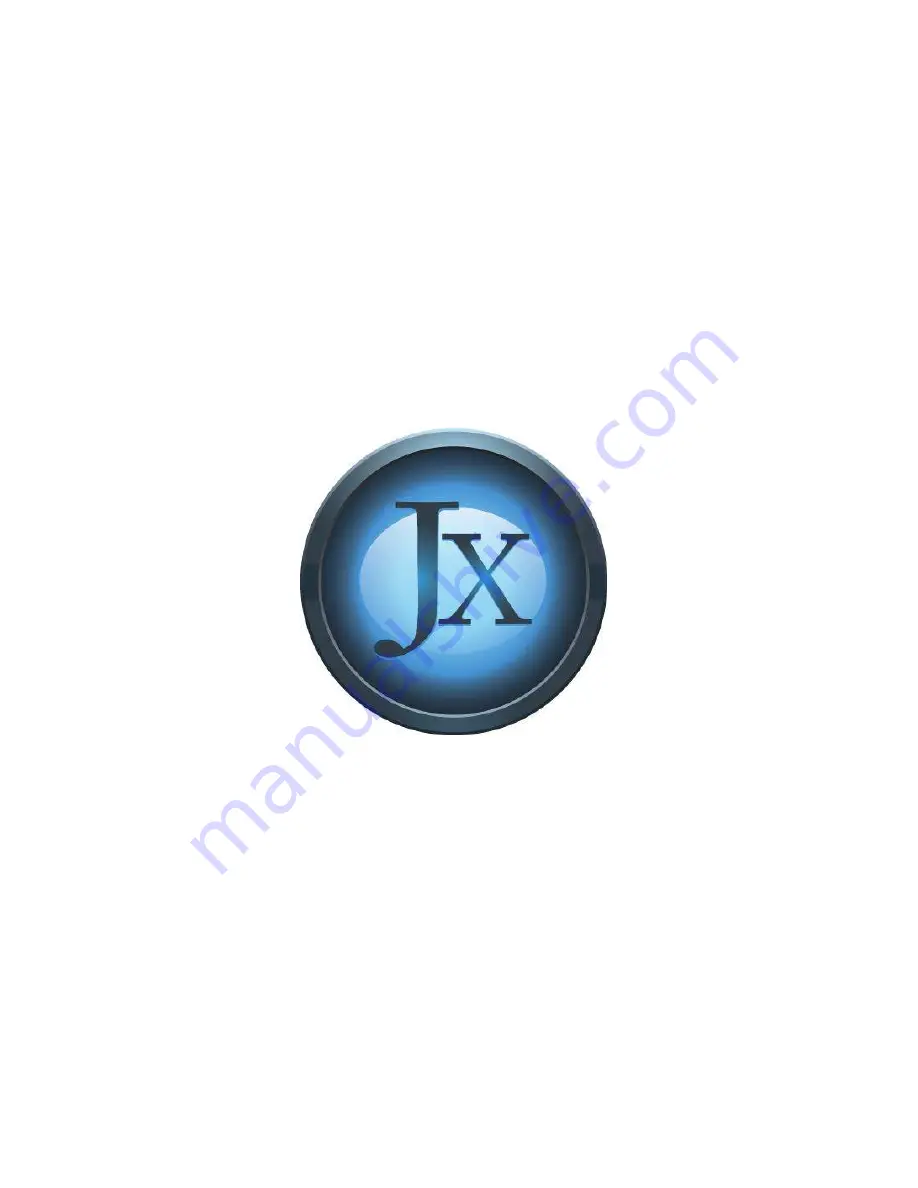
Operating Manual
Jetronix-Eco
Version 1.01
●
1/4/2013
Last edited: 01 April 2013
This document is copyright © by Jovy Systems® Limited. All rights reserved.
No part of this publication may be reproduced, transmitted, transcribed, stored in a retrieval system, or translated into any language, in any form or by any means,
electronic, mechanical, photocopying, recording, or otherwise, without prior written permission from Jovy Systems® Limited.
All copyrights, confidential information, patents, design rights and all other intellectual property rights of whatsoever nature contained herein are and shall remain
the sole and exclusive property of Jovy Systems® Limited. The information furnished herein is believed to be accurate and reliable.
However, no responsibility is assumed by Jovy Systems® Limited for its use, or for any infringements of patents or other rights of third parties resulting from its
use.
The Jovy Systems® Limited name and Jovy Systems® Limited logo are trademarks or registered trademarks of Jovy Systems® Limited.
All other trademarks are the property of their respective owners
This User Guide provides detailed guide on how to use the Jetronix-Eco Software