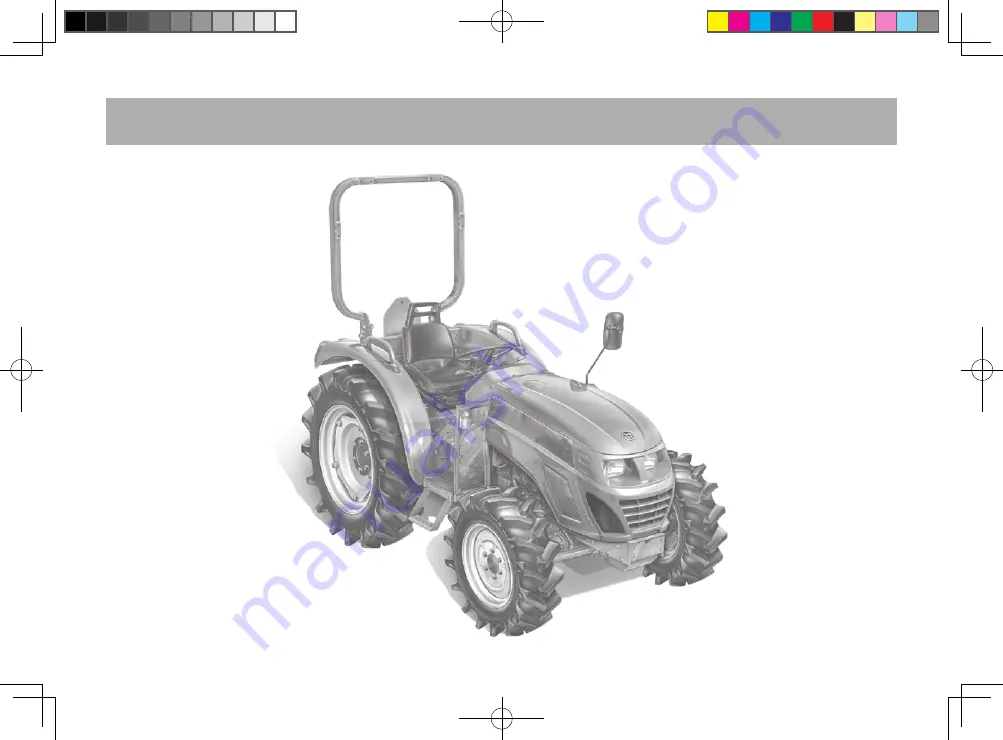
Congratulations, and welcome to the fabulous world of
LX500L
ownership, where serious work is made fun
again!
This versatile tractor is a culmination of the entire tractor and diesel knowledge gained by the Daedong Indus-
trial Co.,LTD over the years since 1947 and has been designed with the finest materials and under rigid quality
control standards set forth by the
KIOTI
Engineering Department.
Knowledge of tractor operation is essential for many years of dependable service and reliability. To help new
owner’s familiarize themselves with the
KIOTI LX500L
, it is the policy of
KIOTI
tractor to provide an owner’s
manual which includes helpful information about tractor safety, operation and maintenance. If the information
you seek is not found in this manual, your
KIOTI
tractor dealer will be happy to help you.
Please feel free to contact
DAEDONG IND. CO.,LTD
with your questions/concerns.
FOREWORD
LX500_en_om_00.indd 1
2012-11-27 오후 2:56:01
Summary of Contents for LX500L
Page 6: ...LX500_en_om_00 indd 6 2012 11 27 2 54 38...
Page 32: ...1 20 LX500L s76o187a LX500_en_om_01 indd 20 2012 11 27 3 05 01...
Page 38: ...MEMO LX500_en_om_01 indd 26 2012 11 27 3 05 16...
Page 39: ...2 2 SERVICING OF TRACTOR SERVICING 2 2 LX500_en_om_02 indd 1 2012 11 27 3 05 56...
Page 50: ...MEMO LX500_en_om_03 indd 10 2012 11 27 3 06 19...
Page 56: ...MEMO LX500_en_om_04 indd 6 2012 11 27 3 06 46...
Page 98: ...MEMO LX500_en_om_06 indd 10 2012 11 27 3 08 38...
Page 111: ...9 9 MAINTENANCE SERVICE INTERVALS 9 2 LUBRICANTS 9 4 LX500_en_om_09 indd 1 2012 11 27 3 11 59...
Page 144: ...MEMO LX500_en_om_11 indd 4 2012 11 27 3 12 27...
Page 153: ...13 13 INDEX INDEX 13 2 LX500_en_om_13 indd 1 2012 11 27 3 13 28...