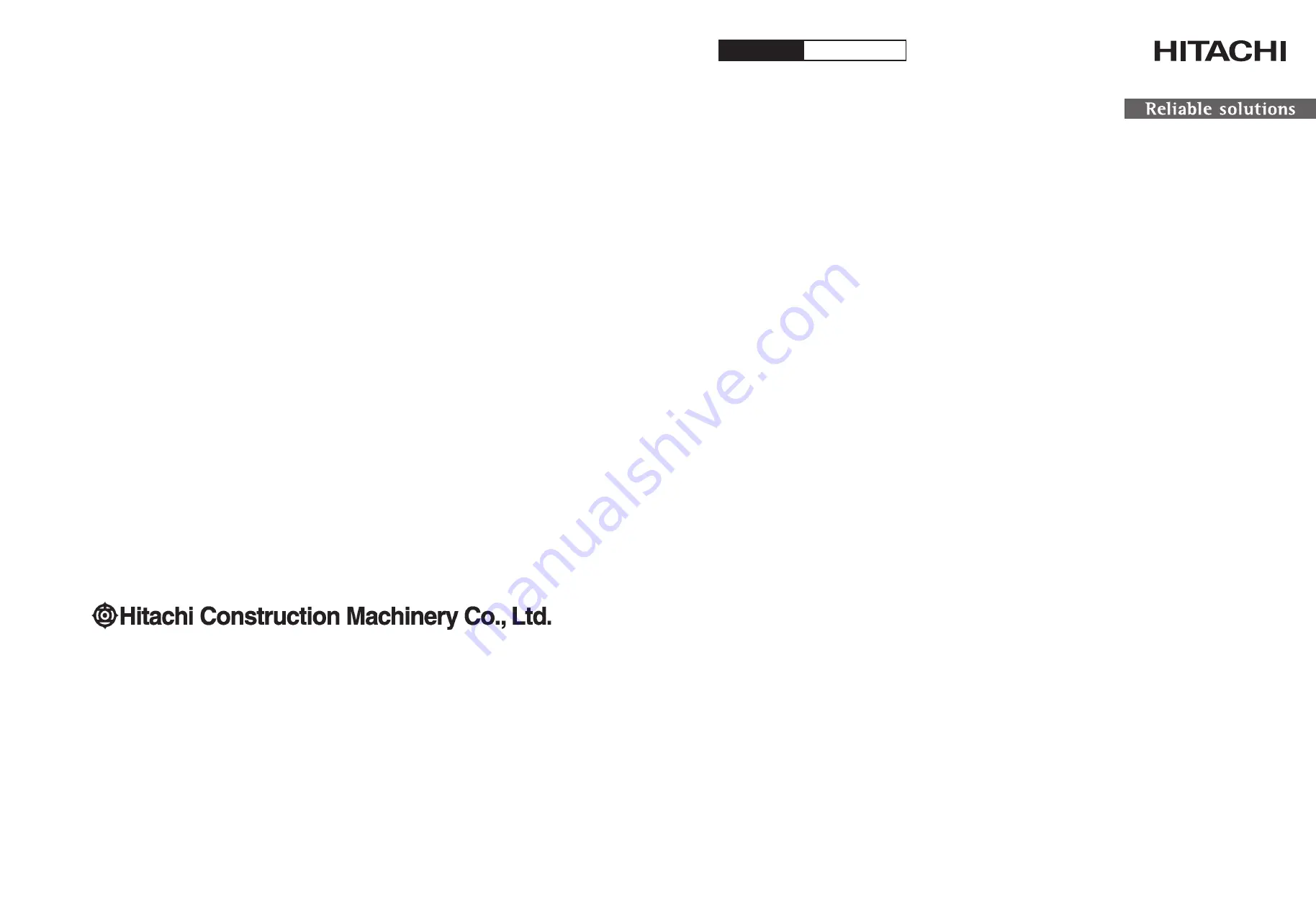
ZX1
70W
-5A
WLBJE0-EN-00
ZX170W
-5A
WHEELED EXCA
VA
TOR WORKSHOP MANUAL
PRINTED IN JAPAN (K) 2018, 05
Service Manual consists of the following separate Part No.
Technical Manual (Operational Principle)
: Vol. No.TOLBJE0-EN
Technical Manual (Troubleshooting)
: Vol. No.TTLBJE0-EN
Workshop Manual
: Vol. No.WLBJE0-EN
Engine Manual
: Vol. No.ETDCY-EN, EWDCY-EN
WLBJE0-EN-00
PART NO.
Wheeled Excavator
Workshop Manual
URL:http://www.hitachi-c-m.com
Summary of Contents for ZX170W-5A
Page 2: ......
Page 6: ...SYMBOL AND ABBREVIATION SY 2 Blank WLBJE0 EN 00 ...
Page 48: ...WLBJE0 EN 00 ...
Page 50: ...WLBJE0 EN 00 ...
Page 52: ...LBJE0W 1 2 Blank WLBJE0 EN 00 ...
Page 61: ......