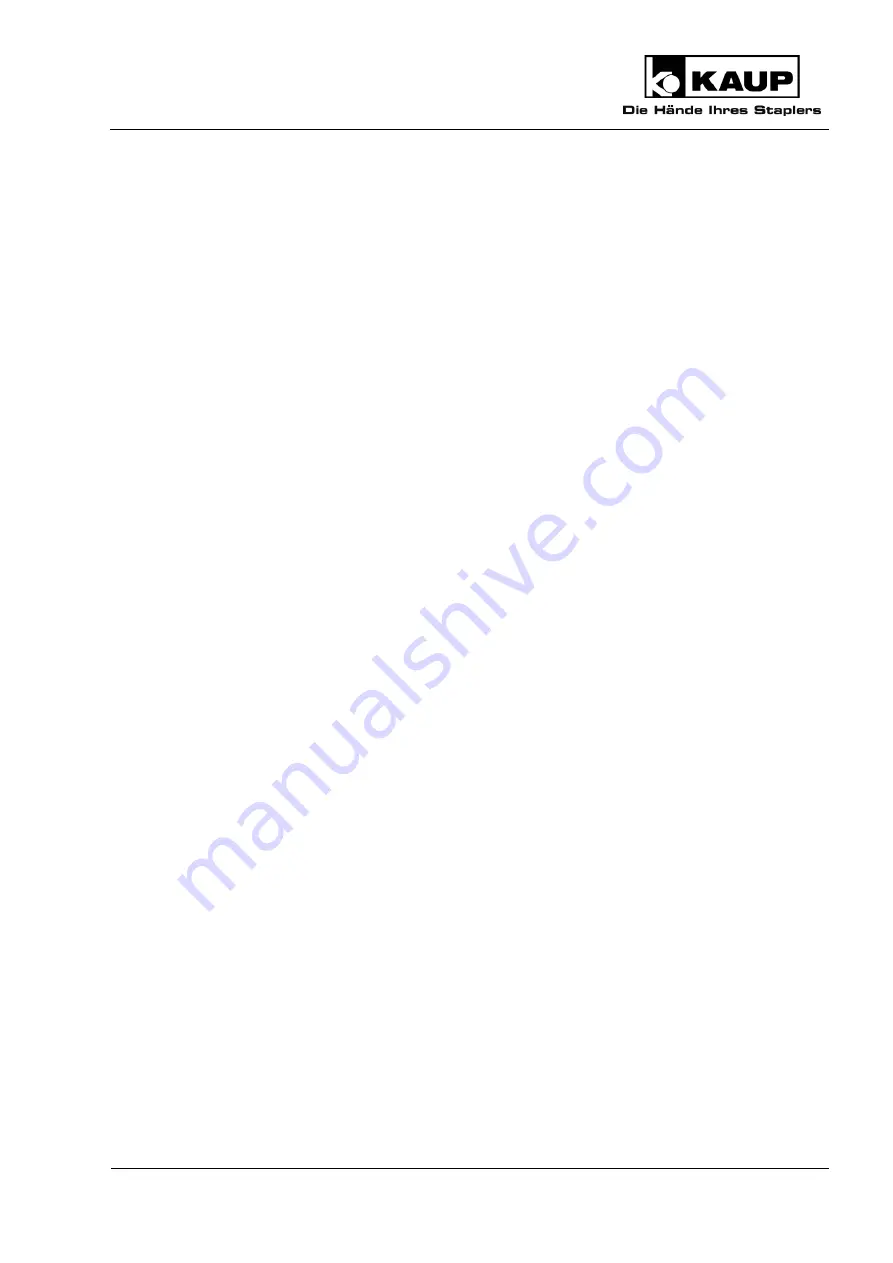
SAP 100074
en
Operating Manual
Original Operating Manual
1
Edition 04/17
Subject to modifications
Appliance Clamp
T 413G-1L, T 403G-1L
T 413G-2L, T 403G-2L
T 413-1, T 414-1
T 414-1L, T 404-1L
T 414-2L, T 404-2L
T413-1
T414-1
T413G-1L
Appliance Clamp with sideshift
and arms with rubber covering for „white
appliances
“, 1 arm swivelling
T403G-1L
Appliance Clamp without sideshift and arms with rubber covering for „ white
appliances
“, 1 arm swivelling
T413G-2L
Appliance Clamp with sideshift
and arms with rubber covering for „ white
appliances
“, 1 arm swivelling, 2 contact pads per arm
T403G-2L
Appliance Clamp without sideshift and arms with rubber covering for „ white
appliances
“, 1 arm swivelling, 2 contact pads per arm
T414-1L
Appliance Clamp with sideshift and arms with rubber covering for „ white
appliances
“, both arms swivelling
T404-1L
Appliance Clamp without sideshift and arms with rubber covering for „ white
appliances
“,both arms swivelling
T414-2L
Appliance Clamp wit
h sideshift and arms with rubber covering for „ white
appliances
“, both arms swivelling, 2 contact pads per arm
T404-2L
Appliance Clamp without sideshift and arms with rubber covering for „ white
appliances
“, both arms swivelling, 2 contact pads per arm