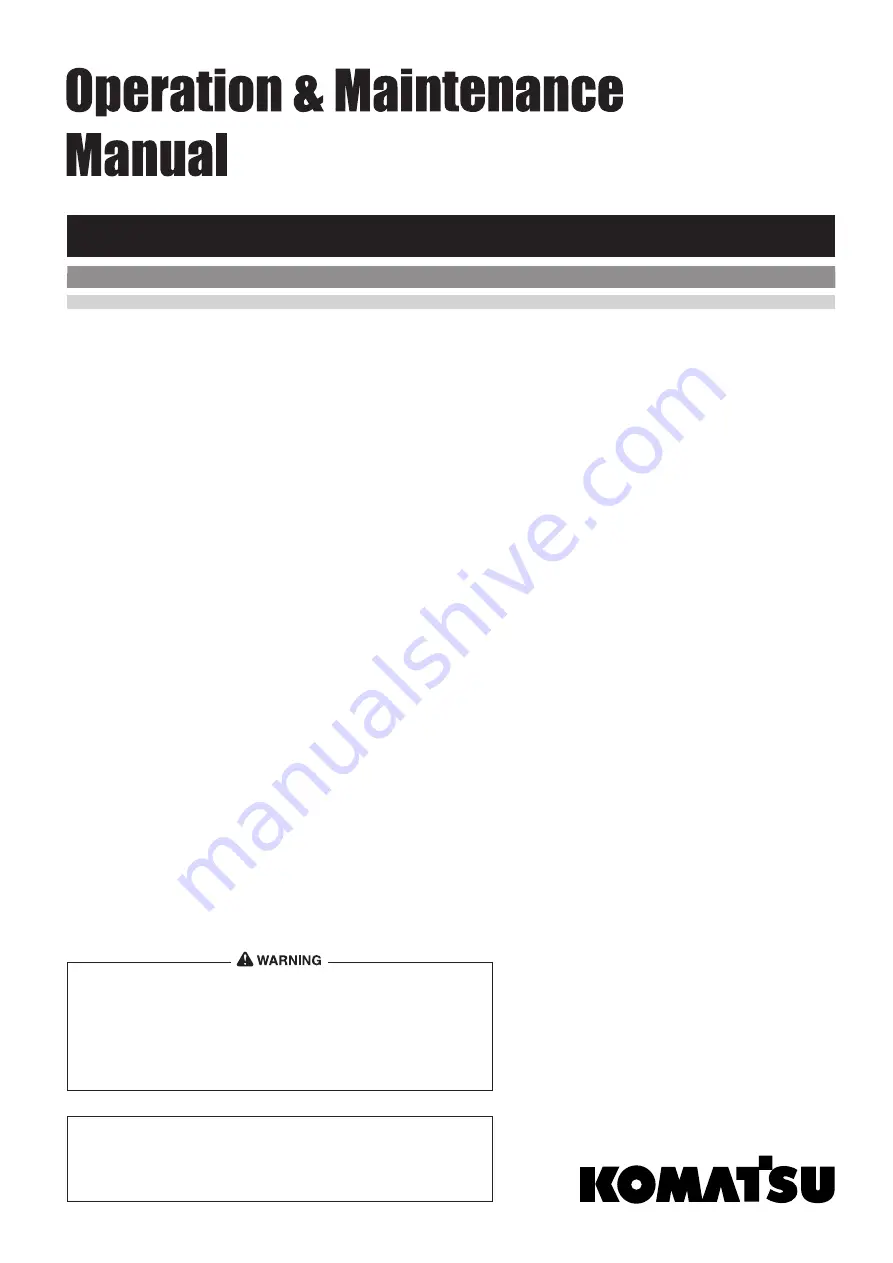
WA20
-2
,WA30
-5
WA40
-3
,WA50
-3
WHEEL LOADER
SERIAL NUMBERS
and up
NOTICE
Komatsu has Operation & Maintenance Manuals written in
some other languages. If a foreign language manual is
necessary, contact your local distributor for availability.
Unsafe use of this machine may cause serious injury
or death. Operators and maintenance personnel
must read this manual before operating or maintain-
ing this machine. This manual should be kept near the
machine for reference and periodically reviewed
by all personnel who will come into contact with it.
WA20 - 11270
WA30 - 18970
WA40 - 13530
WA50 - 20642
SEAM010700
Summary of Contents for WA20-2
Page 39: ...1 30 MEMO ...
Page 40: ...2 1 OPERATION ...
Page 42: ...2 3 10 GENERAL VIEW 10 GENERAL VIEW 10 2 GENERAL VIEW OF CONTROLS AND GAUGES ...
Page 114: ...3 1 MAINTENANCE ...
Page 132: ...3 19 22 PERIODIC REPLACEMENT OF SAFETY CRITICAL PARTS ...
Page 134: ...3 21 22 PERIODIC REPLACEMENT OF SAFETY CRITICAL PARTS ...
Page 136: ...3 23 22 PERIODIC REPLACEMENT OF SAFETY CRITICAL PARTS ...
Page 175: ...3 62 MEMO ...
Page 176: ...4 1 SPECIFICATIONS ...
Page 178: ...5 1 OPTIONS ATTACHMENTS ...
Page 188: ...4 3 25 SPECIFICATIONS 25 SPECIFICATIONS ...
Page 190: ...4 5 25 SPECIFICATIONS 25 SPECIFICATIONS ...
Page 192: ...4 7 25 SPECIFICATIONS 25 SPECIFICATIONS ...
Page 194: ...4 9 25 SPECIFICATIONS 25 SPECIFICATIONS ...
Page 195: ...4 10 MEMO ...