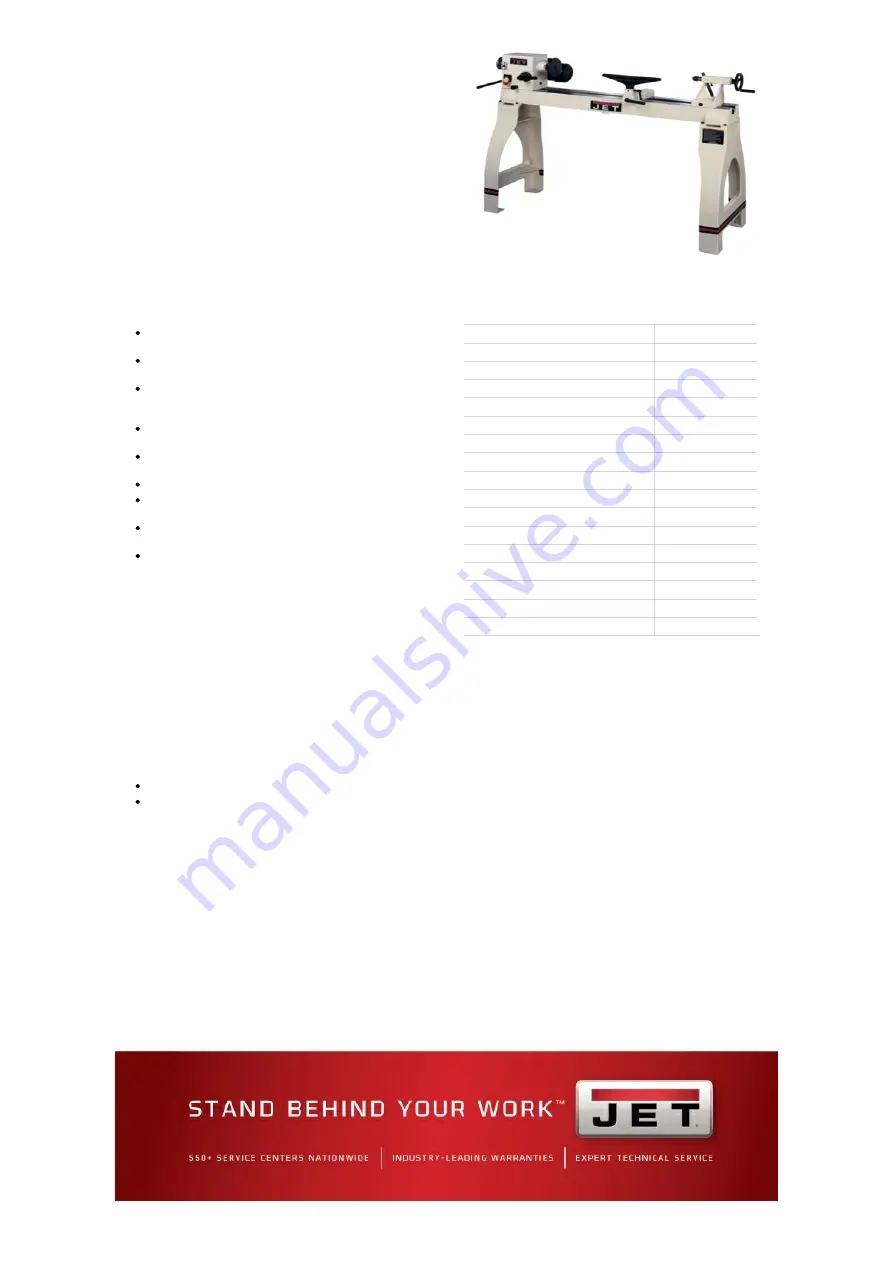
JWL-1442VSK, 14" X 42" VS
PRO WOOD LATHE WITH
LEGS
708358K
This mid range lathe offers mechanical variable speed along with a
headstock that pivot as well as slide to the end of the bed for
outboard turning capabilities
FEATURES
Reeves drive pulley system allows quick variable speed
changes from 450 to 3,000 RPM
Heavy-duty cast-iron lathe bed adds stability while limiting
vibration during operation
Headstock swivels 360° with positive stops at 45° and 90°
and may be positioned anywhere along the bed ways for
maximum flexibility and user comfort
Spindle has positive locking indexing in 10 degree
increments for fast, efficient fluting and veining operations
Built-in spindle locks let you remove or replace faceplates
and chucks with ease
Live center has a removable pin for boring through stock
Cam-lock mechanisms allow adjustments of headstock,
tailstock and tool rest base without having to use tools
Hollow tailstock allows you to perform long hole boring for
lamps and other vessels
Special cast-in webbings in legs accept 2 x 4's or a 2 x 12
to construct a solid tool or sandbag shelf
SPECIFICATIONS
Size (In.)
Style (Type)
Woodworking
Swing Over Bed (In.)
14
Swing Over Tool Rest Base (In.)
10
Distance Between Centers (In.)
42
Headstock Movement
Pivot 360, Slide
Spindle Bore (In.)
Tailstock Bore
Spindle Taper
Quill Taper
Quill Travel (In.)
Spindle Thread (In./TPI)
Outboard External Threads (In. x TPI)
Spindle Speeds
Speed Range
450-3000
Number of Indexing Positions
36
Centerline of Spindle to Floor (In.)
43-1/2
RESOURCES
Summary of Contents for 708358K
Page 26: ...25 Headstock Assembly ...
Page 29: ...28 Wiring Diagram ...
Page 31: ...30 Notes ...
Page 32: ...31 Notes ...