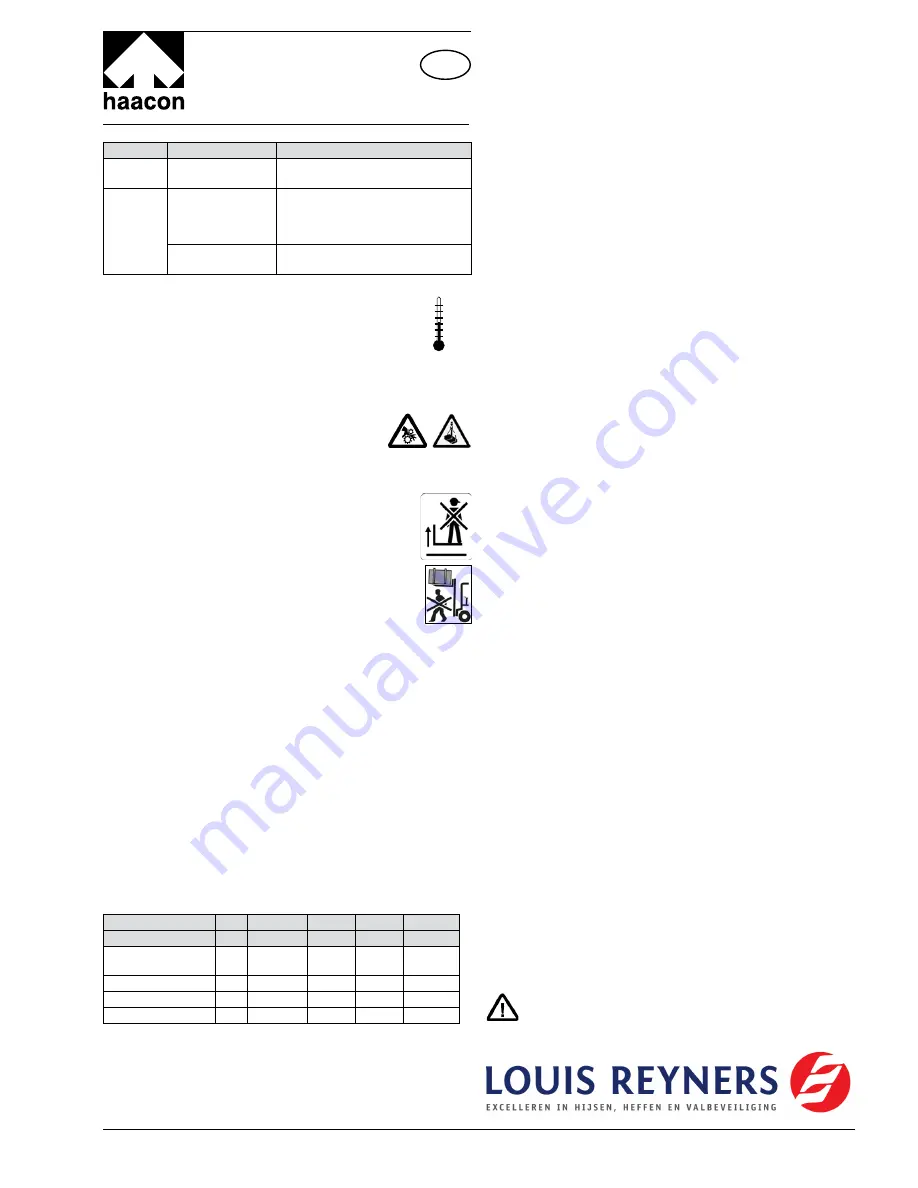
1
OPERATING INSTRUCTIONS
(Translation)
Rack & Pinion Jack
Typ(e) 1624.1,5 1624.3 1624.5 1624.10
1685.1,5 1685.3 1685.5 1685.10
1156 1659 6152
1. User groUps
Duties
Qualifications
Operator
Operation,
visual inspection
Instruction by means of the operat-
ing instructions; authorised person 1
Specialist
personnel
Assembly,
disassembly,
repair, mainte-
nance
Mechanic
Tests
Authorised person 2 per TRBS-1203
(Technical expert)
2. sAFeTY INsTrUCTIoNs
Where to use this winch
Operate the equipment in accordance with the information in
these operating instructions.
– Only use when in perfect working order.
– Only operate by trained personnel.
– Only use for the recommended application (i.e. pulling or pushing).
– To be fixed with securing pin in the final position when used for winde-
ning or lengthening load surfaces.
safe working practices
– First read the operating instructions!
– Always be conscious of safety and hazards when
working.
– Observe lifting device and load during all movements.
– Report damage and deficiencies on the equipment immediately to
the person responsible.
– Repair equipment first before continuing work!
– Do not leave the load suspended without supervision.
– Transport device protected against impacts and shocks,
falling over or toppling.
The following are not allowed:
– Overload (--> technical data, type plate, payload plate)
– Mechanical propulsion.
– Impacts, blows.
exclusions on use
– Not suitable for permanent operation and vibration stress.
– Not approved for use as builders' hoist (DGUV-R 100-500-2.30).
– Not approved for use in explosive areas/environments.
– Not suitable for aggressive environments.
– Not suitable for lifting hazardous loads.
organisational measures
– Ensure that these operating instructions are always at hand.
– Ensure that only trained personnel work with the equipment.
