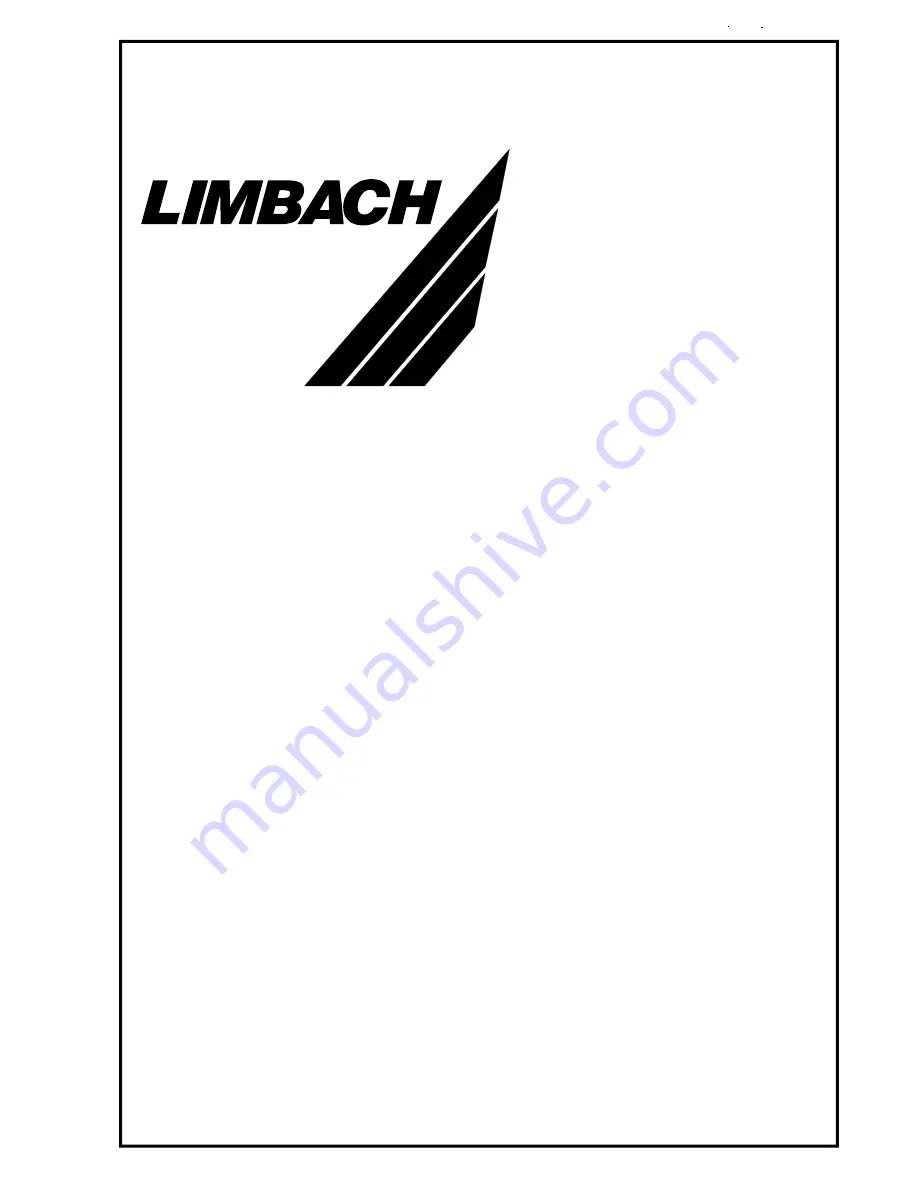
I n s t a l l a t i o n M a n u a l
L 1 7 0 0
L 2 0 0 0
a n d
L 2 4 0 0 S e r i e s
Lim bach Flug mo to ren GmbH & Co. KG
Kot thaus ener Str. 5
53639 Kö nigs win ter
Ger ma ny
Tel.: 02244 / 9201 - 0
Fax: 02244 / 9201 - 30
Part-No. 905.170.010.000
Edi tion: 01.03.99
Limbach Flugmotoren GmbH & Co. KG
Flugmotoren