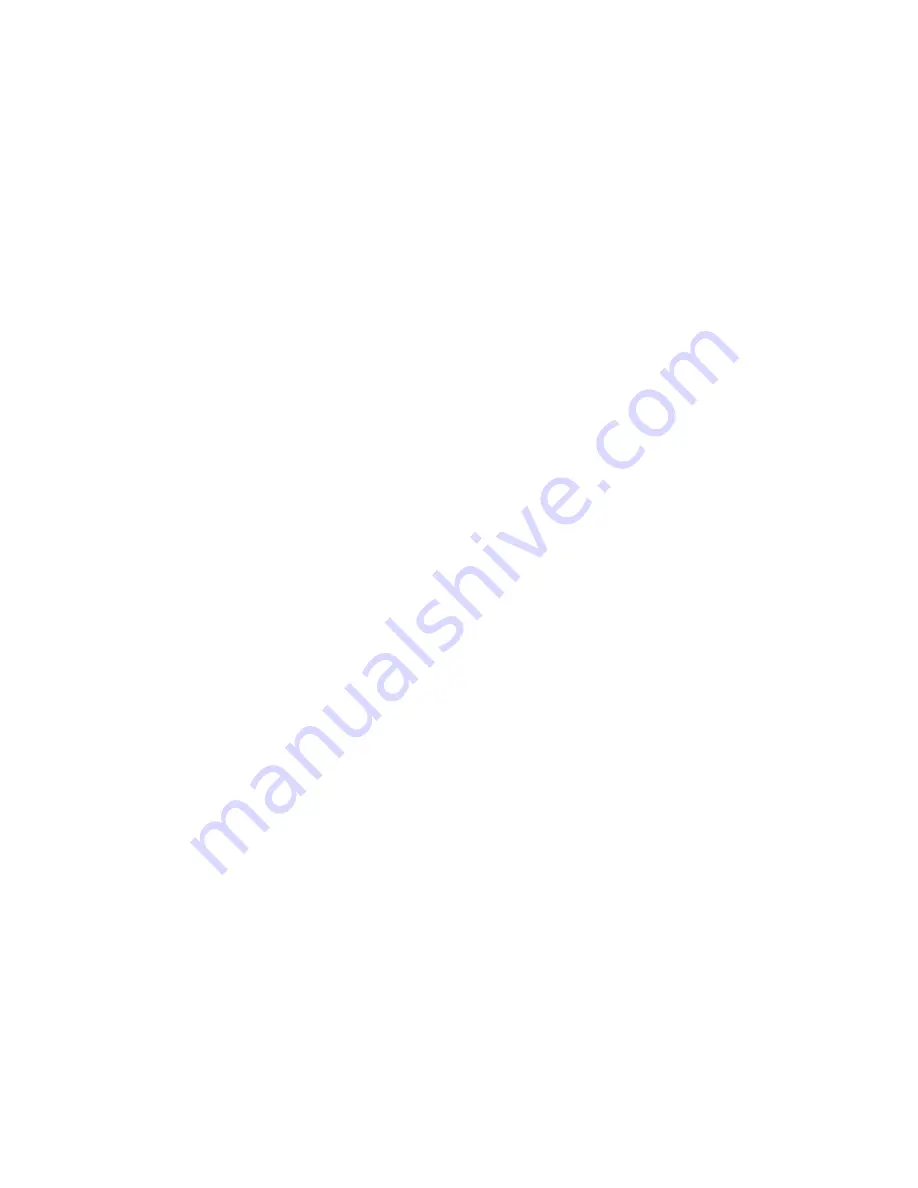
CEBM028602
Shop
Manual
PC240LC
-11
HYDRAULIC EXCAVATOR
SERIAL NUMBERS
PC240LC-11 A22001
and up
ENGINE
6D107E-3
This material is proprietary to Komatsu America Corp. and is not to be reproduced, used, or disclosed except in
accordance with written authorization from Komatsu America Corp.
It is our policy to improve our products whenever it is possible and practical to do so. We reserve the right to
make changes or improvements at any time without incurring any obligation to install such changes on products
sold previously.
Due to this continuous program of research and development, revisions may be made to this publication. It is
recommended that customers contact their distributor for information on the latest revision.
Copyright 2015 Komatsu
Printed in U.S.A.
Komatsu America Corp.
April 2015