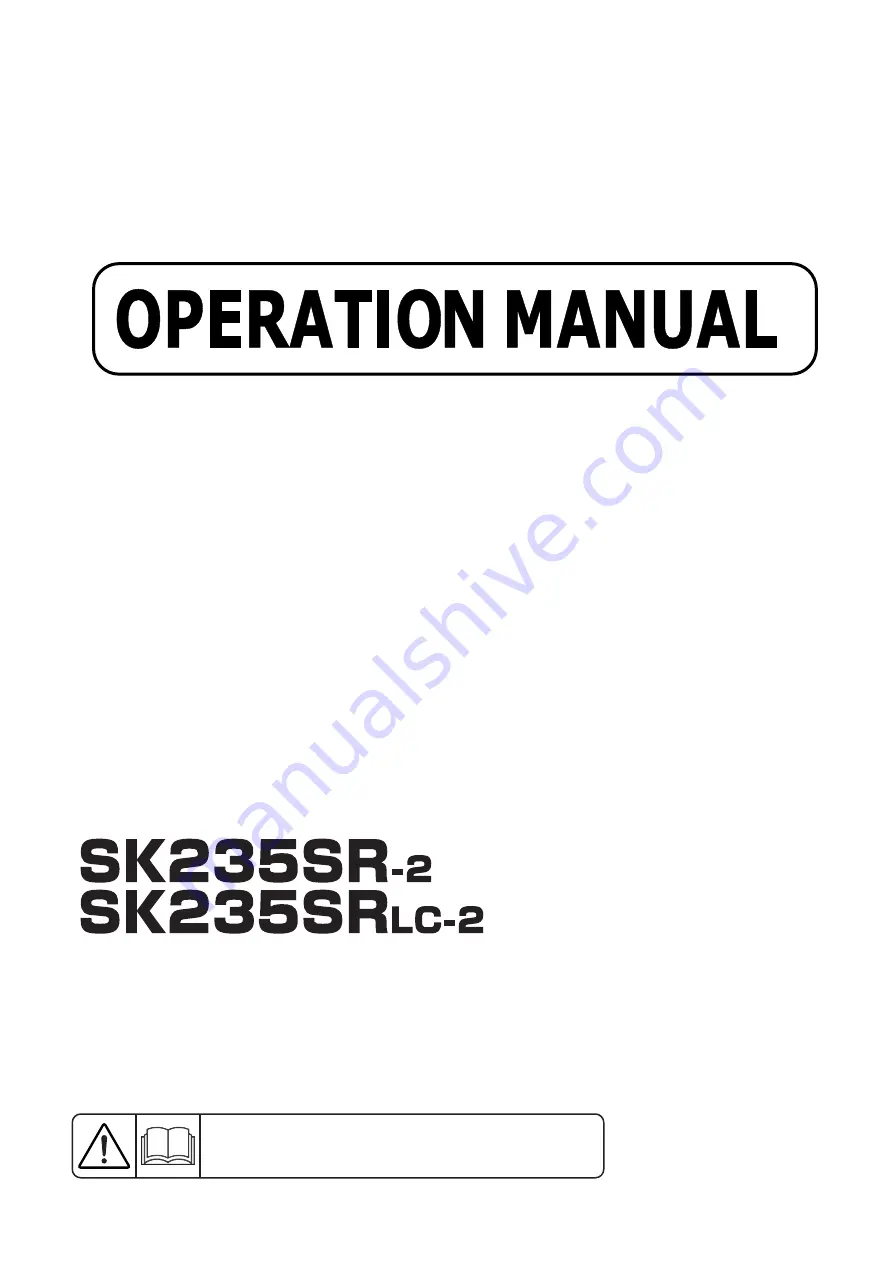
Book Code No. S2YF00022ZE01
APPLICABLE No.
SK235SR
-2
SK235SR
LC-2
YF06-02559~
YU06-03014~
READ, UNDERSTAND AND FOLLOW ALL SAFETY
PRECAUTIONS AND INSTRUCTIONS FOUND IN THIS
MANUAL BEFORE OPERATING THE MACHINE.
Printed in Japan 2010.11 (KE)
Destination : AUS
Copyright © 2015 Kobelco Construction Machinery Co.,Ltd. All rights reserved. [S2YF00022ZE01] [0731CsCshWbYs]