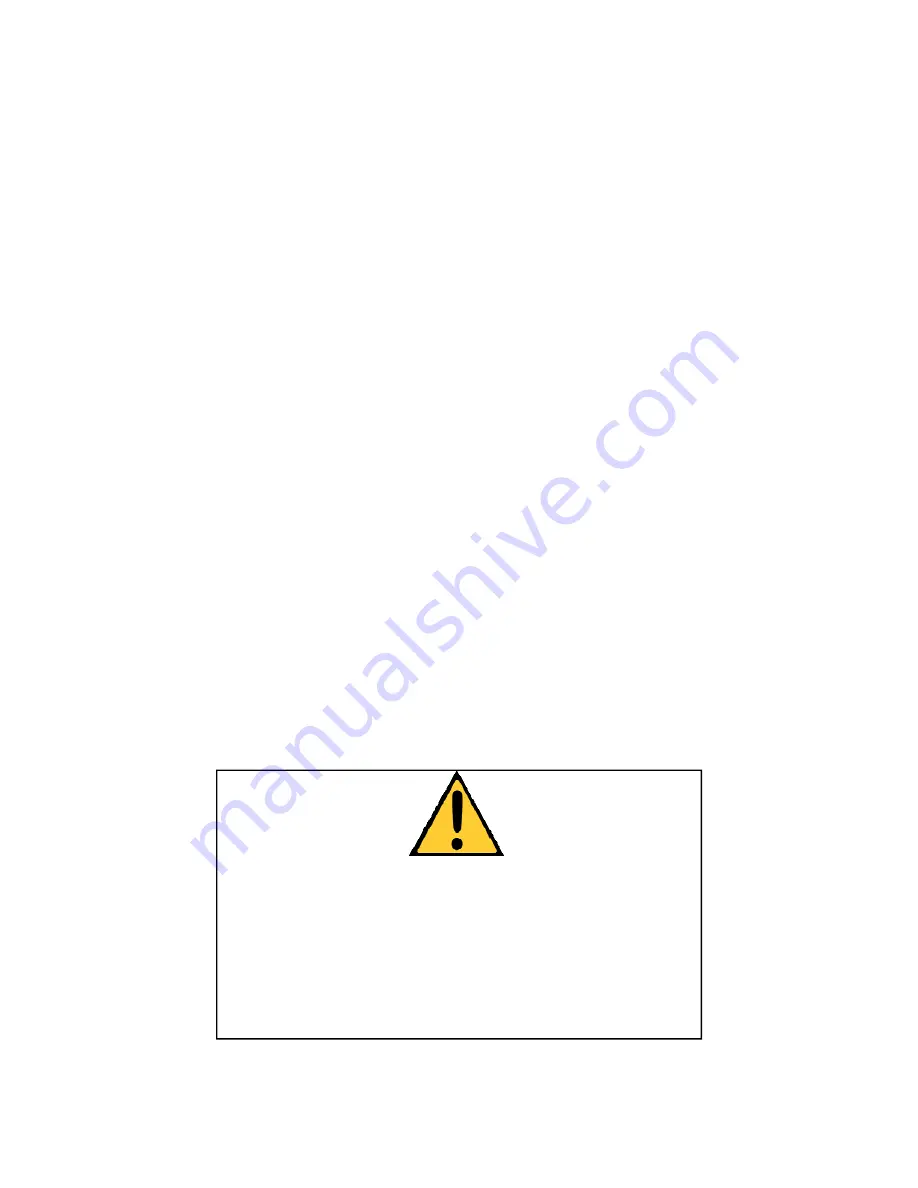
CALIFORNIA
Proposition 65 Warning
WARNING: Diesel engine exhaust and
some of its constituents are known to the
State of California to cause cancer and
birth defects or other reproductive harm.
WARNING: Battery posts, terminals, and
related accessories contain lead and lead
compounds, chemicals known to the State
of California to cause cancer and birth
defects or other reproductive harm.
ANY PICTURES CONTAINED WITHIN THIS OPERATOR’S
MANUAL THAT DEPICT SITUATIONS WITH SHIELDS, GUARDS,
RAILS, OR LIDS REMOVED ARE FOR DEMONSTRATION
PURPOSES ONLY. HAGIE MANUFACTURING COMPANY
STRONGLY URGES THE OPERATOR TO KEEP ALL SHIELDS
AND SAFETY DEVICES IN PLACE AT ALL TIMES.
Summary of Contents for UpFront DTS 8T
Page 99: ...93 VIII TROUBLE SHOOTING NOTES...
Page 101: ...2007 Hagie Manufacturing Company Clarion Iowa USA NOTES NOTES...
Page 102: ...96...