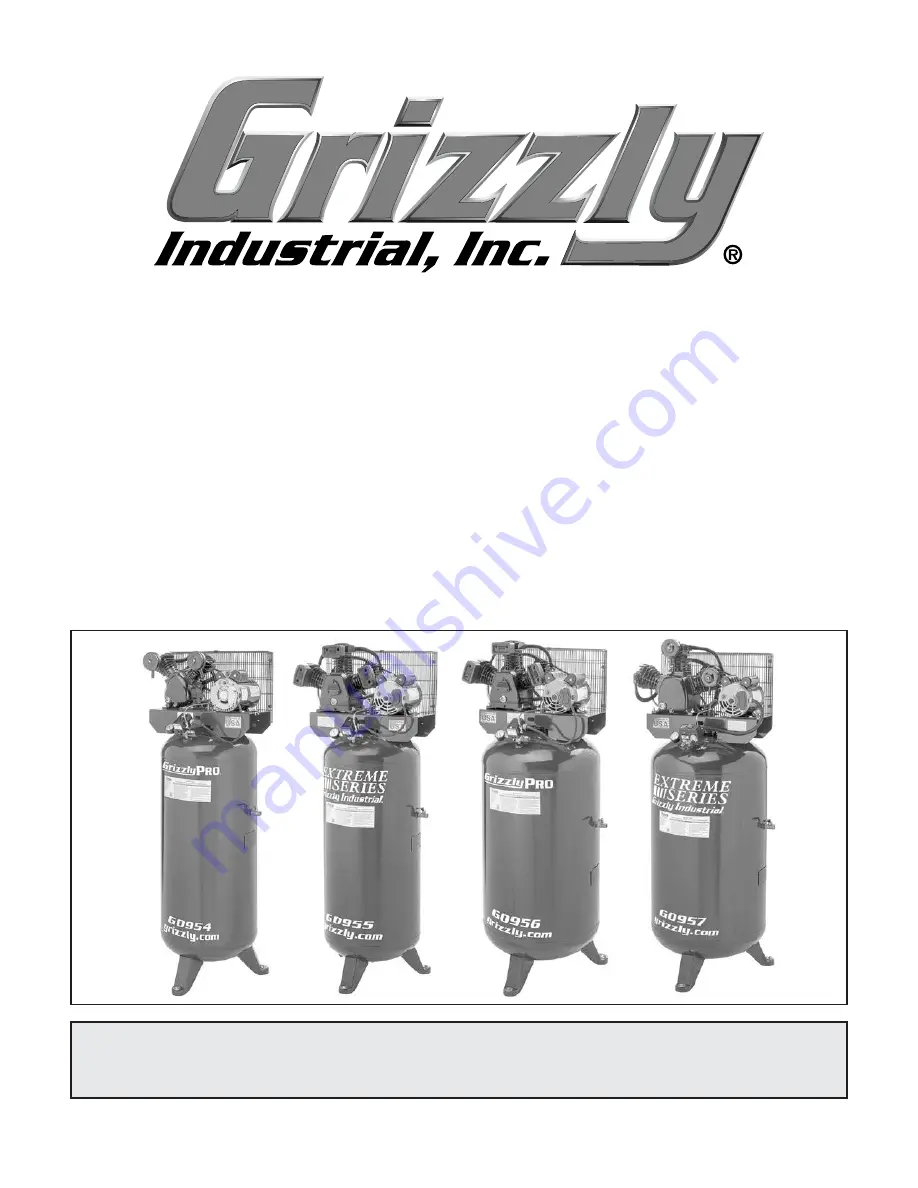
COPYRIGHT © NOVEMBER, 2022 BY GRIZZLY INDUSTRIAL, INC.
WARNING: NO PORTION OF THIS MANUAL MAY BE REPRODUCED IN ANY SHAPE
OR FORM WITHOUT THE WRITTEN APPROVAL OF GRIZZLY INDUSTRIAL, INC.
#CS22333 PRINTED IN USA
V1.11.22
MODEL G0954, G0955,
G0956, & G0957
STATIONARY AIR
COMPRESSORS
OWNER'S MANUAL
(For models manufactured since 11/21)
***Keep for Future Reference***
Summary of Contents for G0954
Page 64: ......