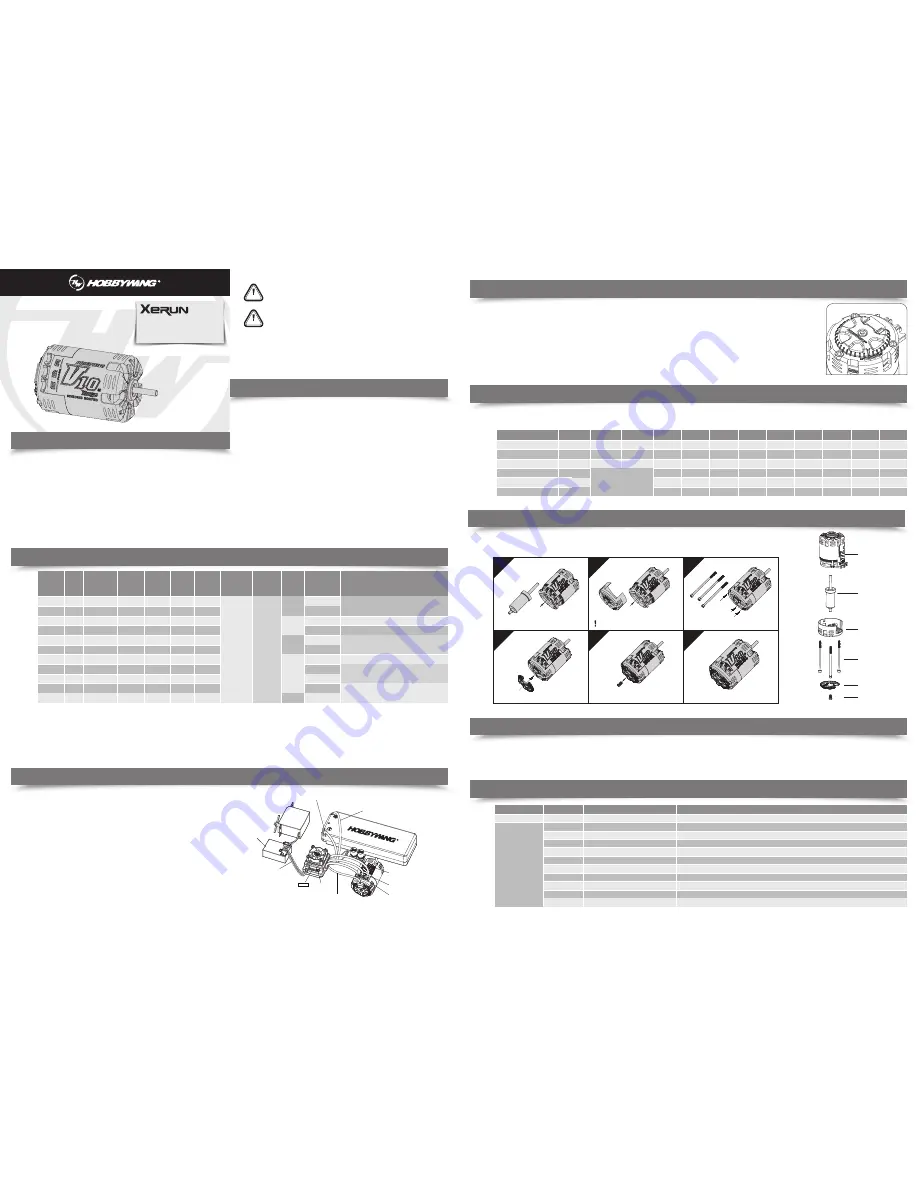
02
Features
• Designed to withstand extreme levels of use at its highest peak performance.
• Complete new CNC cut motor case with extra front spoke ventilation slots.
• Works as a sensored unit and also sensorless without the sensor cable attached.
• Selectable mechanical timing of 30 to 60 degrees for STOCK motors (*10.5-25.5T) and 20 to
50 degrees for non-STOCK motors (*3.5-8.5T).
• Minimal maintenance is required with precise machining technology which ensures a
minimum tolerance end play of the rotor shaft. Eliminating the copper shims used in most of
today’s motors.
