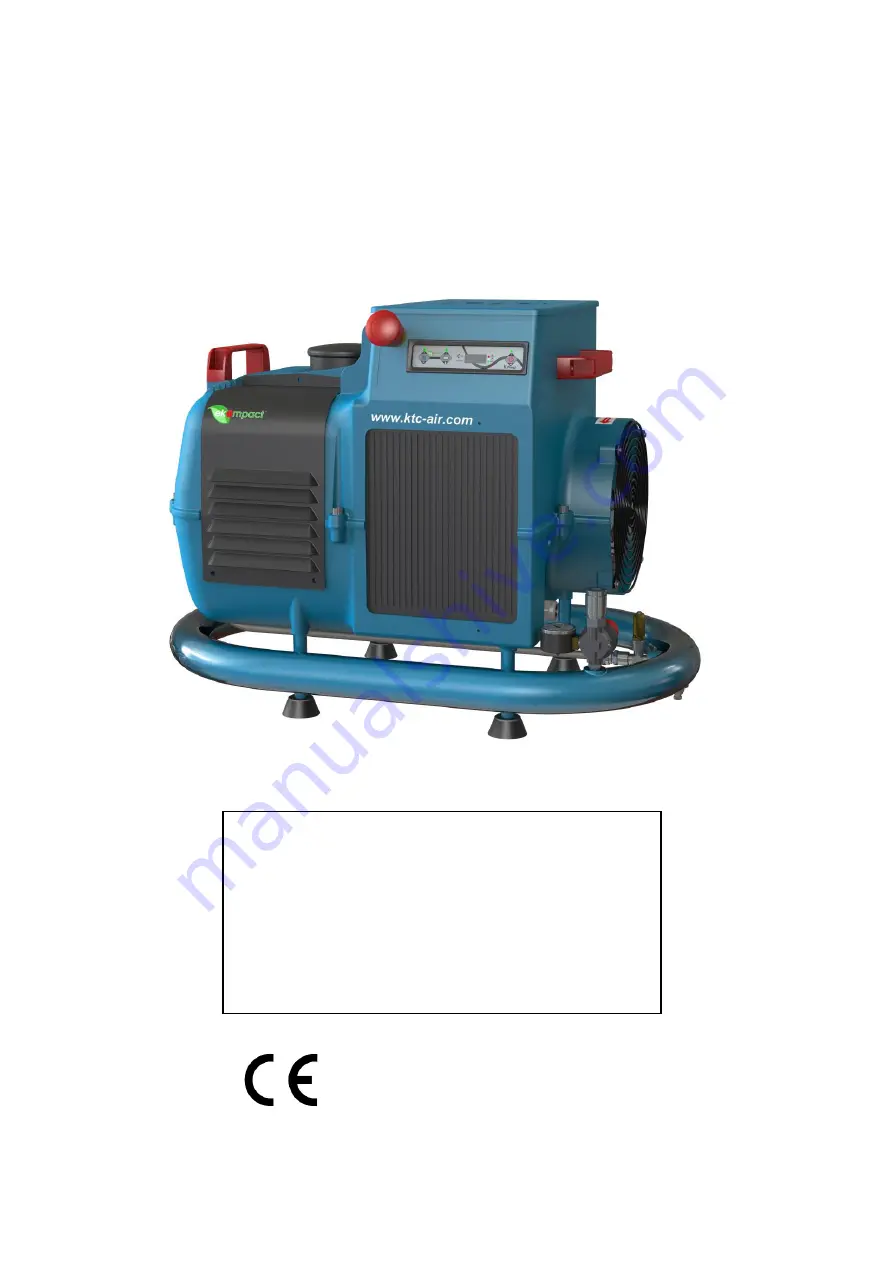
CONFIDENTIAL - This document is the property of K.T.C. S.r.l. and cannot be reproduced or issued to third parties without written
authorization. K.T.C. S.r.l. shall safeguard its rights to the full extent of the law.
OPERATION AND INSTALLATION MANUAL
COD. 091114 – COMPACK 2 ECO / SPECIAL - REV. 08 - DATE 10/2020
page
1
of
63
OPERATION AND MAINTENANCE MANUAL FOR
COMPACK 2 ECO / SPECIAL COMPRESSORS
ENGLISH VERSION