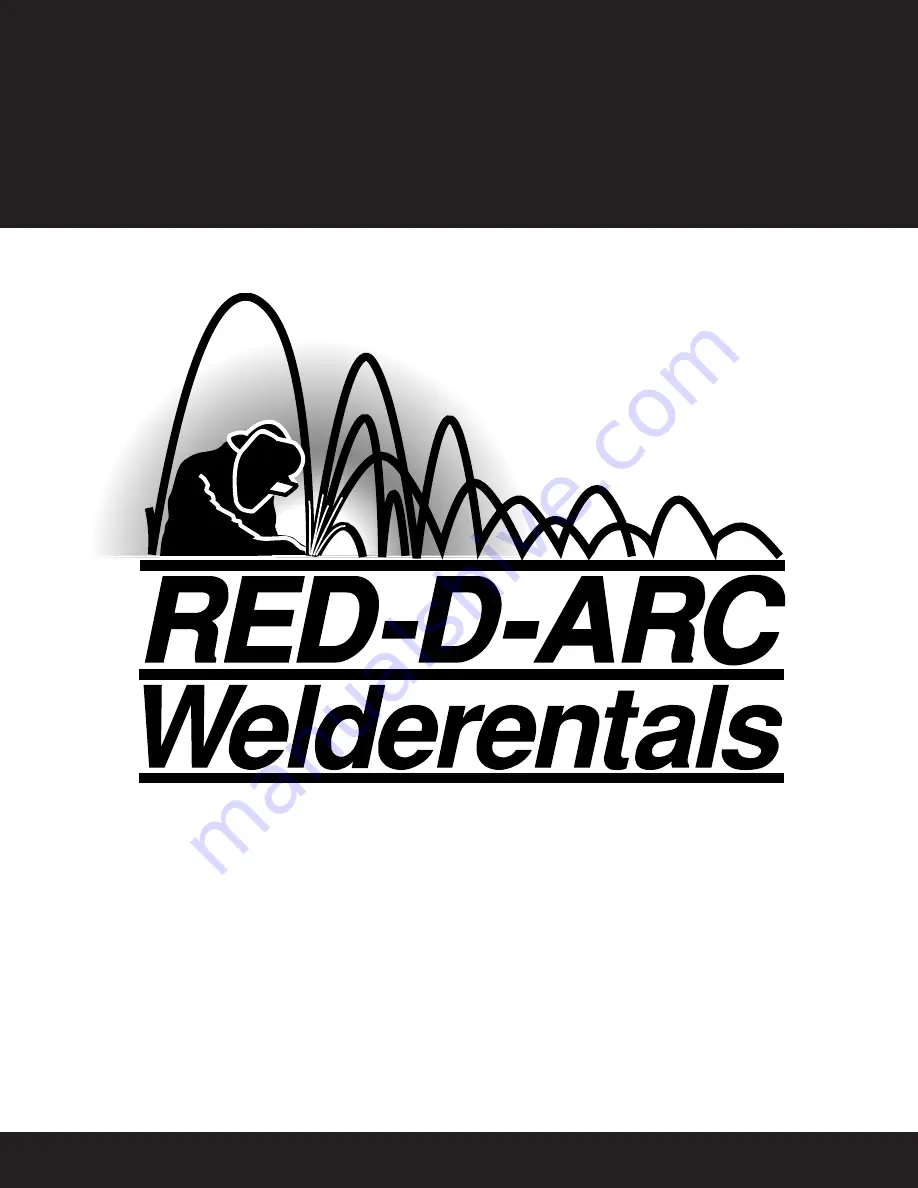
RED-D-ARC
DC-400
IM655-B
November, 2006
Red-D-Arc Spec-Built Welding Equipment
This
RED-D-ARC
welder is built to
RED-D-ARC Extreme Duty
design specifications by Lincoln Electric.
Safety Depends on You
This welder is designed and built with safety in mind.
However, your overall safety can be increased by proper installation
... and thoughtful operation on your part.
DO NOT INSTALL, OPERATE OR REPAIR THIS EQUIPMENT
WITHOUT READING THIS MANUAL AND THE SAFETY
PRECAUTIONS CONTAINED THROUGHOUT.
And, most importantly, think before you act and be careful.
For use with machines having Code Numbers:
10648; 10699; 11038; 11085 and
11128; 11347
North America’s Largest Fleet of Welding Equipment
1-800-245-3660
OPERATOR’S MANUAL
Summary of Contents for RED-D-ARC DC-400
Page 39: ...DC 400 NOTES ...