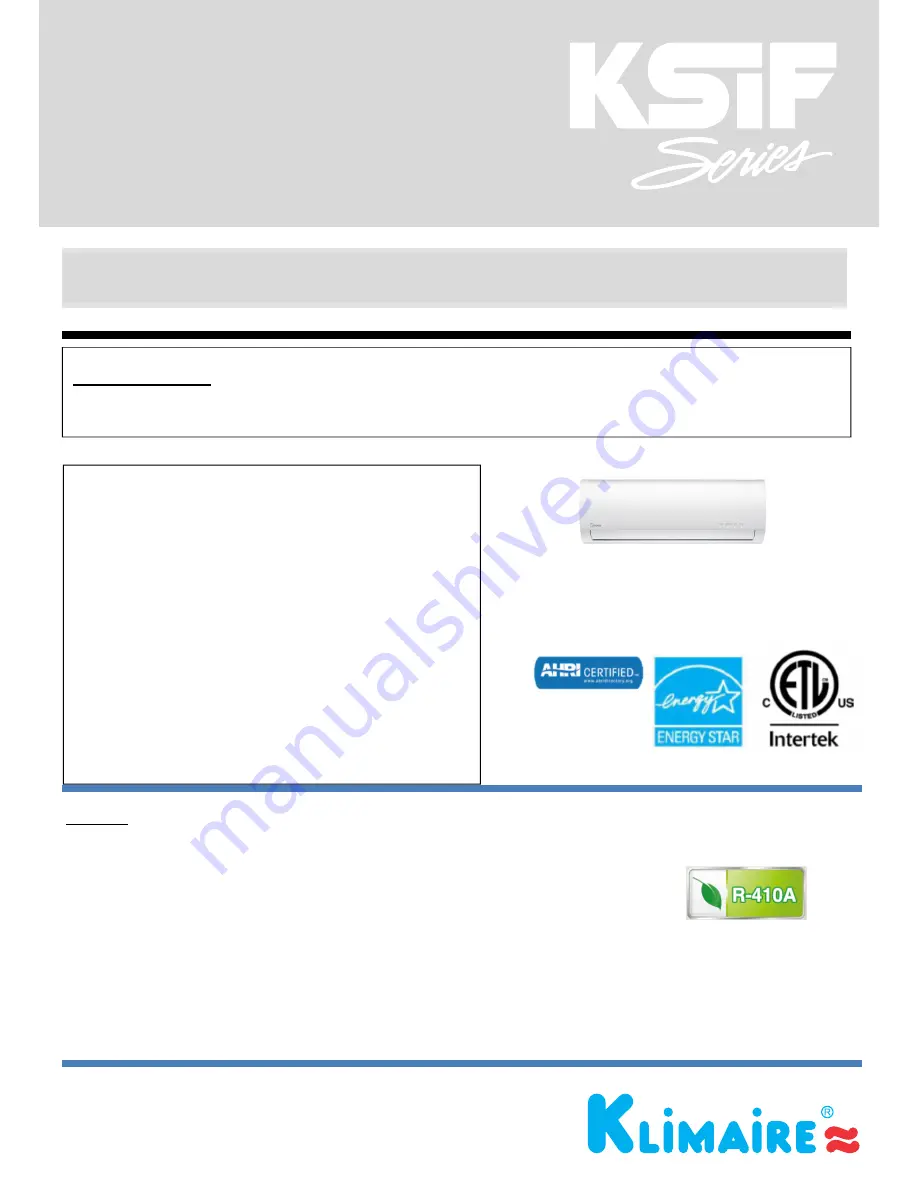
Model Numbers:
KSIF009-H115-I
,
KSIF012-H115-I
,
KSIF009-H215-I
,
KSIF012-H215-I
,
KSIF018-H215-I
,
KSIF024-H215-I
Table of Contents
1.
Precaution
2.
Part Names And Functions
3.
Dimension
4.
Refrigerant Cycle Diagram
5.
Wiring Diagram
6.
Installation Details
7.
Operation Characteristics
8.
Electronic Function
9.
Troubleshooting
10. Disassembly Instructions
WARNING
Installation MUST conform with local building codes or, in the absence of local codes, with the
National Electrical Code NFPA70/ANSI C1-1993 or current edition and Canadian Electrical
Code Part1 CSA C.22.1.
The information contained in the manual is intended for use by a qualified service technician
familiar with safety procedures and equipped with the proper tools and test instruments
Installation or repairs made by unqualified persons can result in hazards to you and others.
Failure to carefully read and follow all instructions in this manual can result in equipment
malfunction, property damage, personal injury and/or death.
This service is only for service engineer to use.
SERVICE MANUAL
Summary of Contents for KSIF009-H115-I
Page 7: ...5 2 2 Indoor Outdoor units ...
Page 9: ...7 For Mounted plate A For Mounted plate B For Mounted plate C ...
Page 10: ...8 For Mounted plate D ...
Page 42: ...40 P W N U ...
Page 43: ...41 N V N W ...