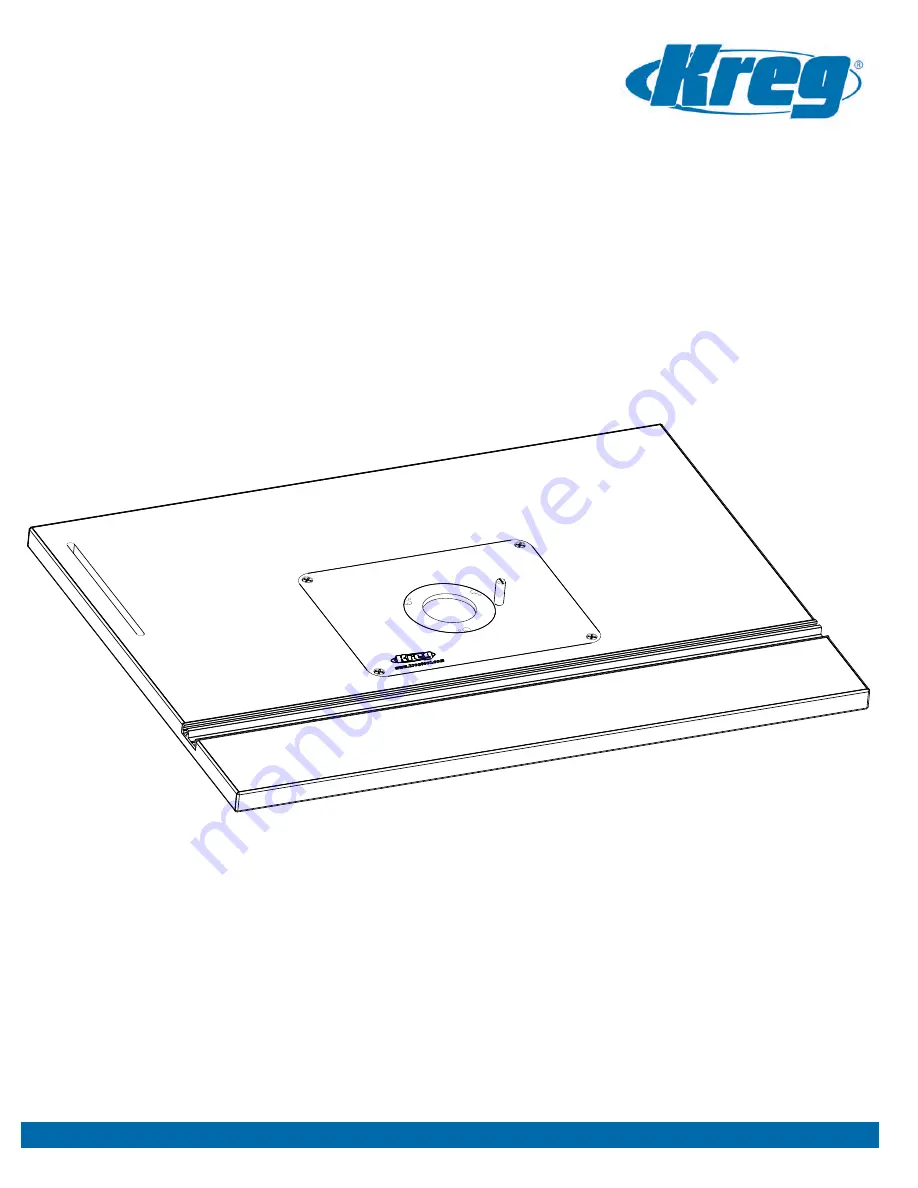
RT10116
Version 20070701
· Woodworking machines are dangerous, and can cause personal injury if not
used
properly.
· Read safety instructions and operating instructions for your machine completely,
before using products. Using this system before understanding its safe and
proper use could result in serious injury to the operator.
· Failure to follow these rules may result in serious personal injury.
· For your own safety, read instruction manual before operating the tool. Learn the
tools application and limitations as well as the specifi c hazards distinctive to it.
· Keep all guards and safety devices in proper place while using these products.
· Always wear safety glasses.
· Keep hands well away from the rotating bit when operating machine.
· Avoid akward hand positions, where a sudden slip could cause contact with the
rotating bit.
· This system was designed for certain applications only. Kreg strongly recommends
that this system NOT be modifi ed and/or used for any application other than
for which it was designed. If you have any questions relative to its application,
DO NOT use the tool until you have written, phoned, or e-mailed Kreg Tool and
have been advised accordingly.
