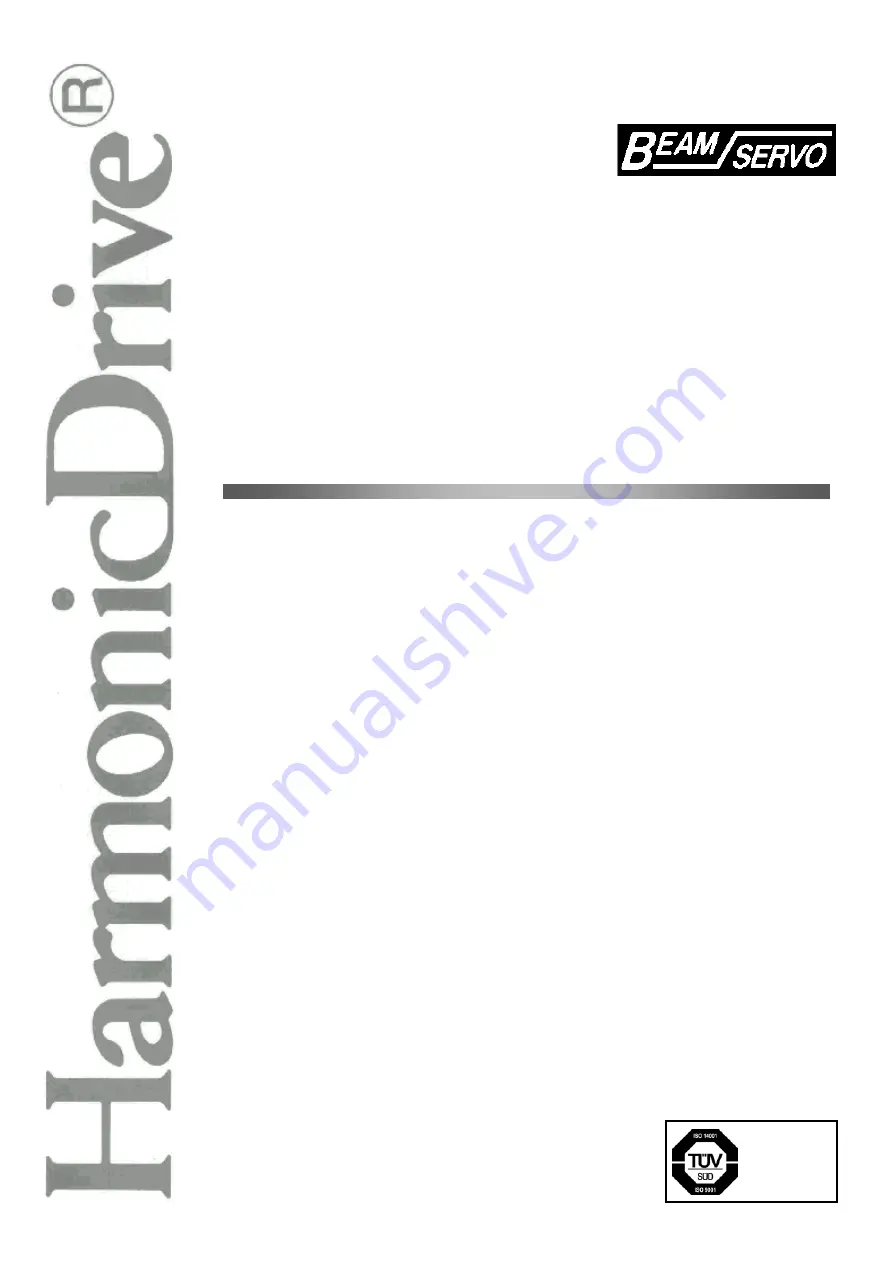
Galvanometer Scanner System
LSA-10A-30-D-130
Technical Document
(Scanner: LSA-10A-30/Driver: PSM-130)
● We thank you for purchasing the Galvanometer Scanner
LSA Series
System.
● Any mishandling or misuse of this product may result in unexpected
accidents and shorten the life of the product. Please read this
document thoroughly and use accordingly to ensure safe prolonged
use.
● Product specifications are subject to change without notice for
improvement purposes.
● Keep this manual in a convenient location and refer to it whenever
necessary in operating or maintaining the units.
● The end user of the actuator should have a copy of this manual.
ISO14001
ISO9001