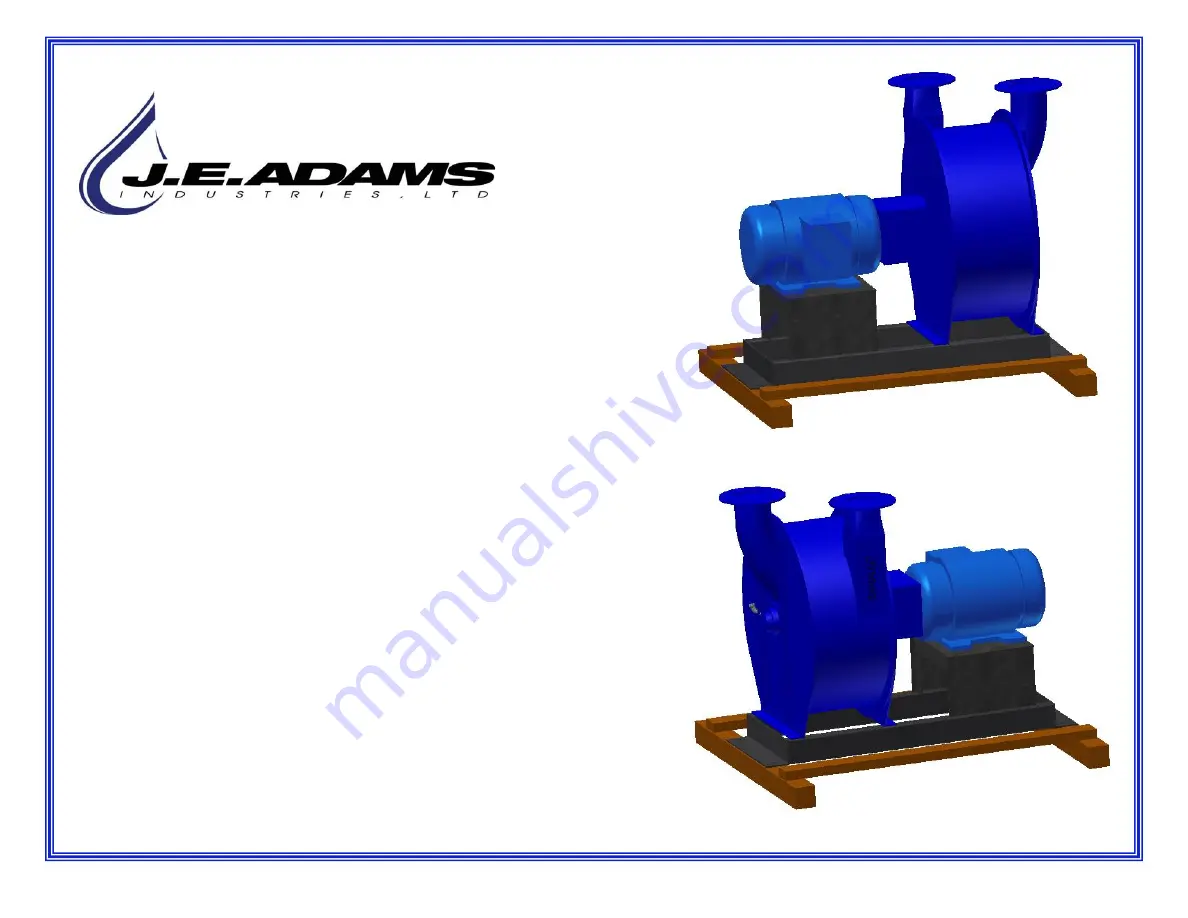
Models-
M24B & M30B Vacuum Producer
Page 2
Product Information
Page 3
Safety Instructions
Page 4 - 5
Receiving, Handling & Storage
Page 5 - 8
Installation Steps
Page 8 - 9
Pre-Startup Checks/First Startup
Page 10
Operating Temperatures
Page 11 - 13
Coupler Alignment
Page 14 - 17
Lubrication/ Bearing Replacement
Page 18
–
19
Setting Butterfly Intake Valve
Page 20 - 24
Surge and Motor Control Options
Page 25 - 34
Optional VFD and Transducer Set-up
REV 06/23/23
1