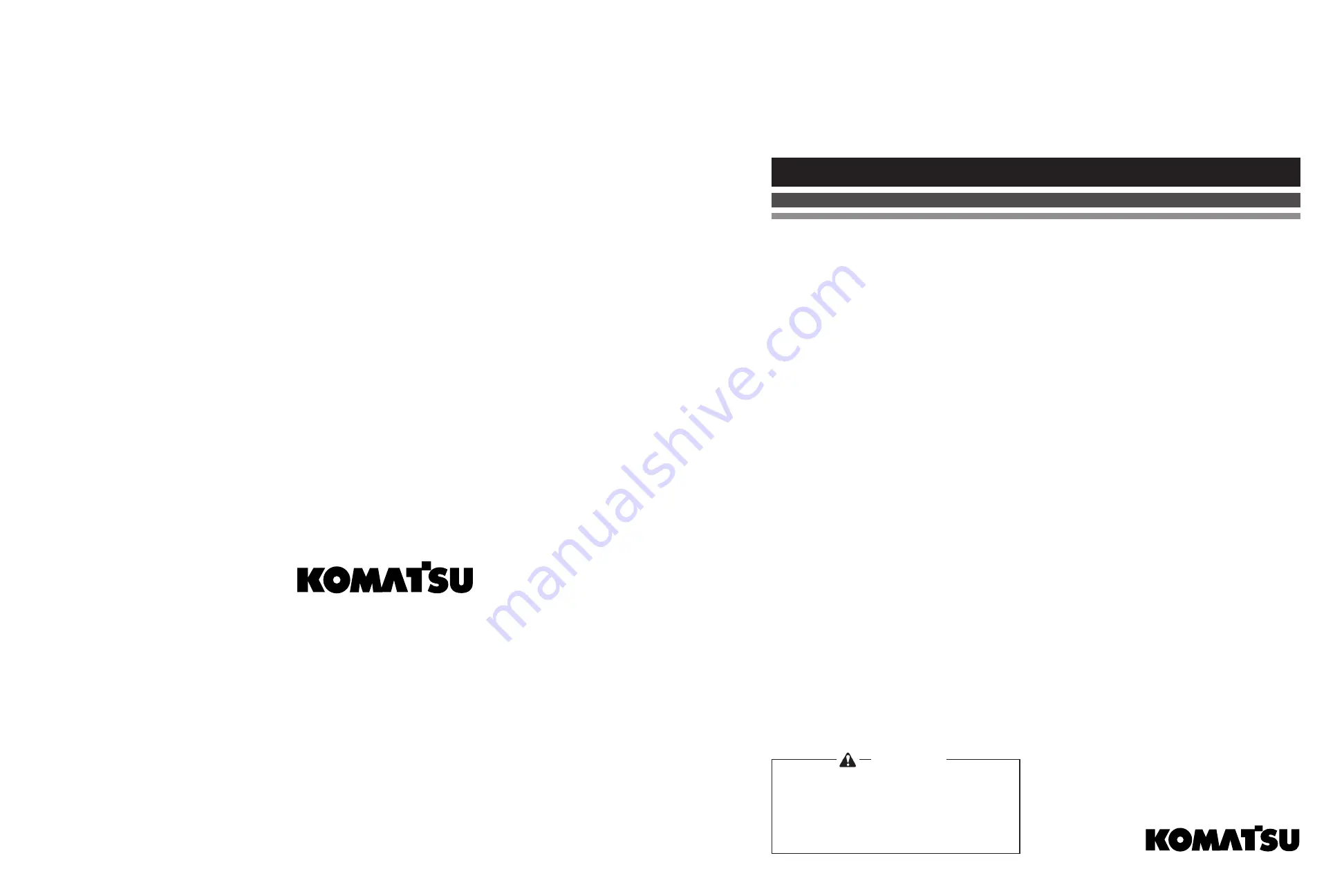
Unsafe use of this machine may cause serious injury or
death. Operators and maintenance personnel must read this
manual before operating or maintaining this machine. This
manual should be kept inside the cab for reference and
periodically reviewed by all personel who will come into
contact with the machine.
EEAM010300
Operation &
Maintenance Manual
PC290LC
-6K
PC290NLC
-6K
HYDRAULIC EXCAVATOR
SERIAL NUMBER
PC290LC-6K - K30001
and up
PC290NLC-6K - K30001
and up
Including 2 piece boom
WARNING
© Komatsu Europe International
All Rights Reserved
Printed in Europe
5-2002
PC290LC-6K,PC290NLC-6K
EEAM010300
Summary of Contents for PC290LC-6K
Page 2: ......
Page 44: ...1 32 PC290 ENG MEMO ...
Page 45: ...2 1 PC290 ENG OPERATION ...
Page 146: ...2 102 PC290 ENG MEMO ...
Page 147: ...3 1 PC290 ENG MAINTENANCE ...
Page 171: ...3 25 PC290 ENG 22 PERIODIC REPLACEMENT OF SAFETY CRITICAL PARTS m n ...
Page 223: ...4 1 PC290 ENG SPECIFICATIONS ...
Page 225: ...4 3 PC290 ENG 25 SPECIFICATIONS PC290LC 6K ...
Page 226: ...4 4 PC290 ENG 25 SPECIFICATIONS PC290NLC 6K ...
Page 230: ...4 8 PC290 ENG 25 SPECIFICATIONS Mono Boom ...
Page 233: ...5 1 PC29 ENG OPTIONS ATTACHMENTS ...
Page 264: ...5 30 PC29 ENG MEMO ...