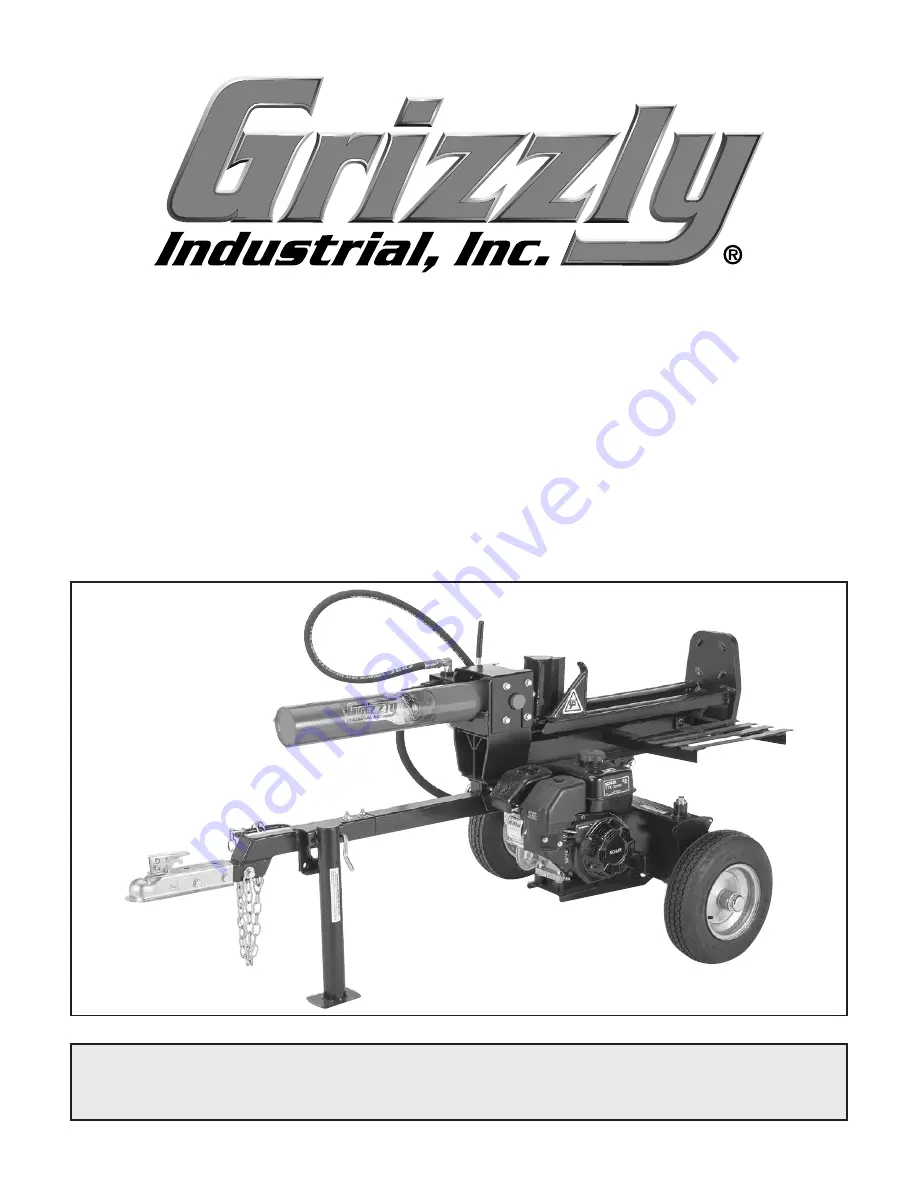
MODEL T27710
22-TON LOG SPLITTER
w/KOHLER ENGINE
OWNER'S MANUAL
(For models manufactured since 04/16)
COPYRIGHT © JUNE, 2016 BY GRIZZLY INDUSTRIAL, INC.
WARNING: NO PORTION OF THIS MANUAL MAY BE REPRODUCED IN ANY SHAPE
OR FORM WITHOUT THE WRITTEN APPROVAL OF GRIZZLY INDUSTRIAL, INC.
#BLWK18211 PRINTED IN CHINA
V1.06.16
Summary of Contents for T27710
Page 40: ...38 Model T27710 Mfd Since 04 16...
Page 44: ......
Page 45: ......
Page 46: ......
Page 47: ......
Page 48: ......
Page 49: ......
Page 50: ......
Page 51: ......
Page 52: ......
Page 53: ......
Page 54: ......
Page 55: ......
Page 56: ......
Page 57: ......
Page 58: ......
Page 59: ......
Page 60: ......
Page 61: ......
Page 62: ......
Page 115: ...53 18 690 01 Rev C KohlerEngines com...
Page 116: ...54 KohlerEngines com 18 690 01 Rev C...
Page 117: ...55 18 690 01 Rev C KohlerEngines com...
Page 118: ...56 KohlerEngines com 18 690 01 Rev C 2015 by Kohler Co All rights reserved...