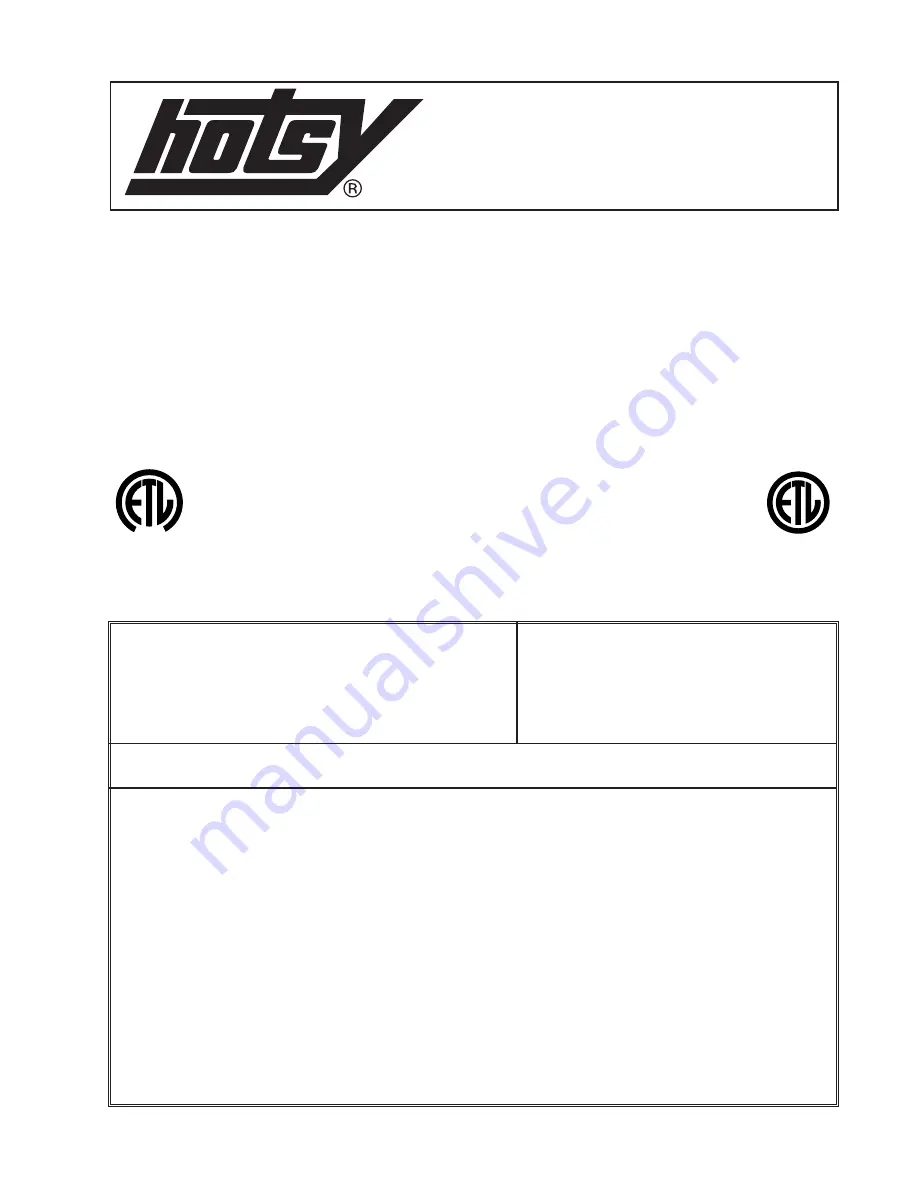
9.807-621.0
SERIAL NUMBER:
DATE PURCHASED:
FOR SALES AND SERVICE, PLEASE CONTACT:
®
c
LISTED
®
OPERATING INSTRUCTIONS AND PARTS MANUAL
Thank you for purchasing a Hotsy Pressure Washer. This manual covers the operation and mainte-
nance of your pressure washer. All information in this manual is based on the latest product informa-
tion available at the time of printing. Hotsy, Inc. reserves the right to make changes at any time with-
out incurring any obligation.
Read instructions carefully before attempting to assemble, install, operate or service this pressure
washer. Failure to comply with instructions could result in personal injury and/or property damage!
MODELS 965SS, 1065SS,
1065SSE, 1075SSE