· Be aware of kickbacks. Kickbacks occur when the workpiece binds-up while being
routed, causing it to twist, jump, and possibly become airborne. To avoid kick
backs (and potential injury) always use sharp bits, keep the machine aligned and
maintained properly, and adequately secure/support the workpiece.
· Turn machine off before adjusting. Never adjust the fence, plate level, reducing rings,
or any other part of the tool while the machine is running.
· Wait for the machine to stop. Make sure the router comes to a complete stop before
adjusting the workpiece or workpiece-angle.
· Ground electric machines. If your machine is equipped with a three-prong plug, it
should be plugged into a three-hole electrical receptacle only. If the proper
outlet is not available, have one installed by a qualifi ed electrician before use.
Never remove the third prong, and never modify the provided plug in any way.
· Don’t operate in a dangerous or unclean environment. Don’t use power tools in
damp or wet locations, or expose them to rain. Keep work area well-lit,
un-cluttered, and clean.
· Keep children and visitors away. All children and visitors should be kept a safe distance
from the work area, and should not operate the tool under any condition.
· Make your workshop “child-proof”. Use padlocks, master switches, or any other means
necessary to make your work area safe for children.
· Use the right tool. Never ‘force’ the tool to do work for which it was not intended. If used
properly, the tool will produce better results in less time, under safer conditions.
· Wear proper apparel. No loose clothing, gloves, neckties, rings, bracelets, or any other
jewelry that could possibly get caught in moving parts. Non-slip footwear is highly
recommended, as is protective hair covering. Remember to always use safety glasses,
specifi cally designed as safety wear.
· Secure the workpiece. Use clamps or a vise to hold work when it is practical and safe.
Using the proper tool may allow you to free both hands for tool operation. Also, be sure
to never overreach.
· Secure your tools. In the event of the machine tipping or sliding, it is always
recommended to secure your tools to the machine during use.
· Keep the proper footing and balance. Ensure that you are in no danger of slipping or
sliding once you turn the machine on. Once again, non-slip footwear is highly
recommended.
· Maintain tools in top condition. Keep tools sharp, clean, and properly maintained for the
highest quality and safest performance. Remember to properly follow all lubrication and
accessory maintenance practices, as detailed in this Instruction Manual.
· Disconnect tool before servicing. When changing accessories such as bits, clamps, etc.,
making any sort of physical assessment of the tool, or when motor is being mounted/
connected, remember to disconnect the machine from its power source. This will reduce
the possibility of accidentally engaging the machine.
· Check for damaged parts. Before use of the tool, a careful assessment of all guards and
other parts should be made to ensure that it will operate properly, and perform as
intended. Check for alignment of moving parts, binding of moving parts, breakage of
parts, mounting, and any other conditions that may affect its operation. A guard or other
part that is damaged should be properly repaired or replaced as soon as possible,
preceding any additional use. Do not use the tool if you are not qualifi ed to make these
sorts of assessments.
· Never leave a running machine unattended. Always turn the machine’s power “OFF”
after operation. Do not leave the tool until it comes to a complete stop.
· Drugs, alcohol, medication warning. Do not operate tool while under the infl uence of
drugs, alcohol, or any medications.
Router Table Top
Precision
ASSEMBLY INSTRUCTIONS
Item# PRS1020
Other Precision Routing Products
Safety Guidelines
7.
(
24” x 32”
)
Tools Required:
• 5/64” Allen Wrench
• Phillips Head Screwdriver
• Flat Head Screwdriver
• 6” #2 Square Driver
• 1/8” Allen Wrench (Included)
• 3” #2 Square Driver (Included)
www.kregtool.com • 800.447.8638
This unique featherboard can be quickly and easily connected to almost any
miter slot or t-slot without the need for additional hardware. It features a durable
plastic composite body which ensures optimum workpiece pressure.
True-FLEX
True-FLEX
Featherboard
Featherboard
TM
Item# PRS3010
Taking cues from high-end table saw rip fences, this groundbreaking router
fence provides an entirely new way to work. It’ll make every project you
start faster, easier, and far more precise than ever before.
Precision Router Table Fence
Precision Router Table Fence
Item# PRS1010
www.kregtool.com • 800.447.8638
Come meet the entire family of Precision Routing Products
Come meet the entire family of Precision Routing Products
at www.kregtool.com
at www.kregtool.com