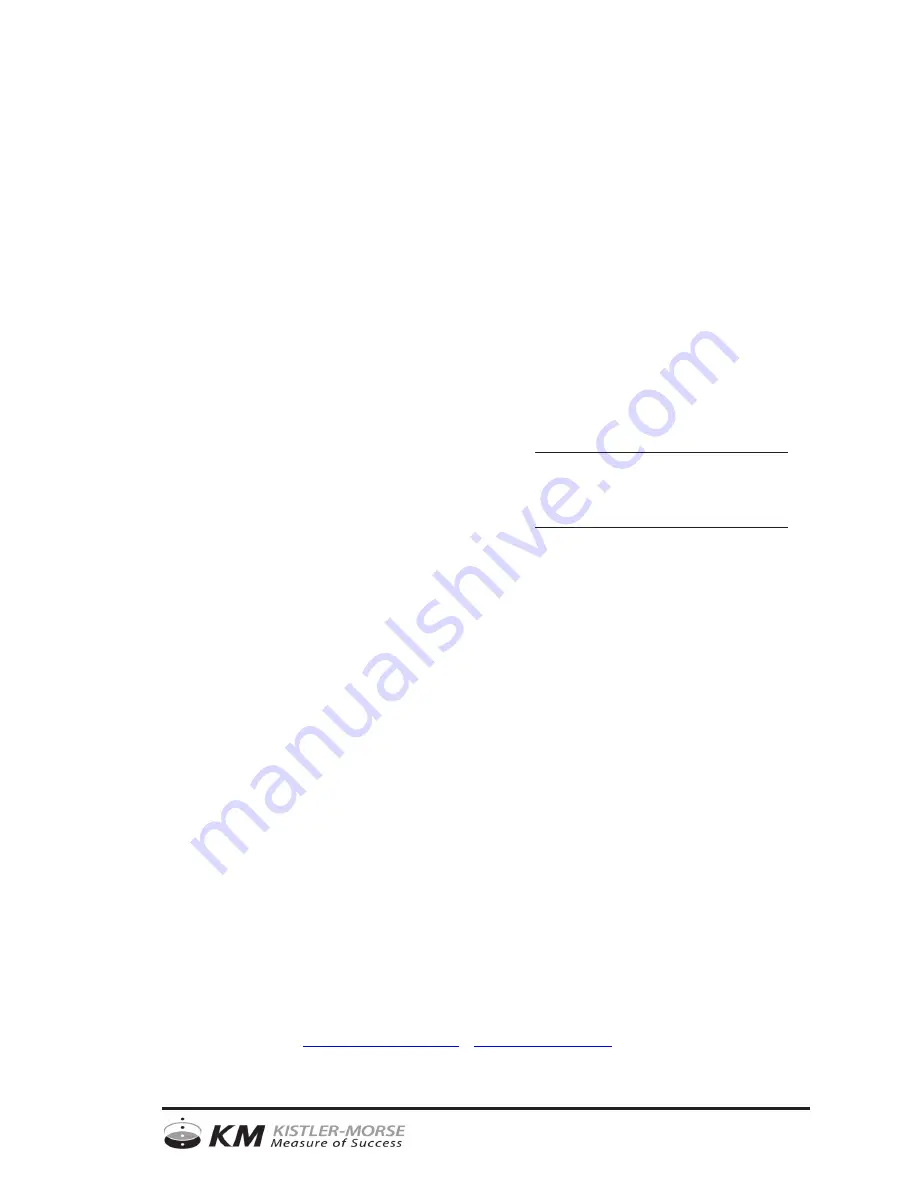
Weigh II Installation
and Operation Manual
CAUTION
It is essential that all instructions in
this manual be followed precisely to
ensure proper operation of the
equipment.
97-1120-01
Rev. D
January 2005
$15.00 U.S.
O
O
r
r
d
d
e
e
r
r
f
f
r
r
o
o
m
m
:
:
C
C
A
A
B
B
r
r
i
i
g
g
g
g
s
s
C
C
o
o
m
m
p
p
a
a
n
n
y
y
622 Mary Street; Suite 101; Warminster, PA 18974
Phone: 267-673-8117 - 800-352-6265; Fax: 267-673-8118
-
www.cabriggs.com
Summary of Contents for Weigh II
Page 12: ...2 4 Chapter 2 Hardware Installation...
Page 20: ...3 8 Chapter 3 Menu Tree Keyboard Functions and Quick Start...
Page 50: ...6 12 Chapter 6 Calibration...
Page 68: ...A 2 Appendix A Product Specifications...
Page 70: ...B 2 Appendix B Summary of Commands Used When Vessel Mounting Hot Keys...
Page 77: ...Appendix E E 1 This appendix not used at this time...
Page 78: ...Appendix E E 2...
Page 80: ...Appendix F Technical Drawings F 2...
Page 81: ...Appendix F Technical Drawings F 3...
Page 82: ...Appendix F Technical Drawings F 4...
Page 83: ...Appendix F Technical Drawings F 5...
Page 84: ...Appendix F Technical Drawings F 6...
Page 85: ...Appendix F Technical Drawings F 7...
Page 86: ...Appendix F Technical Drawings F 8...
Page 87: ...Appendix F Technical Drawings F 9...
Page 88: ...Appendix F Technical Drawings F 10...
Page 89: ...Appendix F Technical Drawings F 11...
Page 90: ...Appendix F Technical Drawings F 12...
Page 91: ...Appendix F Technical Drawings F 13...
Page 92: ...Appendix F Technical Drawings F 14...
Page 93: ...Appendix F Technical Drawings F 15...
Page 94: ...Appendix F Technical Drawings F 16...
Page 95: ...Appendix F Technical Drawings F 17...
Page 96: ...Appendix F Technical Drawings F 18...
Page 97: ...Appendix F Technical Drawings F 19...
Page 98: ...Appendix F Technical Drawings F 20...
Page 99: ...Appendix F Technical Drawings F 21...
Page 100: ...Appendix F Technical Drawings F 22...
Page 101: ...Appendix F Technical Drawings F 23...
Page 102: ...Appendix F Technical Drawings F 24...
Page 103: ...Appendix F Technical Drawings F 25...
Page 104: ...Appendix F Technical Drawings F 26...
Page 105: ...Appendix F Technical Drawings F 27...
Page 106: ...Appendix F Technical Drawings F 28...
Page 107: ...Appendix F Technical Drawings F 29...
Page 108: ...Appendix F Technical Drawings F 30...
Page 109: ...Appendix F Technical Drawings F 31...
Page 110: ...Appendix F Technical Drawings F 32...
Page 116: ...Appendix G Calculation of Maunal Calibration Parameters G 6...