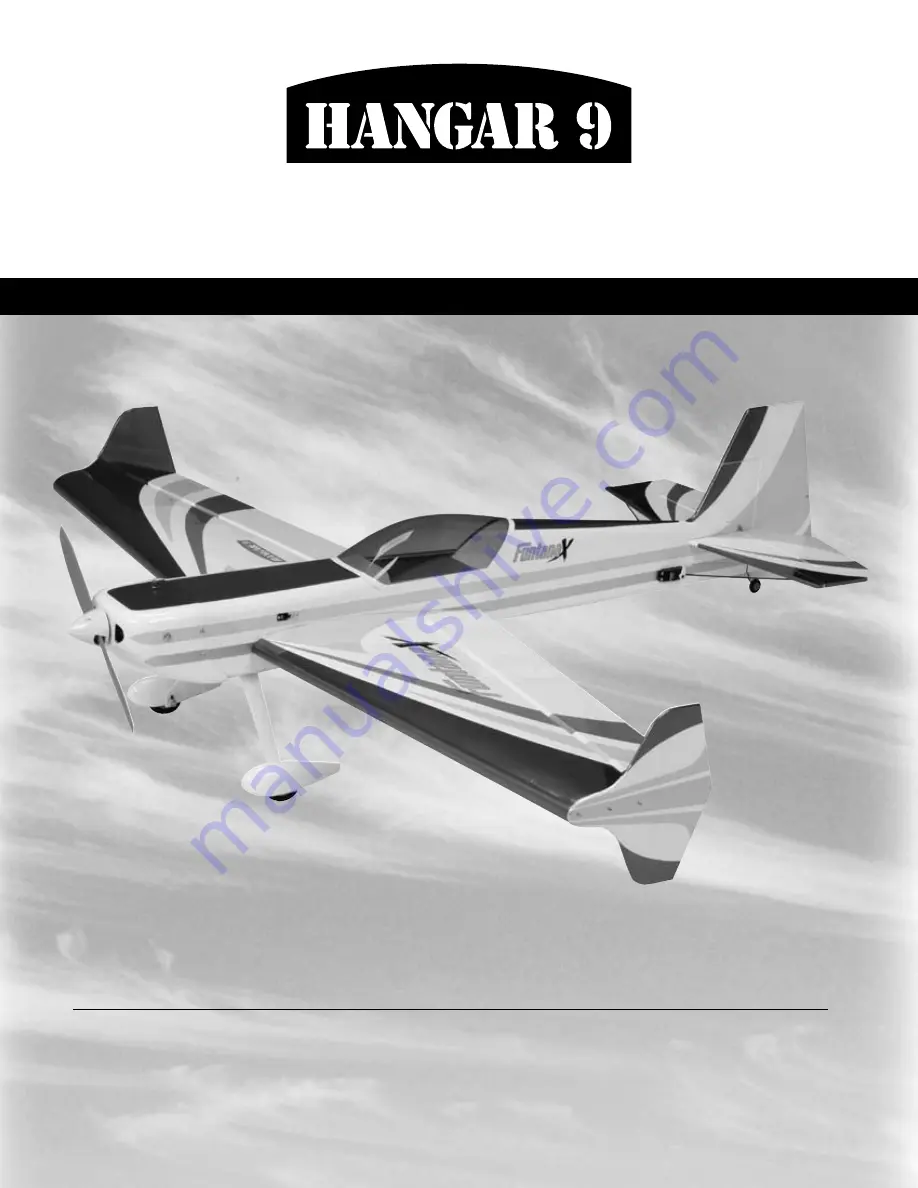
Wingspan: ..................................... 56 in (1422mm)
Length: .......................................... 56 in (1441mm)
Wing Area: ......................... 714 sq in (46.1 sq dm)
Assembly mAnuAl
FuntanaX 50 ARF
Weight: ............................ 4–5.5 lb (1.8 kg–2.5 kg)
Radio: .................................. 4-channel w/5 servos
Engines: ........... 32–.46 2-stroke, .40–.72 4-stroke
Specifications
5.
Summary of Contents for FuntanaX 50
Page 33: ...33 Notes ...