ...https www besttruckmanuals com...
Page 2: ...https www besttruckmanuals com...
Page 3: ...https www besttruckmanuals com...
Page 4: ...https www besttruckmanuals com...
Page 5: ...https www besttruckmanuals com...
Page 6: ...https www besttruckmanuals com...
Page 7: ...https www besttruckmanuals com...
Page 8: ...https www besttruckmanuals com...
Page 9: ...https www besttruckmanuals com...
Page 10: ...https www besttruckmanuals com...
Page 11: ...Service Training Section 1 Page 1 1 TRACTIONMOTOR https www besttruckmanuals com...
Page 16: ...Service Training Section 1 P ge 6 https www besttruckmanuals com...
Page 17: ...Service Training Section 2 Page 1 2 DRIVE TRANSMISSION https www besttruckmanuals com...
Page 24: ...Service Training Section 2 Page 8 https www besttruckmanuals com...
Page 25: ...https www besttruckmanuals com...
Page 26: ...https www besttruckmanuals com...
Page 27: ...https www besttruckmanuals com...
Page 28: ...https www besttruckmanuals com...
Page 29: ...https www besttruckmanuals com...
Page 30: ...https www besttruckmanuals com...
Page 31: ...https www besttruckmanuals com...
Page 32: ...https www besttruckmanuals com...
Page 33: ...https www besttruckmanuals com...
Page 34: ...https www besttruckmanuals com...
Page 35: ...https www besttruckmanuals com...
Page 36: ...https www besttruckmanuals com...
Page 37: ...https www besttruckmanuals com...
Page 38: ...https www besttruckmanuals com...
Page 39: ...https www besttruckmanuals com...
Page 40: ...https www besttruckmanuals com...
Page 41: ...https www besttruckmanuals com...
Page 42: ...https www besttruckmanuals com...
Page 43: ...https www besttruckmanuals com...
Page 44: ...https www besttruckmanuals com...
Page 45: ...https www besttruckmanuals com...
Page 46: ...https www besttruckmanuals com...
Page 47: ...https www besttruckmanuals com...
Page 48: ...https www besttruckmanuals com...
Page 49: ...https www besttruckmanuals com...
Page 50: ...https www besttruckmanuals com...
Page 51: ...https www besttruckmanuals com...
Page 52: ...https www besttruckmanuals com...
Page 53: ...https www besttruckmanuals com...
Page 54: ...https www besttruckmanuals com...
Page 55: ...Section 6 Page 1 Service Training 6 ELECTRICALEQUIPMENT https www besttruckmanuals com...
Page 56: ...Service Training Section 6 Page 2 https www besttruckmanuals com...
Page 58: ...Service Training Section 6 Page 4 6 1 2 Electric plate https www besttruckmanuals com...
Page 93: ...Section 6 Page 39 Service Training 4 1V 4 1V 8 2V LES https www besttruckmanuals com...
Page 115: ...Service Training Section 6 Page 61 6 7 ELECTRICAL DIAGRAMS https www besttruckmanuals com...
Page 118: ...TNL01 Chapter 8 131 804 24 01 0904 https www besttruckmanuals com...
Page 120: ...TNL01 Chapter 8 131 804 24 01 0904 https www besttruckmanuals com...
Page 121: ...https www besttruckmanuals com...
Page 122: ...https www besttruckmanuals com...
Page 124: ...TNL01 Chapter 8 131 804 24 01 0904 https www besttruckmanuals com...
Page 125: ...https www besttruckmanuals com...
Page 126: ...https www besttruckmanuals com...
Page 127: ...https www besttruckmanuals com...
Page 128: ...https www besttruckmanuals com...
Page 129: ...https www besttruckmanuals com...
Page 130: ...https www besttruckmanuals com...
Page 131: ...https www besttruckmanuals com...
Page 132: ...https www besttruckmanuals com...
Page 133: ...https www besttruckmanuals com...
Page 134: ...https www besttruckmanuals com...