• 200
℃
high temperature tolerance and high purity copper windings maximize conductivity
and reliability.
• 200
℃
high temperature tolerance sintered NdFeb (Neodymium, 35EH-LT) magnets.
• Extreme low resistance multi-layered outlet PCB and high RPM NSK bearings.
• Compliant with ROAR, IFMAR, BRCA and JMRCA rules, certificated by RoHS, CE, FCC etc.
04
INSTALLATION AND CONNECTIONS
• Install the motor in its mount using M3 screws no longer than 8mm.
• There are 3 power wires coming from the ESC must be soldered to the motor.
They are usually color coded as Blue for Wire A, Yellow for Wire B and Orange
for Wire C. When connecting the power wires between the ESC and motor,
please make sure that you match ESC Wire A to Motor Phase A, ESC Wire B to
Motor Phase B and ESC wire C to Motor Phase C (This is VERY important).
• When using sensored ESC, make sure the sensor cable is clean and reliable.
Connect the sensor cable to both ESC and motor in the correct direction.
• Double check you have all the connections correct before turning on the ESC
(See connection diagram as below).
Sensor wire
Blue power wire
(motor phase “A”)
Yellow power wire
(motor phase “B”)
Orange power wire
(motor phase “C”)
Switch
ESC
Input TH
Channel
(Ch.2)
Receiver
Servo
Battery Positive (Red)
Battery Negative (Black)
- + S
01
CAUTIONS
CAUTIONS
ATTENTION
USER MANUAL
V10 G2
05
TIMING ADJUSTMENT
• To adjust the timing, simply loosen the 1 short screws on the back of the motor and rotate the Sensor Module Cover, noting the white-color lines
on the motor and the mark (pointer) on the cover. After the adjustment, please lock the 2 short screws.
• You can alter the timing on the motor to change the power-band and characteristics of the motor for best and the most efficient performance.
The factory timing for STOCK motors (*10.5-25.5T) is 40 degrees, for non-STOCK motors (*3.5-8.5T) is 30 degrees. You can reduce the timing by
turning the end cap clockwise, increase the timing by turning the end cap counter clockwise.
• Increasing the timing will increase the RPM of the motor whilst at the same time increasing temperatures and losing efficiency. Higher timing will
require a softer gear ratio. We recommend you start with this setting and adjust based on your needs from that position.
• When setting your motor timing it is important to make sure your ESC is also set correctly. Please follow your ESC instructions on how to do this.
To check the motor temperatures during testing, simply drive for 3 laps of the track, stop and use an infrared temperature measuring instrument
to make sure the motor is not too hot. If the motor is too hot then allow the motor to cool before trying it again.
OPTIONS
30820001
30820002
30820005
30820006
30820007
30820008
30820009
30820012
30820013
30820014
30820015
XERUN-V10-Rotor-
Φ
5-12.3
XERUN-V10-Rotor-
Φ
5-12.5F
XERUN-V10-Rotor-
Φ
5-12.5
XERUN-V10-Rotor-
Φ
7-12.5
XERUN-V10-Rotor-
Φ
5-13.0
XERUN-V10-Rotor-
Φ
5-13.5
XERUN-V10/Bandit-Rotor-
Φ
5-12.1
XERUN-V10-Rotor-
Φ
5-12.5-U-T
XERUN-V10-Rotor-
Φ
7-12.3-U
XERUN-V10-Rotor-
Φ
7-12.5-U
PN
Spare Part
Description
Specification
Ball bearing
540 MOTOR BEARING-3.175
R2ZZ Ball Bearing, 3.175x9.525x3.967mm
Thick magnet, w/o cooling fan, magnet hole Ø5, O.D. of the magnet:12.3mm
Thick magnet, with cooling fan, magnet hole Ø5, O.D. of the magnet:12.5mm
Thick magnet, w/o cooling fan, magnet hole Ø5, O.D. of the magnet:12.5mm
Thin magnet, w/o cooling fan, magnet hole Ø7, O.D. of the magnet:12.5mm
Thick magnet, w/o cooling fan, magnet hole Ø5, O.D. of the magnet:13.0mm
Thick magnet, w/o cooling fan, magnet hole Ø5, O.D. of the magnet:13.5mm
Thick magnet, w/o cooling fan, magnet hole Ø5, O.D. of the magnet:12.1mm
Thick magnet / titanium-alloy shaft, w/o cooling fan, magnet hole Ø5, O.D. of the magnet:12.5mm
Thin magnet / strong magnet, w/o cooling fan, magnet hole Ø7, O.D. of the magnet:12.3mm
Thin magnet / strong magnet, w/o cooling fan, magnet hole Ø7, O.D. of the magnet:12.5mm
Rotor
09
• The “Max. Output Power” is measured with 7.4V input voltage and ESC at ZERO timing. This parameter is neither the “maximum input power” nor the “rating power”, it is calculated
by “RPM x Torque / 9550”. Because each factory runs a different testing platform, the above data may vary if the motor is tested in different factories running different testing platforms.
