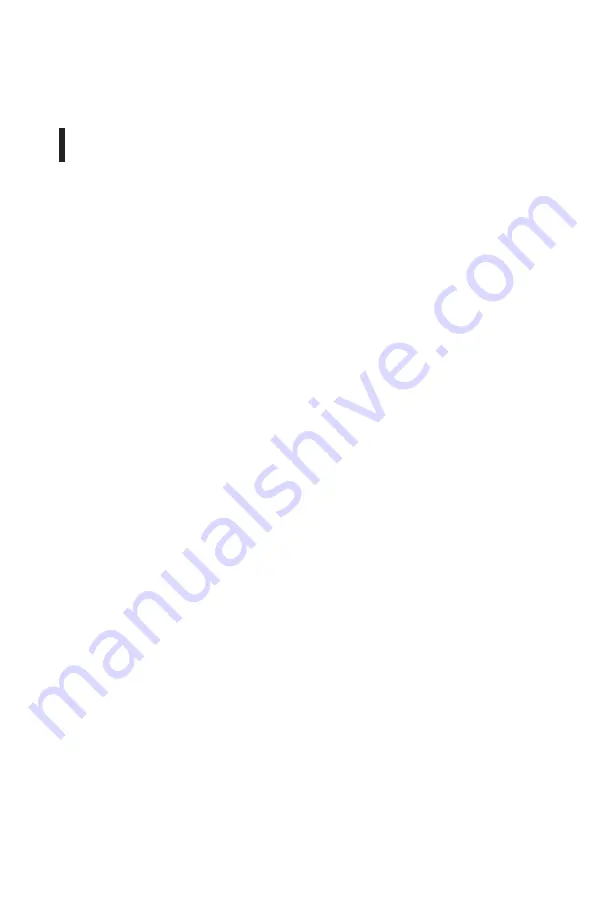
Manual No. 115N
61-00-15
Revision 24
December 2020
Propeller Owner's Manual
and Logbook
“Compact” Models with Aluminum Blades
Constant Speed, Non-Counterweighted
( )HC-( )( )Y( )-1( )
Constant Speed, Counterweighted
( )HC-( )( )Y( )-4( )
Constant Speed and Feathering
( )HC-( )( )Y( )-2( )
Constant Speed and Feathering, Turbine
( )HC-( )( )Y( )-5( )
Hartzell Propeller Inc.
One Propeller Place
Piqua, OH 45356-2634 U.S.A.
Ph: 937-778-4200 (Hartzell Propeller Inc.)
Ph: 937-778-4379 (Product Support)
Product Support Fax: 937-778-4215