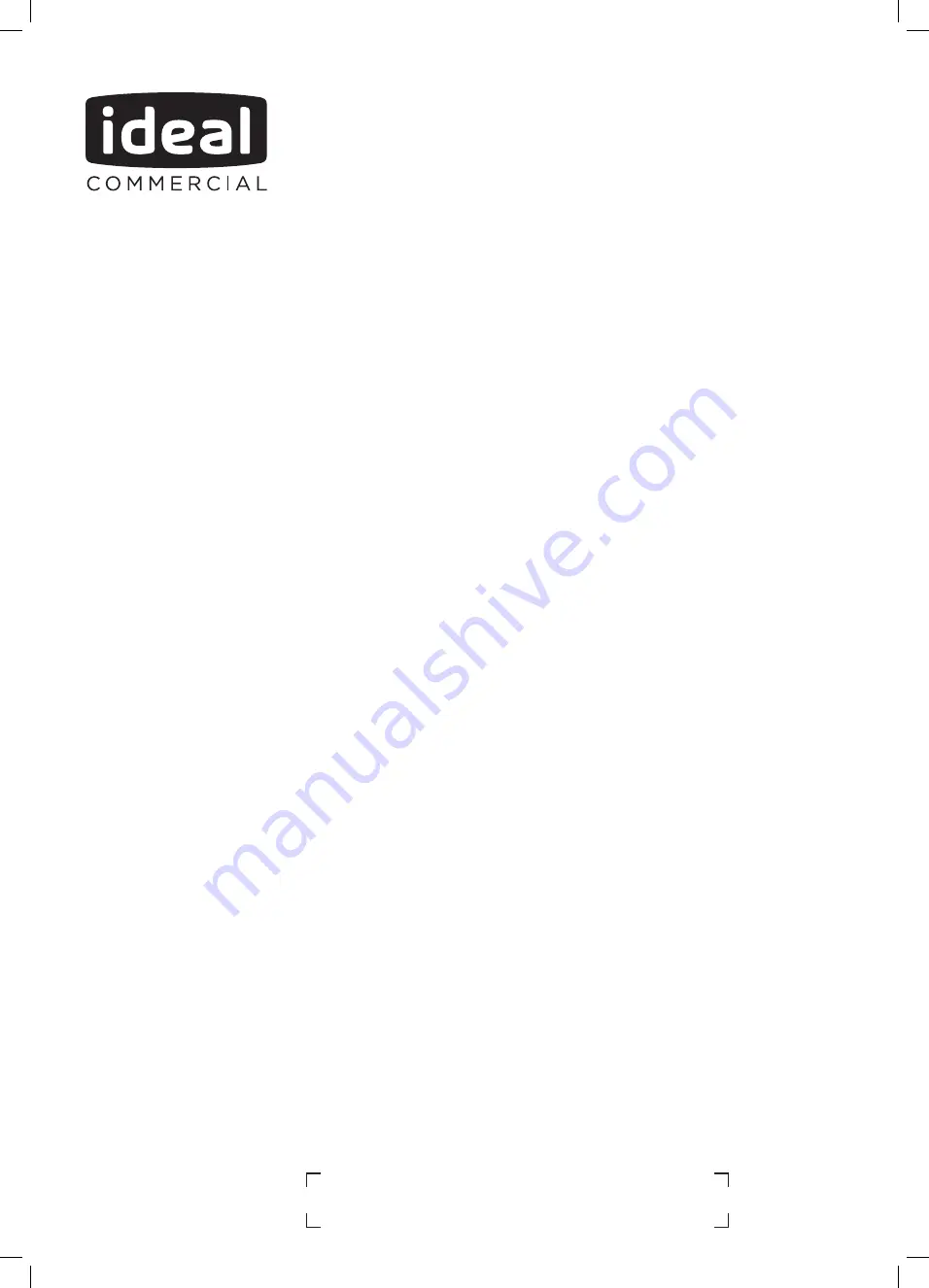
INSTALLATION AND
SERVICING
VISCOUNT
GTS
14 - 25
When replacing any part on this appliance, use only spare parts that you can be assured conform to the safety and performance
specification that we require. Do not use reconditioned or copy parts that have not been clearly authorised by Ideal.
For the very latest copy of literature for specification and maintenance practices visit our website www.idealcommercialboilers.com
where you can download the relevant information in PDF format.
June 2018
UIN 203619 A04
300014488-001-B