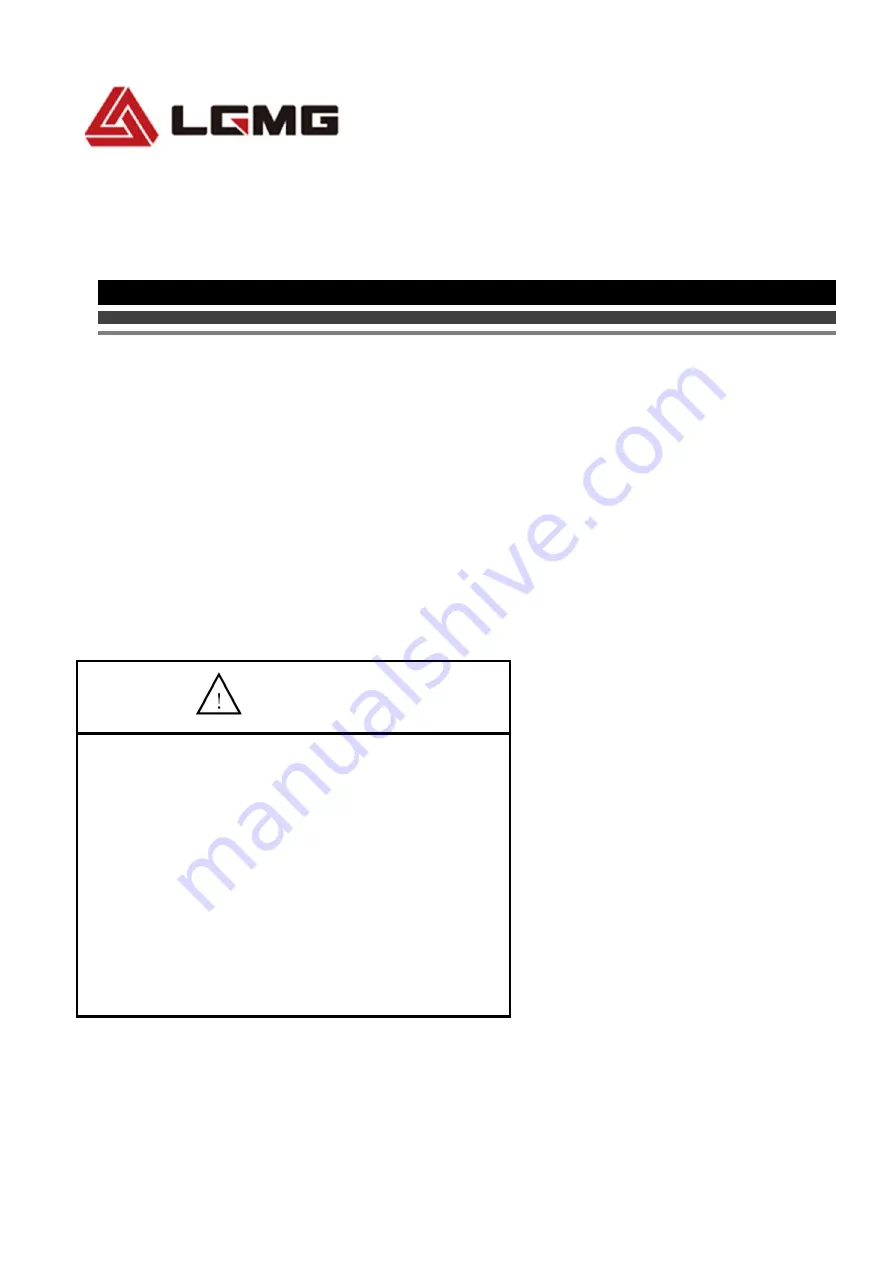
Operation
and
Maintenance
Manual
MT86H
Off
‐
Highway
Dump
Truck
WARNING
Before operation and maintenance, the
drivers and service personnel shall always
read and get understanding of the manual.
Otherwise, fatal accident may occur. This
manual shall be kept properly for future
reference by the personnel concerned.
LINGONG
GROUP
JINAN
HEAVY
MACHINERY
CO.,
LTD
Summary of Contents for MT86H
Page 9: ...MT86H Operation and Maintenance Manual 1 Chapter I Safety ...
Page 10: ...MT86H Operation and Maintenance Manual 2 ...
Page 18: ...MT86H Operation and Maintenance Manual 10 ...
Page 19: ...MT86H Operation and Maintenance Manual 11 Chapter II Product Introduction ...
Page 20: ...MT86H Operation and Maintenance Manual 12 ...
Page 25: ...MT86H Operation and Maintenance Manual 17 Chapter III Operation ...
Page 26: ...MT86H Operation and Maintenance Manual 18 ...
Page 64: ...MT86H Operation and Maintenance Manual 56 ...
Page 142: ...MT86H Operation and Maintenance Manual 134 ...
Page 143: ...MT86H Operation and Maintenance Manual 135 Chapter V Maintenance ...
Page 144: ...MT86H Operation and Maintenance Manual 136 ...
Page 160: ...MT86H Operation and Maintenance Manual 152 3 Lubrication diagram ...
Page 161: ...MT86H Operation and Maintenance Manual 153 Chapter VI Annex ...
Page 165: ...157 6 5 Schematic diagram of electrical system ...