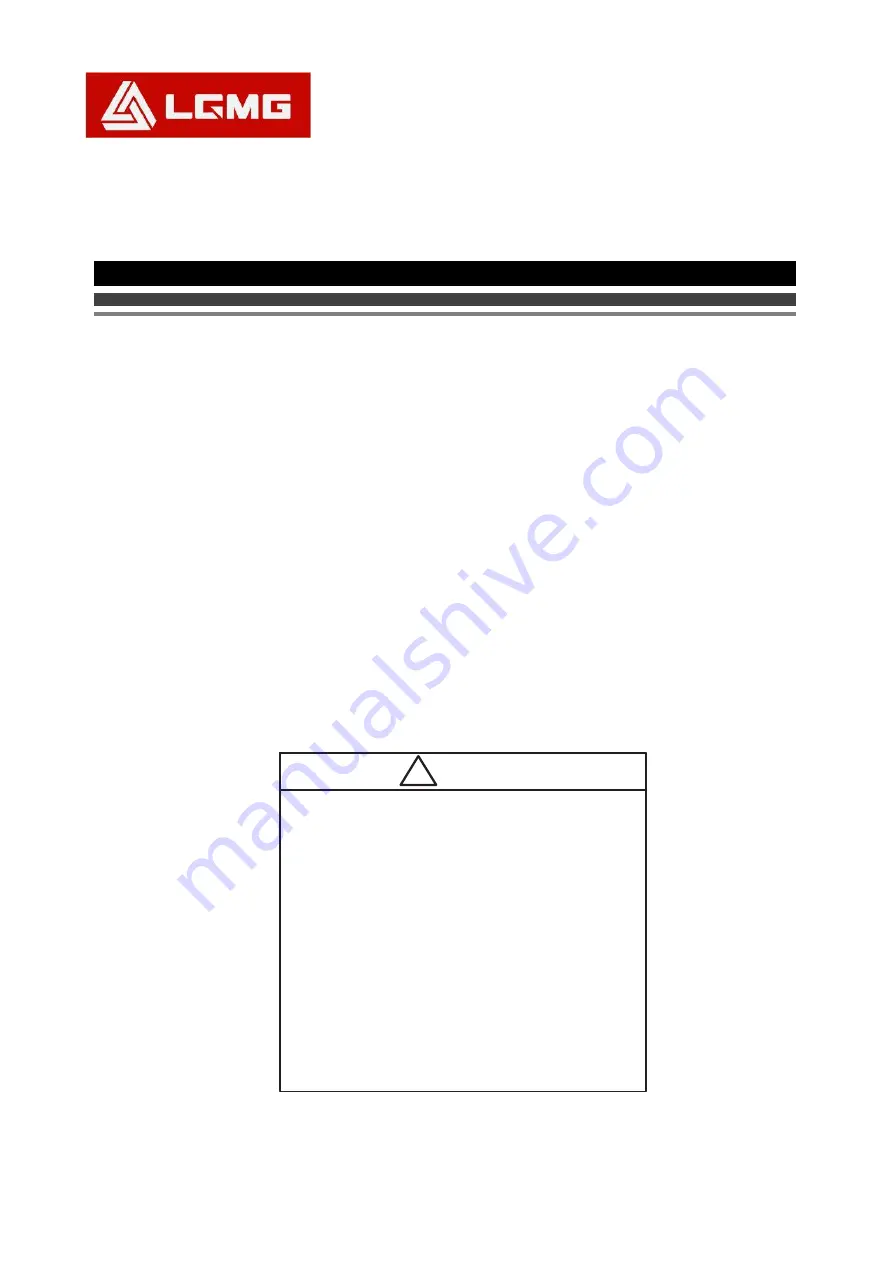
LGMG North America Inc.
Maintenance Manual
T65J/T85J
Mobile Elevating Work Platform
ANSI
!
WARNING
Before operation and maintenance, the
drivers and service personnel shall
always read and thoroughly understand
all information in this manual. Failure to
do so may result in, fatal accidents or
personal injury.
This manual must be kept with this
machine at all times.
Summary of Contents for T65J
Page 2: ...This page left blank intentionally...
Page 6: ...LGMG North America Inc Maintenance Manual IV This page left blank intentionally...
Page 7: ...LGMG North America Inc Maintenance Manual 1 Chapter 1 Maintenance...
Page 8: ...LGMG North America Inc Maintenance Manual 2...
Page 30: ...LGMG North America Inc Maintenance Manual 24...
Page 31: ...LGMG North America Inc Maintenance Manual 25 Chapter 2 Schematics...
Page 32: ...LGMG North America Inc Maintenance Manual 26...
Page 33: ...LGMG North America Inc Maintenance Manual 27 Electric schematic T65J...
Page 34: ...LGMG North America Inc Maintenance Manual 28 Electric schematic T85J...
Page 35: ...LGMG North America Inc Maintenance Manual 29 Hydraulic schematic T65J...
Page 36: ...LGMG North America Inc Maintenance Manual 30 Hydraulic schematic T85J...
Page 37: ...31...