Attention: The “Output Power” value shouldn’t be compared with the “Input Power” value directly because the motor efficiency is always less than 100%, the value of
“Output Power” is always smaller than the “Input Power” .
• The “Current at Peak Output Power” is a guide used for selecting the suitable power system (ESC, Motor, Gear ratio, etc.) If the actual input current of the power system is bigger than
the peak parameter stated in the above table, this means that the power system settings/configuration is over its peak (Or in other words, “overloaded”)
• The “KV” is measured without any load on the motor and ESC at ZERO timing. Please don’t run the motor without load for long periods of time (1 minute), otherwise the motor may
overheat.
03
SPECIFICATIONS
30401100
30101101
30101102
30101103
30101104
30101105
30101106
30101107
30401108
30101109
30401101
9550KV
0.002
Ω
8.4A
600W
120A
7600KV
0.0032
Ω
6.6A
500W
115A
5800KV
0.0045
Ω
6.5A
470W
110A
5000KV
0.0062
Ω
5.5A
430W
105A
4550KV
0.0088
Ω
3.8A
380W
97A
4050KV
0.0106
Ω
3.2A
360W
90A
3800KV
0.0163
Ω
2.1A
260W
74A
3000KV
0.0265
Ω
1.8A
220W
59A
2300KV
0.0457
Ω
1.3A
150W
41A
1900KV
0.072
Ω
1.1A
120W
32A
PN
Φ
5-12.3
Φ
5-13.0
Φ
5-12.5
Φ
7-12.5-U
Φ
7-12.3-U
KV
Without Load
(RPM/V)
Resistance
Current
Without
Load
Max.
Output
Power
Current
@Max.
Output
Power
Dia. & Length
Dia. of
External
Shaft
Stock
Rotor
Application
1/10 on-road Modified;1/10 4WD off-road Modified
1/10 4WD off-road Modified
1/10 Drift; 1/10 on-road Stock
1/10 Stock;1/10 rock crawler
1/10, 1/12 on-road Modified
1/10 on-road Stock
1/10 Drift; 1/10 2WD off-road Modified
3.5T
4.5T
5.5T
6.5T
7.5T
8.5T
10.5T
13.5T
17.5T
21.5T
Model
25.5T
1500KV
0.0531
Ω
0.8A
85W
24A
Weight
Ø=36mm
(1.417in)
L=52.5mm
(2.067in)
Ø=3.17mm
(0.125in)
L=15mm
(0.575in)
178g (6.279oz)
178g (6.279oz)
181g (6.385oz)
181g (6.385oz)
172g (6.067oz)
178g (6.279oz)
170g (5.997oz)
172g (6.067oz)
173g (6.102oz)
170g (5.997oz)
166g (5.855oz)
GEARING
06
3.5T
4.5T
5.5T
6.5T
7.5T
8.5T
10.5T
13.5T
17.5T
21.5T
11.0:1
9.5:1
8.5:1
8.0:1
7.6:1
7.0:1
5.5:1
4.7:1
4.0:1
3.5:1
25.5T
3.2:1
2.7:1
66mm
5.2:1
5.2:1
6.2:1
10.5:1
8.5:1
7.5:1
7.0:1
6.6:1
6.3:1
5.0:1
4.0:1
3.5:1
3.0:1
25mm
29mm
32mm
35mm
36mm
38mm
42mm
51mm
66mm
66mm
11.1:1
10.3:1
9.4:1
8.5:1
8.0:1
7.0:1
6.0:1
5.5:1
12.0:1
10.8:1
9.8:1
8.9:1
8.0:1
7.0:1
6.0:1
5.5:1
13.5:1
12.6:1
11.5:1
10.4:1
9.0:1
8.0:1
7.0:1
6.5:1
1/10 on-road (Small track)
1/10 on-road (Big track)
1/12 on-road
2WD off-road
4WD off-road
Truggy
Class
Not Available
7.4V LiPo
7.4V LiPo
3.7V LiPo
7.4V LiPo
7.4V LiPo
7.4V LiPo
Battery
Below is a very rough idea of starting gear ratios for the motors. Please be aware that these are guide ratios for ESC with ZERO timing. Please always check with other drivers using the
same ESC/Motor combination at your track for a good starting point. If you have no idea about what gear ratio is most suitable for your car, please begin with “softer” gearing and then
adjust as needed.