– Check at regular intervals whether it is being used in a safety and
hazard conscious manner.
Installation, service and repair
Only by specialist personnel!
Only use original spare parts for repairs.
Do not modify or alter safety-relevant parts!
Additional attachments must not impact safety.
Further regulations to be observed are:
– German Industrial Health and Safety Ordinance (BetrSichV).
– Country-specific regulations.
– German Accident prevention regulations (DGUV-V 54).
3. TeCHNICAL DATA
Type
1624.1,5 1624.3 1624.5 1624.10
Type
1685.1,5 1685.3 1685.5 1685.10
Permitted load
pulling / pushing*
t
1,5
3
5
10
Lift per crank turn
mm
13,9
8
3,9
4
Crank force
N
220
240
210
360
Weight (lift 800 mm)
kg
15
25
35
58
haacon policy is one of continuous development. We reserve the right to
amend specifications without notice or obligation.
*It is possible that the admissible load is reduced for different types.
The permitted load on the identification plate is valid.
For other versions the indications on the attached drawings and on the
serial number plate are valid.
4. geNerAL
These high quality rack & pinion jacks, produced for decades, are ro-
bust and reliable. They are capable of producing lifting, pulling, shifting
and pushing forces from 1,5 to 10 tonnes. Suitable for safe adjustment
of belt conveyors to any level and widening/lengthening of load bearing
surfaces.
5. CoNsTrUCTIoN
These rack & pinion jacks are a derivative of haacon‘s proven rack jack
range, type 11.1,5 - 11.10. Spur gear in special steel, hardened or tem-
pered. Gear mechanism of this rack jack range complies with German
BGV D8 safety regulations for lifting and pulling equipment.
The rack jacks are available with either „SIKU“ safety cranks or „RAKU“
ratchet cranks.
sIKU
= Safety crank with self-acting friction type load brake with
two-part spring loaded detent lever secures the load at any height. By
rotating the crank clockwise the load is lifted and vice versa.
Double acting locking device
If the rack and pinion jack is designed for pulling and pushing, it will be
fitted with a double acting locking device. The crank, chain wheel, etc.
for the manual operation can be fixed at this locking device.
6. INsTALLATIoN
Fix the rack and pinion jack securely to the drilled holes of the toothed
rack and the housing, or to the drilled mounting holes, corresponding to
the operating conditions.
7. operATIoN
For use as a lifting device
Unfold the crank handle. Turn crank clockwise to lift the load. To lower
the load, turn crank anti-clockwise.
If the crank is not turned the load is suspended safely.
For extending or retracting load surfaces
The load is moved by rotating the crank clockwise or anti-clockwise.
The extended or retracted parts must be fixed in the desired position
with securing pins.
Use of rack & pinion jacks without brake:
Only shift in horizontal direction.
Do not move loads on inclined levels. Do not lift loads.
8. TesTINg
The equipment must be checked in accordance with the conditions of
use and the operating conditions at least once per year by an authorised
person 2 per TRBS 1203 (Technical expert) (testing per BetrSichV, §10,
sect. 2 represents implementation of the EC guidelines 89/391/EEC and
2009/104/EC or the annual occupational safety inspection per DGUV-V
54, §23, sect. 2 and DGUV-G 309-007). These checks must be docu-
mented:
– Before commissioning.
– After significant alterations before recommissioning.
– At least once per year.
– In the event of unusual occurrences arising that could have detrimen-
tal effects on the safety of the winch (extraordinary tests, e.g. after a
long period of inactivity, accidents, natural events).
– After repair works that could have an influence on the safety of the
winch.
Technical experts (AP2) are persons, who have sufficient knowledge
based on their education and experience, in the areas of winches, lift
and pull systems and the relevant official occupational health and safety
rules, accident prevention regulations, guidelines and generally ac-
cepted engineering rules (e.g EN standards), to evaluate the opera-
tional safety of winches, lift and pull systems. Technical experts (AP2)
are to be nominated by the operator of the equipment. The implementa-
tion of the annual occupational safety inspection as well as the training
to obtain the aforementioned knowledge and skills can be provided by
haacon hebetechnik.
9. MAINTeNANCe reCoMMeNDATIoNs
The operator determines the intervals themselves based on frequency
of use and the operating conditions.
– Regular cleaning, no steam jets!
– Carry out visual check on inaccessible brakes / locks every 5 years at
the latest, replace brake pads as required.
– General overhaul by the manufacturer after 10 years at the latest.
ATTeNTIoN!
Inspection, maintenance and repair works only on an unloaded
hoist. Work on brakes and locks only by qualified specialist
personnel.
gB
-
20° C
+50° C
Louis Reyners BV
|
Symon Spiersweg 13a, 1506 RZ Zaandam
|
+
31 (0) 75 650 47 50
|
|
www.LR.nl
Summary of Contents for 1624.1,5
Page 6: ...6 Louis Reyners BV Symon Spiersweg 13a 1506 RZ Zaandam 31 0 75 650 47 50 info lr nl www LR nl ...
Page 7: ...7 Louis Reyners BV Symon Spiersweg 13a 1506 RZ Zaandam 31 0 75 650 47 50 info lr nl www LR nl ...
Page 8: ...8 Louis Reyners BV Symon Spiersweg 13a 1506 RZ Zaandam 31 0 75 650 47 50 info lr nl www LR nl ...