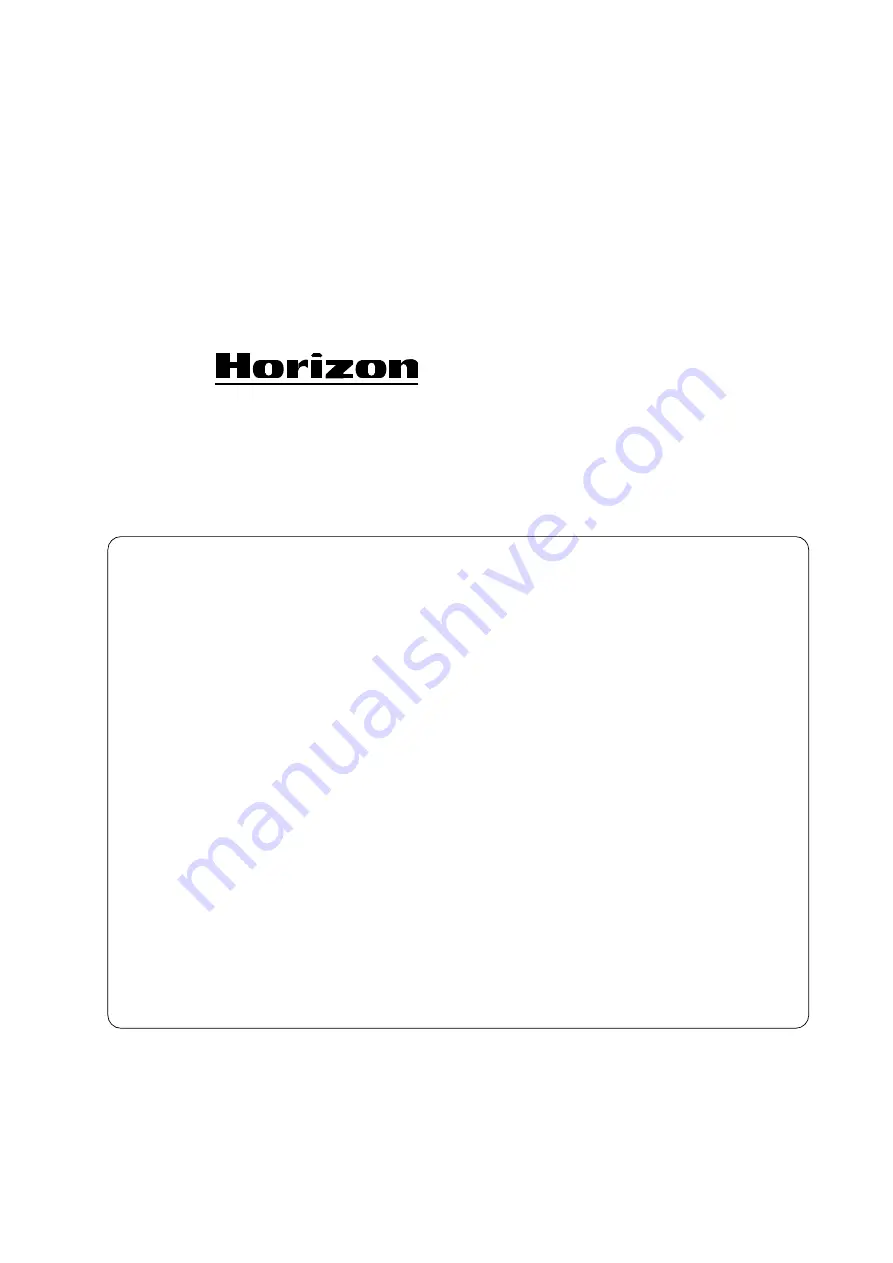
I
STITCHER & FOLDER
SPF-10
II
Important Information
- This manual is designed to help you to install, operate and maintain Stitching and Folding
System SPF-10II. Read, understand and keep this manual in a safe and convenient place.
- Do not operate SPF-10II until you read and understand the instructions in this manual.
- Horizon International Inc. shall not be liable for incidental consequential damages resulting
from : improper or inadequate maintenance by customer; unauthorized modification or misuse;
operation outside of the environmental specifications for the product.
- Horizon International Inc. pursues a policy of continuing improvement in design and perfor-
mance of the product. Therefore, the product design and specifications are subject to change
without prior notice and without our legal obligation.
- All rights are reserved. No part of the manual may be photocopied, reproduced or translated to
another language without the prior written consent of Horizon International Inc.
000927/SPF10II/01E/DV
UM201008-01
Summary of Contents for SPF-10II
Page 18: ...14 1 Before You Begin ...
Page 32: ...28 2 Operation Procedure ...
Page 37: ...33 4 Maintenance 4 Maintenance 4 1 Lubrication 34 4 2 Cleaning 34 4 3 Replacement 35 ...
Page 40: ...36 4 Maintenance ...
Page 43: ...39 6 Installation Instruction 6 Installation Instruction 6 1 Installation Instructions 40 ...
Page 50: ...46 6 Installation Instruction ...