Thanks for purchasing Hobbywing Xerun V10 Sensored Competition Motor. High
power motor can be very dangerous, so please read through this manual carefully.
Given that we have no control over the correct use, installation, application, or
maintenance of our products, no liability shall be assumed nor accepted for any
damages, losses or costs resulting from the use of the product.
Any claims arising from the operating, failure or malfunctioning etc. will be
denied. We assume no liability for personal injury and/or consequential damages
resulting from our product or our workmanship. As far as is legally permitted, the
obligation to compensation is limited to the invoice amount of the affected
product.
We, HOBBYWING, are only responsible for our product cost and nothing else as
result of using our product.
PARTS LIST
08
The XERUN V10 G2 Motor has the parts as below (Please also check picture 5 for reference).
1) Ball bearing x 1 (13.175x9.525x3.967mm)
2) Rotor x 1
3)Front casing x 1
4) Metal Bottom Case (w/ Sensor Module) x 1 5) Long screws x 3 (M2.50x45mm)
6) Cover of sensor module x 1
7)Short screws 1 (M2.50x6.0mm) 8) Sensor wires x 2 (80mm, 200mm)
• Avoid incorrect connections between the electronic speed controller (ESC) and the
motor.
• All wires and connections should be well insulated. Short-circuits can possibly damage
the products.
• Never allow this product or other electronic components to come in contact with
water, oil, fuel or other electro-conductive liquids. If this happens, stop the use of
your product immediately and let it dry carefully.
• Avoid overloading the motor due to wrong or too aggressive gear ratios. Different
ESCs have different internal timings, follow the ESC instructions.
• Never apply full throttle if the pinion is not installed. Due to the extremely high RPMs
without load, the motor can get damaged.
• Always wire up all the parts of the equipment carefully. If any of the connections
come loose as a result of vibration, your model RC may lose control.
• Avoid soldering longer than 5 seconds at each soldering joint when replacing the
power wires to prevent possible damage to the product due to overheating of the
components. Use a high power soldering station with at least 60W for soldering.
• Never allow the motor case to get over 100 degrees Celsius (212 degrees Fareheit)
because the magnets maybe demagnetized by high temperature.
20170110
07
The XERUN V10 G2 Motor is very strong in construction but also easy to disassemble for maintenance.
We recommend periodical checking of the bearings and to clean the motor of dirt.
Please follow the steps in below to assemble the motor. When disassembling the motor, the sequences are reversed.
ASSEMBLY AND DISASSEMBLY
Rotor x1
Front casing x1
Bottom casing x1
Long screws x3
M2.50 x 45mm
Sensor module
cover x1
Short screws x1
M2.50 x 6.0mm
4. Install the cover of sensor module
5. Tighten the screws to lock the cover of
sensor module
6. Motor assembled
1. Install the rotor
3. Install the long srews
2. Install the bottom casing
*The bulge on the sensor module should
aim at the notch on the bottom casing.
1
2
3
4
5
6