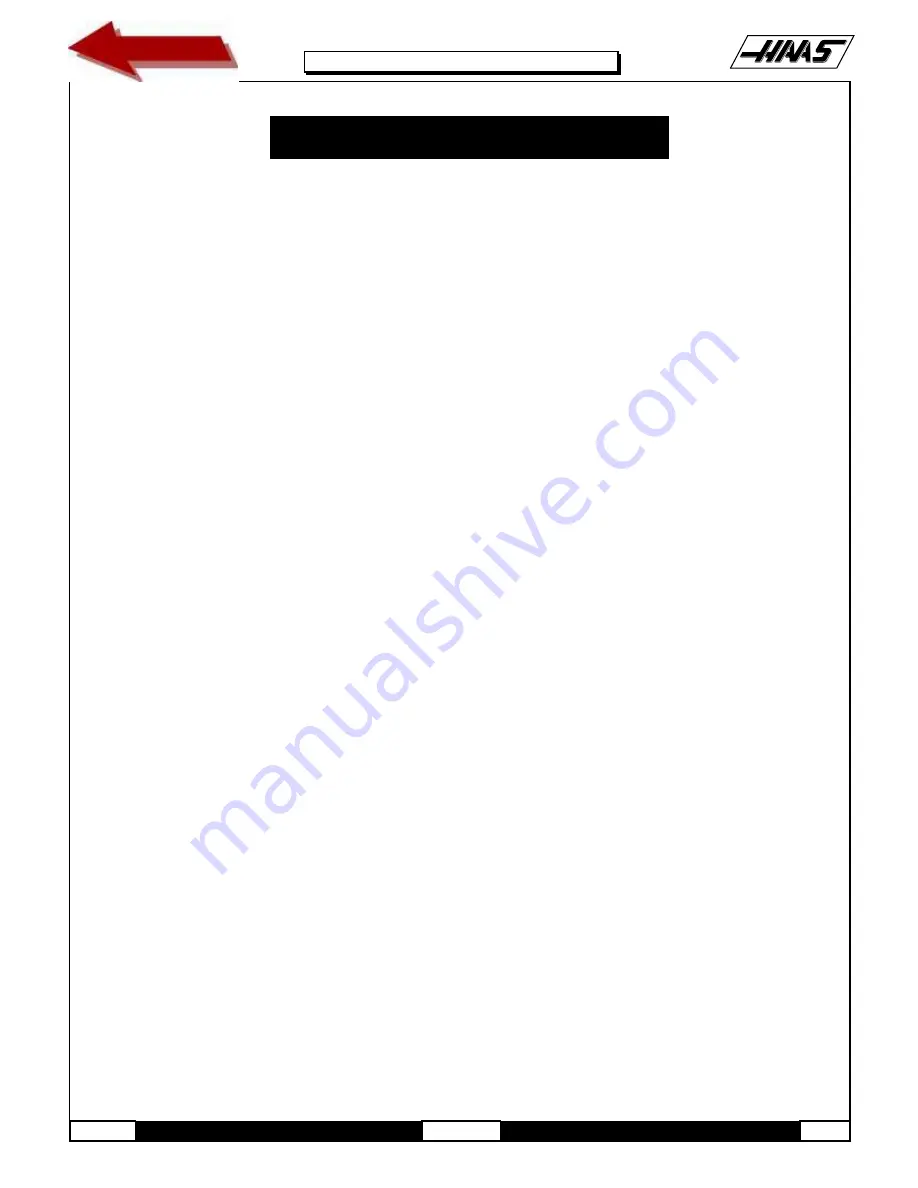
1-15-96
96-8100
1
TABLE OF CONTENTS
HAAS
AUTOMATION, INC.
TROUBLESHOOTING
S E R V I C E M A N U A L
VF-S
ERIES
TROUBLESHOOTING
This section is intended for use in determining the solution to a known problem. Solutions given are intended to give the
individual servicing the CNC a pattern to follow in, first, determining the problems source and, second, solving the problem.
The troubleshooting tips are organized in this section according to the area of the CNC that may be giving sign of a problem.
(Ex.: Out-of round circles in drilling will be found under the heading General Machine Operation - Accuracy).
If the problem you are experiencing cannot be found under the heading you expect, please try several other possible head-
ings. If the problem is still not found, contact Haas Automation for further details.
BEFORE YOU BEGIN:
USE COMMON SENSE
Many problems are easily overcome by correctly evaluating the situation. All machine operations are composed of a
program, tools, and tooling. You must look at all three before blaming one as the fault area. If a bored hole is chattering
because of an overextended boring bar, dont expect the machine to correct the fault. Dont suspect machine accuracy if the
vise bends the part. Dont claim hole mis-positioning if you dont first center-drill the hole.
FIND THE PROBLEM FIRST
Many mechanics tear into things before they understand the problem, hoping that it will appear as they go. We know this
from the fact that more than half of all warranty returned parts are in good working order. If the spindle doesnt turn,
remember that the spindle is connected to the gear box, which is connected to the spindle motor, which is driven by the
spindle drive, which is connected to the I/O BOARD, which is driven by the computer. The moral here is dont replace the
spindle drive if the belt is broken. Find the problem first; dont just replace the easiest part to get to.
DONT TINKER WITH THE MACHINE
There are hundreds of parameters, wires, switches, etc., that you can change in this machine. Dont start randomly changing
parts and parameters. Remember, there is a good chance that if you change something, you will incorrectly install it or break
something else in the process. Consider for a moment changing the processors board. First, you have to download all
parameters, remove a dozen connectors, replace the board, reload and reconnect, and if you make one mistake or bend one
tiny pin it WONT WORK. You always need to consider the risk of accidentally damaging the machine anytime you work on
it. It is cheap insurance to double-check a suspect part before physically changing it. The less work you do on the machine
the better.
Summary of Contents for VF-SERIES
Page 180: ...1 15 96 96 8100 177 TABLEOFCONTENTS TECHNICAL REFERENCE SERVICE M A N U A L VF SERIES ...
Page 235: ...96 8100 1 15 96 232 VF SERIES S E R V I C E M A N U A L ASSEMBLY DRAWINGS VF 1 COLUMN ...
Page 237: ...96 8100 1 15 96 234 VF SERIES S E R V I C E M A N U A L ASSEMBLY DRAWINGS VF 1 LEADSCREW ...
Page 239: ...96 8100 1 15 96 236 VF SERIES S E R V I C E M A N U A L ASSEMBLY DRAWINGS VF 3 COLUMN ...
Page 241: ...96 8100 1 15 96 238 VF SERIES S E R V I C E M A N U A L ASSEMBLY DRAWINGS VF 3 LEADSCREW ...
Page 245: ...96 8100 1 15 96 242 VF SERIES S E R V I C E M A N U A L ASSEMBLY DRAWINGS 3 4 2 1 ...