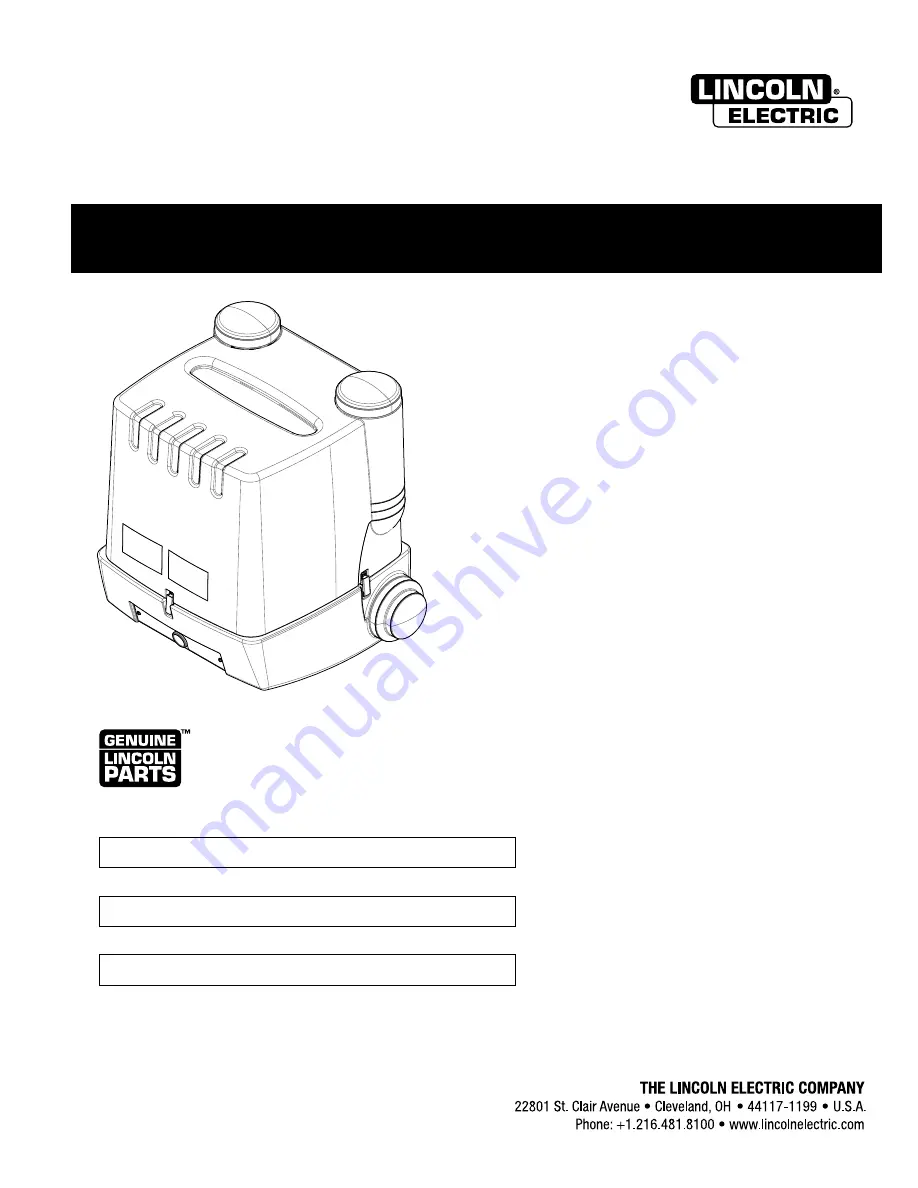
Statiflex
®
200-M
Register your machine:
www.lincolnelectric.com/register
Authorized Service and Distributor Locator:
www.lincolnelectric.com/locator
IM10348
| Issue D ate
Dec-16
© Lincoln Global, Inc. All Rights Reserved.
For use with machines having Product Numbers:
K1654-4 - Single Arm Base Unit
K1654-5 - Dual Arm Base Unit
K1654-6 - High Efficiency Single Arm
Base Unit
Save for future reference
Date Purchased
Code: (ex: 10859)
Serial: (ex: U1060512345)
Operator’s Manual
Need Help? Call 1.888.935.3877
to talk to a Service Representative
Hours of Operation:
8:00 AM to 6:00 PM (ET) Mon. thru Fri.
After hours?
Use “Ask the Experts” at lincolnelectric.com
A Lincoln Service Representative will contact you
no later than the following business day.
For Service outside the USA:
Email: [email protected]