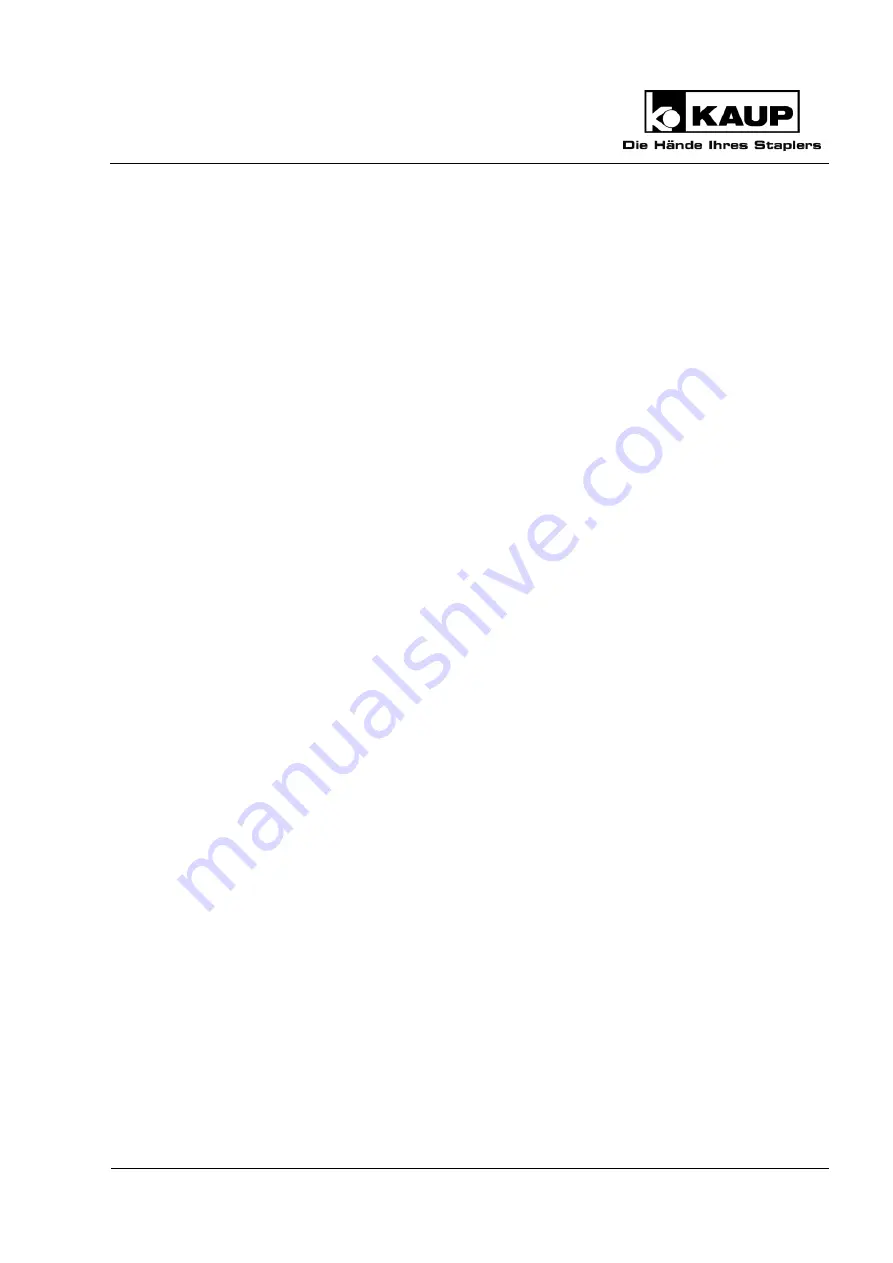
SAP
100069
en
en
Operating Manual
Original Operating Manual
1
Edition 12/17
Subject to modifications
Clamp
T 411B, T 411BA
T 401B, T 401BA
Fork Positioner
T 411 B, T 401 BZ
T 411 B, T 401 BZ
T 411 B / BA
Clamp with welded-on / bolt-on forks with sideshift
T 401 B / BA
Clamp with welded-on / bolt-on forks without sideshift
T 411 BZ / BZA
Fork Positioner with welded-on forks / bolt-on with valveblock sideshift
T 401 BZ / BZA
Fork Positioner with welded-on forks / bolt-on without sideshift