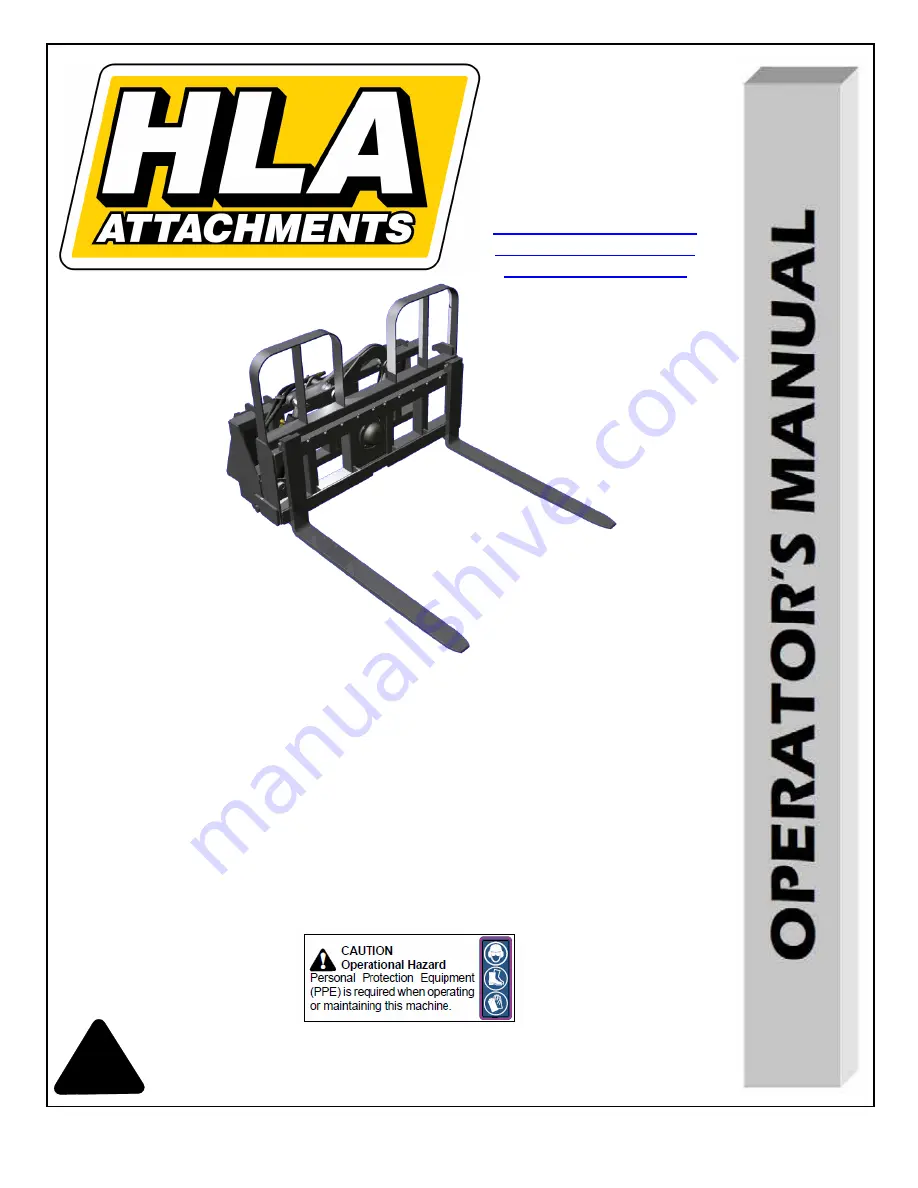
!
Do not attempt to operate the equipment without thoroughly
reviewing this manual for safe and proper operation.
Rev
280820
HA001
11
RRG Series Root Grapples Manual.050918
PRINTED IN CANADA
HDR
Series
Rotating Pallet Fork
HDR5548
HDR2042 · HDR4242 · HDR4248 · HDR5542
HDR5548 · HDR5554 · HDR20 · HDR42 · HDR55
Keep this manual with the machine at all times
HORST WELDING
8082 Rd 129
Listowel, ON N4W 3G8
Canada
519-291-4162
1-866-567-4162
Fax 1-519-291-5388
Summary of Contents for HDR Series
Page 2: ... 0 ...