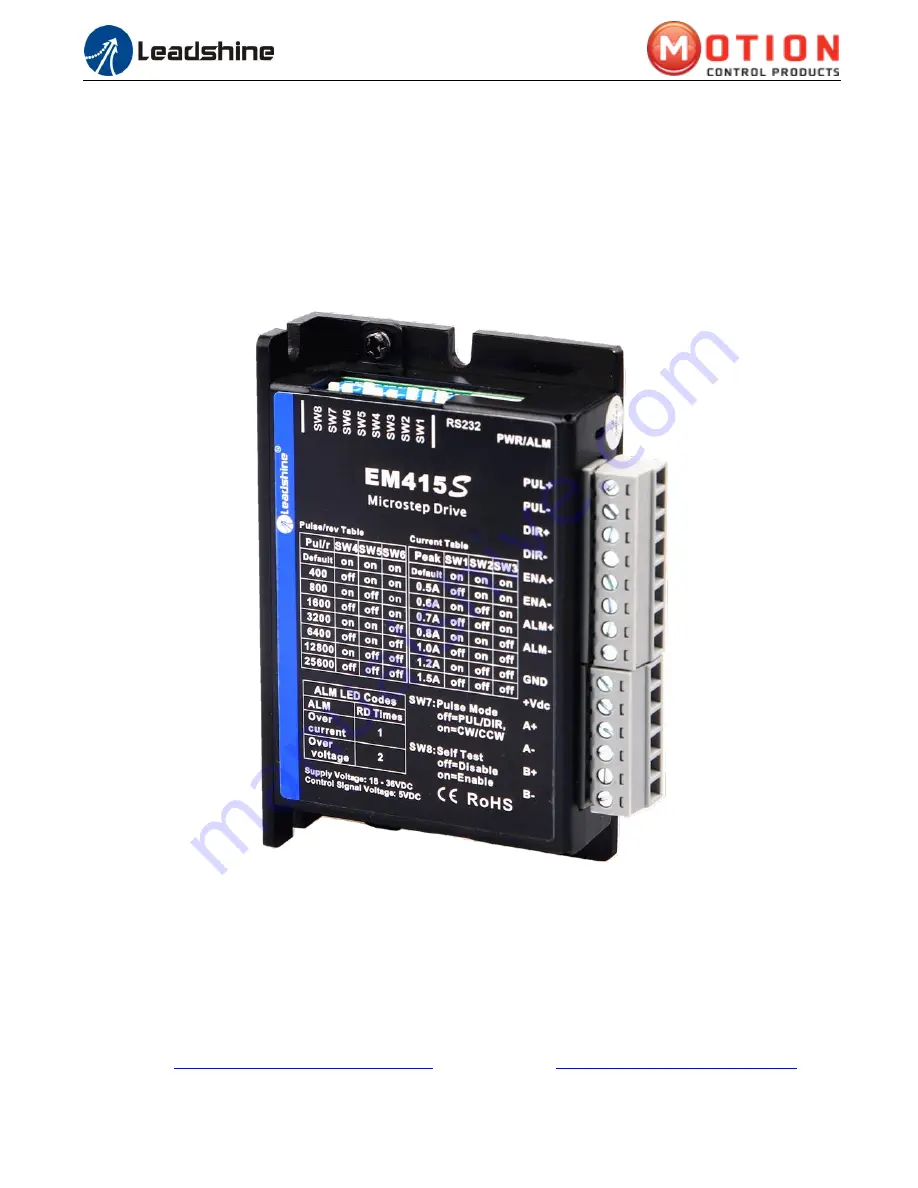
EM415S Digital Stepper Drive User Manual
User Manual
EM415S
Digital Microstepping Drive
Revision 2.0
©2019 Leadshine Technology Co., Ltd.
UK Official Distributor Address:
Motion Control Products Ltd
, 11-15 Francis Avenue, Bournemouth, Dorset, BH11 8NX, United Kingdom
Tel:
+44(0)1202 599922
Fax
: +44 (0)1202 599955
Web:
https://www.motioncontrolproducts.com/
Sales: