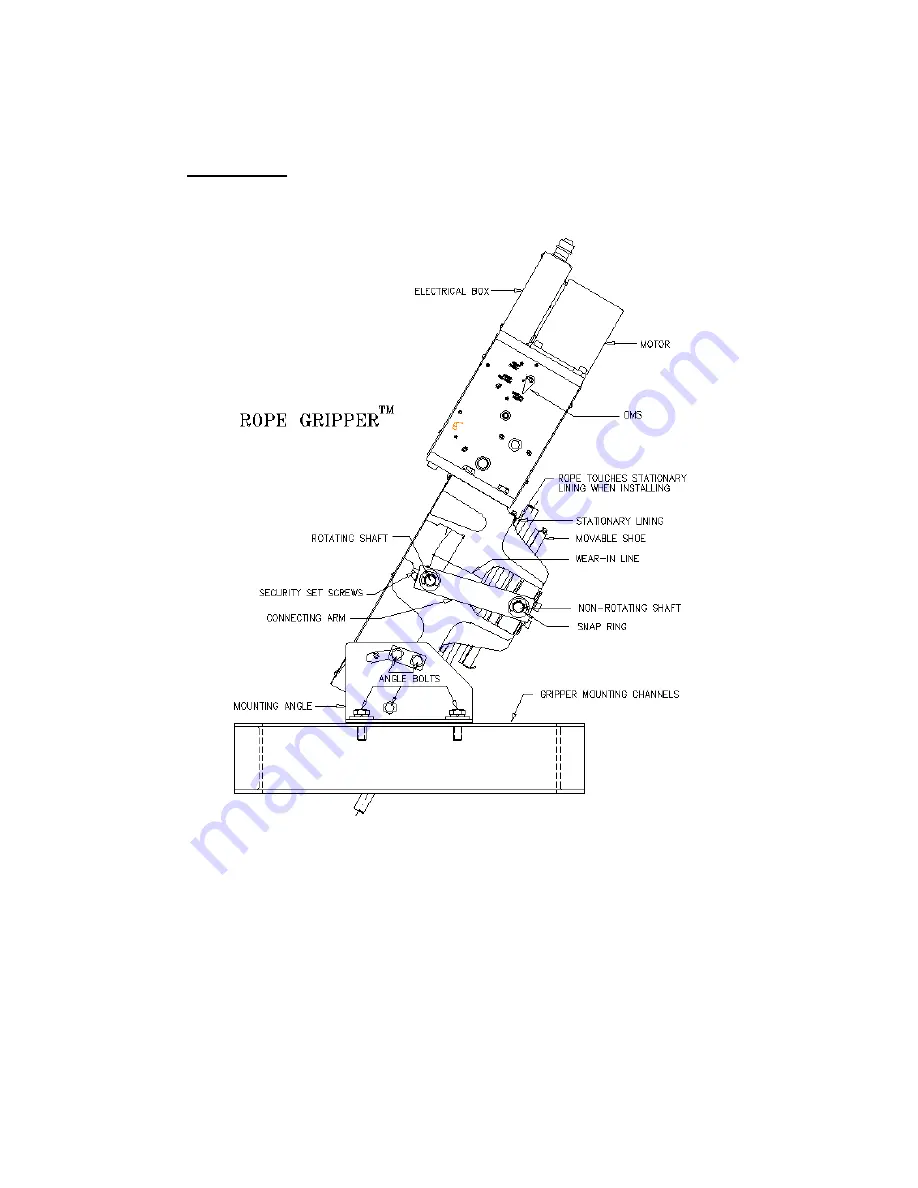
BULLETIN 1166
9/4/2015
Page 1 of 20
HOLLISTER-WHITNEY “ROPE GRIPPER™”
Instructions for Model #622GA1, 622GA2,
(US PATENT 8,511,437)
WARNING:
KEEP HANDS CLEAR OF “ROPE GRIPPER™”.
FORCES CREATED CAN CRUSH FINGERS.
Figure 1 - 622G Rope Gripper
TM
“ROPE GRIPPER
TM
” MOUNTING CHANNELS GUIDELINES
The Mounting Channel Framework supporting the “ROPE GRIPPER™” must withstand
upward and downward forces according to Table 1 (page 4) and applicable code
requirements.
The Mounting Channel Framework must be sufficiently sized to securely hold the “ROPE
GRIPPER™” and elevator while preventing any sliding. The Traction Machine must also be
prevented from sliding. See Figure 2 and Figure 3 for suggested mountings.
When adding a “ROPE GRIPPER™” to an existing installation, it may not be possible to
mount the gripper in the machine room. It is acceptable to mount the gripper horizontally or
upside down, as long as proper consideration for access is given for future gripper
maintenance and opening the gripper manually.