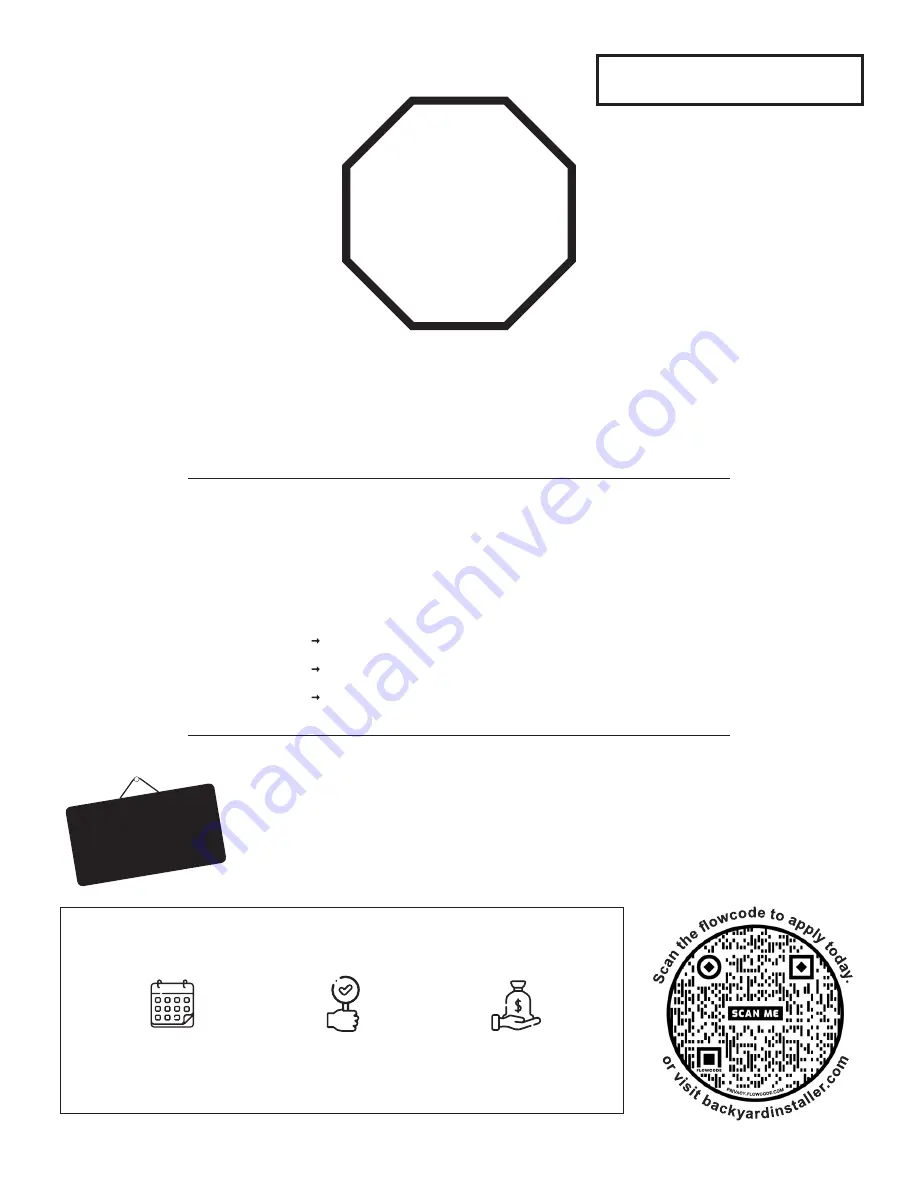
16778-G
Call Us First!
DO NOT RETURN TO STORE.
For questions on assembly or for general inquiries, you may contact us in the following ways:
Call customer service:
1-877-743-3400
Did you enjoy building your shed?
JOIN OUR TEAM
AND MAKE UP TO $1,500/WEEK*
STOP!
Flexible schedule
No selling,
just building
Bonus incentives
available
INSTALLERS
WANTED
*based on number of completed installations
Call a Recruiter Today! 734-365-7000
visit us online at
help.backyardproducts.com
AVOID THE WAIT!
Submit a help request
Answers to frequently asked questions
Live chat with an agent